Network connectivity of industrial equipment and devices is a vital element of Industry 4.0. If the connection fails, all data communication from field devices to back-end servers and cloud networks will be halted, disrupting the operation of Industry 4.0.
Industry 4.0-based Network Manager Ensures Solid Industrial Connectivity
Contributed by | Nexcom
With the hot topics of Industry 4.0, Industrial Internet of Things (IIoT), intelligent automation and so forth emerging into the market, factory machines and equipment will become connected to upload field data to back-end servers or cloud networks. Network factors such as network architecture, network backbone and machine connectivity will require meticulous management.
Network connectivity of industrial equipment and devices is a vital element of Industry 4.0. If the connection fails, all data communication from field devices to back-end servers and cloud networks will be halted, disrupting the operation of Industry 4.0. Although network connectivity is crucial and requires strict management, it is not always clear on whether it should be managed by information technology (IT) or operational technology (OT) personnel.
Normally, staff from the management information system (MIS) department are the ones most proficient in data communication technology throughout an enterprise, and are usually given the role of managing the networking of industrial devices and equipment. However, MIS staffs in the past have mostly worked with network switches, wireless access points, virtual private network (VPN) configuration, firewall devices and so forth. To venture into the new realm of field device management as well as effectively manage both networking and industrial field devices to maintain optimal operation and connection present a great barrier for MIS staffs to overcome.
Field Devices Require Monitoring Also, Not Just the Network Devices
YC Cheng, Assistant Vice President of NEXCOM’s IoT Automation Solutions Business Group, states that although managing industrial devices will bring great challenges to MIS, it should not be overlooked. Rather, the "Network Management" aspect of MIS should be integrated with industrial elements, transforming it into "Network & Device Management" to take on the challenges with full force. For example, control systems today are gradually adopting PC-based control architecture, and the key to stable operation of these controllers lies in reliable control system hardware. A constant attention to the usage of the processor, memory and hard drive in detail is required to ensure ongoing operation and connectivity, showing that field device monitoring is of equal importance to network management.
Cheng points out that field device communication not only involves a wide range of different protocol standards, but also a wide range of custom-developed vendor-specific protocols. For MIS staffs who are unfamiliar with such protocols, a unified management platform that consolidates all the protocol data and depicts the information in an intuitive diagram with easy-to-understand language can assist MIS in the management of the network and devices.
With this in mind, NEXCOM has released the I4.0 network management tool "nCare Node and Network Health Management Solution". nCare includes a number of key features to facilitate management. First, nCare offers a visualized display of the network topology to give MIS a clear view of the entire network and the connection paths of all the devices. To make administration easier, nCare also integrates map services to show the geographic location of each device. Under normal conditions, the network and device connection links in the visual diagram will be displayed in green. In events of abnormal conditions such as connection retries or connection failure, yellow or red will be displayed respectively to allow MIS to quickly identify the root cause of the error and take appropriate corrective measures.
Improved MIS through Visual Topology & Active Notifications
Cheng further adds that the visual topology can also aid the MIS in overseeing the number of production equipment added to or removed from the field. When used in conjunction with whitelist security, any connection from unknown devices such as unauthorized wireless access points can be detected and blocked immediately.
Second, nCare can help MIS detect and monitor the health status of field devices. To enhance the detection capacity, nCare features built-in support for Modbus TCP/RTU communication, Windows Management Instrumentation and even NEXCOM's exclusive Xcare management software. In addition, for field devices that use vendor proprietary protocols such as automatic guided vehicles (AGV), nCare can be customized to support them by translating the protocols into Modbus format, integrating seamlessly into the nCare network management mechanism.
Third, nCare includes a built-in active notification system. Managers can configure notification events to be sent through email or instant messages in real-time, notifying the situation to ensure appropriate measures can be taken accordingly based on the severity of the event. In other words, MIS staff can monitor the status of the network and field devices in real-time and at anytime on mobile devices, easily fulfilling the predictive maintenance concept envisioned by Industry 4.0.
Another noteworthy feature that nCare includes is the "time-reversal backtracking" mechanism. This feature is designed to help MIS staffs locate the exact detail of a particular event in log files for troubleshooting. Compared to finding a needle in a haystack like in the past for traditional log file search, nCare's time-reversal backtracking significantly improves troubleshooting efficiency.
In addition, nCare provides regular reports to help enterprises identify the availability rate of field devices; it also provides enterprises the ability to configure network and field device settings, as well as the encryption settings for each wireless access points to ensure added security. Besides supporting NEXCOM devices, nCare also provides management support for SNMP-compatible devices from other vendors to guarantee a secure investment for customers.
Lastly, nCare features an open standard architecture, supports AAA security authentication and provides seamless integration support for ERP systems and SCADA automation systems to maximize the efficiency of the complete solution. Implementation for both local and virtual machines as well as on the cloud is also supported for flexibility and easy future expansion.
NEXCOM
NEXCOM PC-based Factory Automation solution is perfect for Industry 4.0 system requirements. It contains Industrial Fieldbus Computers, Fieldbus MiniPCIe Modules, and DIN-Rain Computers capable of providing higher computing capability for complex control/management purposes and provides rich communication interface for IT system integration. Users can implement the solution into new or existing systems without any gaps and is fully compatible with Siemens/Allen-Bradley and Beckhoff systems.
The content & opinions in this article are the author’s and do not necessarily represent the views of ManufacturingTomorrow
Comments (0)
This post does not have any comments. Be the first to leave a comment below.
Featured Product
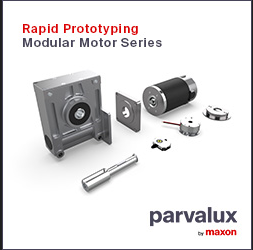