For entry level manufacturing positions, higher education is not normally required. Instead, a personal and commercial drivers license, and special certifications such as an Occupational Safety & Health Administration Certification, Food Safety Program education, and HAZMAT endorsement, can make a candidate more qualified when applying to manufacturing jobs.
Hot Jobs Study Reports Manufacturing a Top Industry
Greg Dyer | Randstad Commercial Staffing
What are the hottest jobs in Manufacturing in 2017?
The hottest jobs in Manufacturing in 2017 are production supervisor, maintenance mechanic, driver, machine operator and warehouse supervisor. The field also has some of the top temporary positions including loader/unloader, assembler, general production worker, and forklift operator.
How were the jobs determined to be the most in-demand and emerging jobs?
We worked with our national recruiting experts to collect data to determine the most in demand jobs over the next year. Our team reviewed the current workforce trends, including available positions, number of qualified candidates, market growth, salary range and specific skillsets. After considering these factors we were able to anticipate the most in demand jobs and where there will be job growth in industries such as engineering, finance and accounting, human resources, information technology, life sciences, manufacturing, and office and administration.
With regards to manufacturing, new technology, innovative production systems, a growing preference for American-made goods and a decline in offshoring are transforming U.S. manufacturing. There is an increased demand for technology-savvy workers to not only capitalize on the next industrial revolution, but to fill a critical void left behind by retiring workers. Job seekers with previous experience, higher education, technological know-how or training will have a competitive edge
How does the manufacturing industry compare to other hot industries in terms of growth, job availability, and candidate pools?
While manufacturing continues to expand, the commonality to many other hot industries is the need for talent that understand both traditional hardware and equipment as well as software and programming as advanced technologies and automation continue to grow. The need for higher skilled candidates has created talent shortages in many segments and markets. While not extremely high, manufacturing has a higher unemployment rate of 6.3% compared to the general national average of 4.7%.
How about wages, how do they compare with other hot industries and what ranges are common?
Salaries for manufacturing positions range anywhere from $37,000 to $55,350 a year. Compared to other industries, manufacturing wages are higher than administrative and office work, and only slightly lower than life science salaries. Wages will continue to increase over the coming months and years given the skilled talent shortages and need for higher skills.
What additional training or education should people looking for manufacturing jobs get to be the most competitive?
For entry level manufacturing positions, higher education is not normally required. Instead, a personal and commercial driver’s license, and special certifications such as an Occupational Safety & Health Administration Certification, Food Safety Program education, and HAZMAT endorsement, can make a candidate more qualified when applying to manufacturing jobs. For higher skilled jobs, systems automation and robotics training and education will give candidates the edge.
What do employers need to know to best position themselves to remain competitive in hiring the best manufacturing candidates?
The manufacturing industry has a lot of emerging jobs, and existing jobs are also growing, but at this point the industry still has a relatively smaller number of positions and a higher unemployment rate than other industries. HR professionals in the manufacturing industry need to be sure they are reaching the right demographics with their job postings to best match candidates with open positions and be willing to pay appropriate wages to attract and retain the best talent for their organizations.
The buzz around robots taking away manufacturing jobs is front page news. How can an individual protect him/herself and his/her future from being replaced by a robot in the manufacturing industry?
In the last month the U.S. gained 5,000 manufacturing jobs and there is always a need for specific jobs that robots don’t have the ability to fulfill. From 2015 to 2016, available jobs increased 1% for machine operators, 2% for production supervisors, and 64% for drivers. So although some manufacturing jobs are disappearing because of robotics and technology, the industry itself isn’t going anywhere. In fact, many organizations are seeing that robotics doesn’t replace the human but allows us to be more productive. In order to remain relevant and competitive in the manufacturing field, individuals need to pay attention to industry trends, and stay up-to-date on skills and certifications that may become necessary in evolving manufacturing jobs.

Greg leads Randstad's in-house services concept and enterprise strategic accounts team, where he is responsible for strategic commercial sales, client delivery and account management for many of Randstad's largest, most complex clients. Greg oversees a team of strategic account directors and in-house leaders and has a proven track record of establishing solid go-to-market strategies, setting and communicating clear vision and goals, and executing and delivering outstanding results in terms of growth and profitability. Under Greg's leadership, Randstad has significantly improved its strategic client delivery and fulfillment in many client staffing programs. Greg holds a bachelor’s degree in business management from The University of Tennessee at Chattanooga and an MBA in management from Brenau University.
The content & opinions in this article are the author’s and do not necessarily represent the views of ManufacturingTomorrow
Comments (0)
This post does not have any comments. Be the first to leave a comment below.
Featured Product
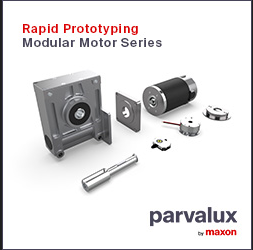