The Internet of Things (IoT) is enabling manufacturers to be more efficient, productive and profitable in the face of increased competition worldwide. We look at five reasons why manufacturers are betting big on these new technologies.
Doug Drinkwater | Internet of Business
The Internet of Things (IoT) is enabling manufacturers to be more efficient, productive and profitable in the face of increased competition worldwide. We look at five reasons why manufacturers are betting big on these new technologies.
Productivity
Productivity is arguably the main driver of IoT in manufacturing, as companies recognise that the sensors and collected data enable them to be more efficient, minimising loss and waste, and making their workers’ more effective.
Trumpf is one of the manufacturers to have taken the plunge with IoT, harnessing C-Labs’ IoT software to connect equipment on the manufacturing floor at multiple locations with enterprise applications and systems running on corporate IT networks.
Ultimately, manufacturers are convinced IoT can reduce downtime, boost savings and produce more goods, more accurately and with less waste.
New revenue streams
IoT offers manufacturers the chance to drive bigger revenues, not only by being more efficient and saving costs, but also by making intelligent and expensive products.
Konecranes is a good example of this. The Finnish firm has been selling intelligent cranes and reinventing itself as a services company. These ‘intelligent’ cranes are more expensive, but have more features too. They’re able to let the operator know (via sensors) its last known condition, how often it’s used, if it’s overused, improperly used and when it is likely to break down.
Operational savings
The one thing that is going to get your C-level executives on-board with any IoT strategy is the ability to save or make money, and this is certainly the case with manufacturing.
Through the use of sensors on the manufacturing floor, on-site managers can reduce downtime through predictive maintenance, there’s less waste (you make exactly what you need), and staff are working on the things you want them to work on.
Reduced downtime
Predictive maintenance is knowing when machinery is going to break down and fixing it before it does. And this is already a huge boost on reducing downtime, ensuring that operations are smooth and that repairs are done before equipment goes wrong.
TVH Group has a good case study on this, and many more will surely follow in future.
Keeping up with the competition
European manufacturers face a battle against their “low-cost” Asian competitors, but with IoT helping on all of the above matters, the war can still be won through leaner and meaner operations.
The German government has recognised this, and through Industrie 4.0 is trying to help German industrial manufacturing – the backbone of Europe’s largest economy – to keep its competitive edge against labour-cost advantages of developing countries and a resurgence in U.S. manufacturing.
During the next five to ten years, Industrie 4.0 is expected to boost productivity across all German manufacturing sectors by €90 billion to €150 billion. Productivity improvements on conversion costs will range from 15 to 25 percent. When the materials costs are factored in, productivity gains of 5 to 8 percent will be achieved.
Cost benefits like these can only help European manufacturers compete with global competitors.
About Internet of Business
Demystifying IoT in manufacturing and explain the connected world.
The Internet of Manufacturing conference will feature ten in-depth case studies focusing on how companies such as Konecranes are revolutionising manufacturing through IoT
The content & opinions in this article are the author’s and do not necessarily represent the views of ManufacturingTomorrow
Comments (0)
This post does not have any comments. Be the first to leave a comment below.
Featured Product
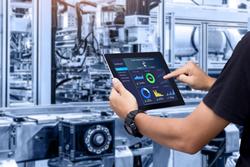