RPA can bring about a “virtual integration” of multiple systems while executing repetitive work more accurately and reliably than humans can.
Contributed by | Genpact
The field of Robotic Process Automation (RPA) has advanced significantly over the past few years, but prospective users need to look beyond the hype to apply this emerging technology effectively. By interacting with existing software systems at the level of the graphical user interface, RPA can bring about a “virtual integration” of multiple systems while executing repetitive work more accurately and reliably than humans can.
Getting past the hype
With all the hype about the advance of robotics, people can be forgiven for thinking that robots are on the verge of making humans redundant in their work environments. Consider, for example, this headline from the London Daily Mail: “Is 2014 the year YOUR job will be taken by a robot?” The term jobocalypse has even been coined to describe this anticipated revolution. It conjures up an image of mass displacement of human labor.
Certainly, Robotic Process Automation (RPA) has advanced significantly over the past few years, but there is no jobocalypse in sight. Experts see a different reality: While Rapid Automation (RA)—or, more simply, “robotics”—reduces the need for repetitive human effort, there are still distinct limitations to the types of work in which it can be applied.
In 2014, not many businesses had hundreds of people banging away at computers to do routine tasks. At Genpact, most of the processes we take on are fairly complex. Identifying the pieces that can be completely automated is the first step, but the bigger part of the job is to reorient the workforce around tasks that require judgment. When you take on an RPA project today, you’re changing the nature of the work; as such, you need to balance automation with decision-making ability.
RA solutions are helping to drive development of the Business Process Outsourcing (BPO) industry. Initially, the industry was based on labor arbitrage, scaling, sizing, offshoring, cost-cutting, and economies of scale, but it has evolved. Today, it delivers business impact by improving process quality, using concepts like Six Sigma. The third phase that we’re seeing now is focused on emerging technologies like RPA, mobility, cloud, big data, and advanced visualization. When these elements are used in combination, they help improve efficiency by providing a new layer of engagement to the client environment.
When applied with this systematic approach, robotic automation offers considerable potential for addressing key pain points in traditional “system of records” technologies, such as Enterprise Resource Planning (ERP). Still, there are limitations to the usability and impact of robots. Prospective users need to recognize which types of transactions can be performed well by robots, identify the appropriate sphere of intervention, and form effective plans for using RPA in a rapidly changing environment.
Robotic automation today
RA differs from more direct types of automation. It interacts with different software systems at the level of the graphical user interface or presentation layer: The same level as a human user of the system. Existing systems can therefore work together more efficiently, because RA performs some tasks faster and more reliably than humans do. This shifts human effort away from routine processing functions and toward managing exceptions and optimizing business processes. One principal advantage is that RA links existing systems without requiring their direct integration. Instead, it applies a variety of familiar user interfaces, such as ERP systems and Microsoft Office documents and databases. Today’s RA systems are more accurate and flexible than employees are; they improve security and compliance, and are available 24/7.
While it’s critical to identify which processes are the best candidates for RA, robotics should be seen as just one component of end-to-end process improvement. At Genpact, we’ve found that RA can be the inflection point that leads to the automation of other parts of the process. To get the maximum value of RA, the natural place to start is with the global process owner, or the person with overall responsibility for an end-to-end process.
The future of robotic automation
As robotic automation matures, three principal factors will drive business impact:
-
Utility. Robotics work effectively in high-demand, highly-scalable applications. These are often situations in which manual processes would involve considerable training and organization for short-term projects. To quickly mobilize RA solutions, the organization first needs to establish capacity. This means making long-term investments rather than addressing applications on a case-by-case basis.
-
Cognitive capabilities. Business models are becoming more sophisticated, with enterprises focusing on customer needs and outcomes rather than products. In this setting, automation algorithms need to work the way humans think, using natural language and learning from experience.
-
Technology partnerships. An ecosystem of expertise has to be in place to exploit diverse technologies, encompassing elements like big data, cloud, and machine learning.
Pulling all of this together requires cutting across traditional boundaries, and ideally uses an end- to-end holistic approach. The key is to automate intelligently while balancing automated and human processes. This calls for an increased reliance on management by exception, which in turn requires strong governance and compliance check points.
Using robotics strategically
Through Genpact’s experience in developing and delivering RA solutions that generate business impact, we have identified the types of processes where robotics work most effectively. We started by estimating an “R Factor” for each process: The percentage of activity that is clearly repetitive, but also deterministic. In other words, it’s not just repetition, but also other conditions that make a process a good target for RA. These include having relatively clean data and well laid out rules. Ideal cases contain the following:
-
Dual data entry, where information must be input manually more than once, such as into a workflow process and then an ERP system.
-
Straight-through processing, where inputs from different sources (such as sales orders) need to be integrated.
-
Similar data extraction requests, from multiple users from the same database.
-
Routine decision-making, where conditions for referral to managers are unambiguous, such as the payment of invoices.
In cases like these, RA can achieve "virtual integration" among systems that normally don’t "talk" to each other by connecting them at the user interface level. Depending on the process’s degree of suitability, this can boost productivity by 10% to 50%. Other payoffs include increased accuracy, more flexibility, improved compliance, and 24/7 availability. What’s more, RA offers the additional benefit of collecting metadata from multiple sources and enabling downstream analytics that can garner insights and actually make operations more intelligent.
In the end, robotic automation is no panacea, and significant limitations still exist—especially regarding data formats and natural language processing. RA is continuously evolving and improving in areas like non-digital input types, machine learning, and natural language. The reality we face today is that RPA needs to be addressed as part of a broad briefcase of tools. The use of these tools must be balanced with more direct forms of automation to get the best mix, thereby achieving maximum impact on the overall agility of the business to respond to challenging shifts in its environment.
Genpact (NYSE: G) stands for “generating business impact.” We design, transform, and run intelligent business operations including those that are complex and specific to a set of chosen industries. The result is advanced operating models that foster growth and manage cost, risk, and compliance across a range of functions such as finance and procurement, financial services account servicing, claims management, regulatory affairs, and industrial asset optimization. Our Smart Enterprise Processes (SEP SM ) proprietary framework integrates effective technology and data-driven insight into the fabric of enterprise processes to help our clients be more competitive. Our hundreds of long- term clients include more than one-fourth of the Fortune Global 500. We have rapidly grown to over 66,000 people in 25 countries with key management and corporate offices in New York City, but our global critical mass doesn’t dilute our flexible and collaborative approach and our management team still drives client partnerships personally. Our clients attribute much of our success to our unique history – behind our passion for process and operational excellence is the Lean and Six Sigma heritage of a former General Electric division that has served GE businesses for more than 16 years.
The content & opinions in this article are the author’s and do not necessarily represent the views of ManufacturingTomorrow
Comments (0)
This post does not have any comments. Be the first to leave a comment below.
Featured Product
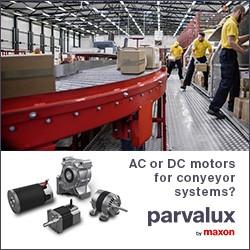