Machines can now communicate failure points and collect data that can be used to improve predictive and preventative maintenance, which in the long run improves uptime.
Smart Manufacturing in Plastic Injection Molding
Denny Scher | ICOMold
Smart Manufacturing is talked about quite a bit. It goes by other names, too, like the Internet of Things (IoT), Industrial IoT (IIoT), and Industry 4.0. The term IoT was first coined by Peter T. Lewis in 1985 to describe “the integration of people, processes, and technology with connectable devices and sensors to enable remote monitoring, status, manipulation, and evaluation of trends of such devices.”
So the term has been around for a while now, but the concept still continues to develop and evolve as technology continues to advance through new hardware like sensors, and through the collection and analysis of data. So, how have the advancements in smart manufacturing affected the plastic injection molding business? This article takes a look at the topic.
Benefits of Smart Manufacturing
Smart factories use smart manufacturing to gain production efficiencies, improve production quality and reduce time to market. Machines can now communicate failure points and collect data that can be used to improve predictive and preventative maintenance, which in the long run improves uptime. Data analysis is used to predict and prevent failure; it indicates when intervention is required and recommends the necessary corrective actions. Troubleshooting is more efficient, which benefits both manufacturers and customers.
Sensors, Connectivity and Data
The entire concept of smart manufacturing in injection molding revolves around collecting and analyzing the data. Sensors collect the data and networks transport the data. If a device or piece of equipment on the floor is standalone, it will not contribute to the collective knowledge of the smart factory. Devices and machinery equipped with sensors have the ability to monitor, collect, exchange and analyze data – all without human interaction. The sensors collect data, and communicate better information on the plant floor, as well as outside the plant (or from the outside in) faster, in order to make easier decisions.
Every device that has the ability to gather intelligence needs to be on a backbone of some type that allows it to produce data or have data pulled out of it. New sensor networks can be established, or sensors and data networking can be added to existing devices. The goal in injection molding is to connect the equipment on the plant floor to a network that can monitor, measure, store, and retrieve data.
As for the data itself, decisions need to be made that make the most sense for the injection molder. How and where to house the data is one such decision – should it be kept in-house, or outside of the company walls? Data security is of paramount concern, so if data is stored off premises, remote connectivity and how to safely get into your system from the outside needs to be addressed.
Plastics, in Particular
Since plastics is the third largest sector in the manufacturing industry, it warrants special consideration in the IIoT as it impacts manufacturers and their customers. In terms of injection molding complex components, the data gathered and analyzed can help ensure maximum repeatability in the injection molding process, consistent quality, and low defects. And again, the data also helps determine preventative machine maintenance which helps avoid unplanned downtime.
From the customer perspective, smart manufacturing provides many benefits for communication and visibility. Machine data collection and reporting gives the customer important timing information on project and production order status.
And so it goes. The drive to glean more – and better – data from industrial equipment and systems will continue to improve productivity in the plastic injection molding sector as technology, sensors, and systems continue to evolve, to the benefit of the molders and their customers.
About Denny Scher
Denny Scher is the Marketing Manager for ICOMold, a custom plastic injection molding company based in Holland, Ohio. ICOMold provides low-cost, high-quality plastic injection molding to a variety of industries worldwide, and provides instant quotes through its unique online quotation system. For more information, visit www.ICOMold.com.
The content & opinions in this article are the author’s and do not necessarily represent the views of ManufacturingTomorrow
Comments (0)
This post does not have any comments. Be the first to leave a comment below.
Featured Product
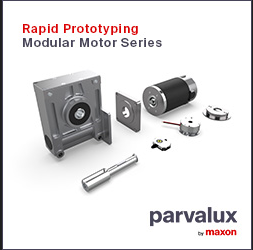