Promess became involved with the battery manufacturer when the hydraulic presses, originally specified for both the pressing and assembly operations, proved to be unable to deliver the level of consistent process control required.
Electro-Mechanical Assembly Press Technology Moves Li-Ion Battery Manufacturer A Step Closer To Perfection
Contributed by | Promess
Lithium ion (Li-Ion) batteries are the technology of choice for applications ranging from handheld electronics to “plug-and-drive” vehicles, as well as back-up power systems used by “server farms” and other critical systems. Their performance characteristics are the result of a very delicately balanced set of chemical, electrical, and physical parameters. All of these factors combined can make manufacturing a challenge for the whole range of Li-Ion sizes, especially at the larger end of the product range.
Large Li-Ion battery packs are composed of individual cells, each of which contains a pair of compacted Lithium Ion powder pellets separated by a collector plate. The pellets, which are composed of proprietary mixtures of Lithium and other elements, must be as identical as possible in terms of size, shape, density and composition. Any variation will negatively impact the chemical and electrical properties of the cell and ultimately shorten the life of the battery.
Once manufactured, the pellets must be joined to the collector in an manner that maintains not only their “in process” characteristics, but also creates a perfectly balanced cell with the collector exactly centered between the pellets, as any variation in the cell’s balanced geometry may also reduce battery life and overall quality.
Large Li-Ion batteries are supplied by a major battery manufacturer to customers in the energy supply industry. The batteries are an integral part of the customer’s product that places a high premium on a long, and even more important, predictable service life.
Promess became involved with the battery manufacturer when the hydraulic presses, originally specified for both the pressing and assembly operations, proved to be unable to deliver the level of consistent process control required. Working closely, with Promess’ Applications Engineering Group, the manufacturer developed a two-step process utilizing the control and repeatability of a Promess 20kN EMAP press system to pre-form the pellets with a force accuracy of +/-.5%. They then use four 300kN Promess EMAP press systems to bond the pellets to the collector maintaining a positional accuracy of +/- 25 microns using the encoder in the servo motor.
The Promess EMAP is a servo controlled, ball screw driven press equipped with a load cell to measure force and an encoder based servo motor to measure distance, with the capability to add any number of other sensors which may be necessary for a particular assembly process. The Promess EMAP is capable of applying force and distance with extreme precision while measuring the functional result and feeding that data back into the control system.
The EMAP system uses the Promess MotionPRO Software to provide closed loop feedback and control that allows 100% in-process differential monitoring. Moreover, the force and position feedback signals can be processed by the Promess MotionPRO controller to provide a graphic “signature” of each cycle.
Not only can the signature of each cycle be compared to a known good signature to measure the consistency of the process, but the signatures also offer insight into variations in the characteristics of the raw materials being used. For example, if the grain size or compaction characteristics of the raw Lithium ion powder vary from lot to lot, this difference would be evident in the signatures of the pressing operation. This same benefit of signature comparison can be applied to any variation in any set of gauged characteristics.
Once gauged and assessed, the process parameters can be modified to accommodate the lot-to-lot variations, or the powder can be modified to match the original specifications. Either way, the ability to monitor the time/force/distance parameters of each press stroke allows the manufacturer to effectively “clone” each pellet and to ensure that each assembly comes as close as possible to achieving the goal of perfection.
The content & opinions in this article are the author’s and do not necessarily represent the views of ManufacturingTomorrow
Comments (0)
This post does not have any comments. Be the first to leave a comment below.
Featured Product
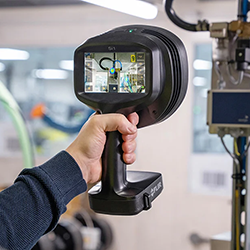