If youve found yourself running out of space within your current facility, automated storage could be the solution youre looking for. With an AS/RS, you have the option to increase storage volume by retrofitting or expanding your current facility which may be less expensive than investing in a new facility.
How To Determine If An AS/RS ( Automated Storage and Retrieval System) Fits Your Facility
John Hinchey | Westfalia Technologies, Inc.
The Material Handling Institute (MHI) defines five characteristics of an automated factory or distribution center: data automation, networking controls for connected equipment, production automation, flexibility and automated material handling. An automated storage and retrieval system (AS/RS) can be categorized into both production automation, and of course, automated material handling.
Retrofitting your warehouse with an AS/RS can be an expensive undertaking, so before fully committing to automation, you must ensure that you will receive the expected return on your investment (ROI). There is no magic formula for implementing an AS/RS. However, the process will go much smoother if you take the following factors into consideration prior to making your decision and designing a customized automated solution for your warehouse.
Current and Projected Operational Growth
An in-depth evaluation of your current operations must be performed before considering whether or not to implement warehouse automation. While the upfront cost of an AS/RS may not seem justified, before completely discounting warehouse automation, you must first consider your company’s long-term growth plans. Doing so will help determine where your company is headed for the future and if an automated solution is right for you. It is also important to note that an AS/RS has a 25+ year life cycle with typical ROI being achieved in three to five years. With that being said, you can see annual benefits, such as labor reductions, smaller footprint and higher customer service levels much earlier.
Available Space
If you’ve found yourself running out of space within your current facility, automated storage could be the solution you’re looking for. With an AS/RS, you have the option to increase storage volume by retrofitting or expanding your current facility which may be less expensive than investing in a new facility. An AS/RS can increase the storage capacity of your existing facility by taking advantage of the available vertical space. This will not only allow you to store more product but will also eliminate the need for a new, larger building.
An AS/RS has the ability to store pallets single-, double- or multiple-deep to increase storage density. Some systems are even able to store pallets up to 18-deep, and retrieve them efficiently with specialized material handling equipment that can access the rack from either side. This type of high-density storage translates into a smaller building footprint which reduces the impact on the environment.
Pallet Velocity
Pallet velocity refers to how fast your pallets move in and out of your warehouse. By calculating the number of inbound and outbound orders you move during peak operation times, you can determine the number of storage and retrieval machines (S/RM) necessary to efficiently handle SKU volume.
Operating Hours
If your warehouse is only operating one or two shifts a day, you might be able to achieve the throughput you need by adding an extra shift. However, you also need to consider whether or not you have adequate staging space for incoming and outgoing materials waiting for pickup or putaway. Conversely, if you’re currently running three shifts and are still struggling, adding an AS/RS can help save on labor costs and make better use of current warehouse space.
In a conventional system, throughput determines the staffing levels and number of fork trucks required. But in an automated system, throughput determines the number of S/RMs needed within the AS/RS. A single S/RM is typically capable of handling between 60 and 70 unit loads per hour when handling one load at a time.
Special Storage Needs
Even if your product requires temperature-controlled storage, an AS/RS is the way to go. The human body is not designed to constantly work in extreme temperatures, but an automated system can accommodate these unique storage needs. One advantage of implementing an AS/RS versus conventional storage is it can operate in a wide range of temperatures — often from -35 degrees to as high as 110 degrees Fahrenheit.
Products that require LIFO (last in, first out) or FIFO (first in, first out) handling are ideally suited for AS/RS because you can customize your solution to pick pallets in the required order. If freshness or expiration needs to be maintained, you can also ensure that pallets are picked in the order that maximizes freshness and minimizes spoilage or obsolescence.
Integration
Integration with warehouse control system (WCS) or warehouse management system (WMS) software is critical for ensuring optimum efficiency and throughput when using an AS/RS. Companies considering automation for their warehouse should also consider how the AS/RS will integrate with their existing WMS software. For those companies with an existing WMS who are looking to introduce a WCS to assist in automation, should consider opting for a warehouse execution system (WES) instead. This will allow the company to use their familiar WMS, integrate it with the new WES and “turn on” the WCS functionality once automation is introduced. Working with an experienced software vendor will help to minimize the cost of startup and ensure efficient integration with your new AS/RS.
A Partner or a Vendor
Finally, an often-overlooked aspect of AS/RS implementation is the reputation of the automation supplier. Look for a company that will take the time to understand your individual business needs, products, future growth plans and space requirements. The ideal supplier will have an experienced team that can provide you with the right solution for your specific needs.
About John Hinchey
John Hinchey is Vice President of Sales at Westfalia Technologies, Inc., a leading provider of logistics solutions for plants, warehouses and distribution centers in the Americas.
The content & opinions in this article are the author’s and do not necessarily represent the views of ManufacturingTomorrow
Comments (0)
This post does not have any comments. Be the first to leave a comment below.
Featured Product
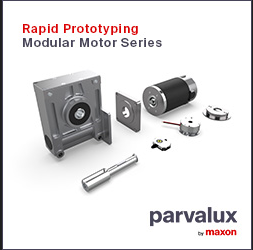