We are in the midst of a major shift that is redefining how our manufacturing processes and industry operate. The amount of data collected from connected, digital devices is growing exponentially, enabling more robust business insights.
4 Steps on Your Journey Toward Industry 4.0
Jeff Christensen | Seegrid
Reprinted with permission from Seegrid's blog:
Introducing new technology can be disruptive: upending the status quo is always challenging for businesses and their employees. For manufacturers, though, the idea of the smart factory of the future is quickly becoming a reality, and even those hesitant to embrace these advancements are finding it hard to ignore. As we advance steadily toward Industry 4.0, companies should prepare to redefine how they approach materials handling.
A GLIMPSE INTO THE PAST
Although the Fourth Industrial Revolution is most commonly referenced nowadays, the previous three shared the common goal of cutting costs while increasing efficiency. The introduction of mechanical processes (the loom and steam power) characterized the first Industrial Revolution, the implementation of the assembly line introduced the second, and we entered the third Industrial Revolution in the 1970s with the creation of automated programming.
In 2017, interconnected automated systems will be the defining technology for the Fourth Industrial Revolution: creating a powerful new standard for the manufacturing industry where data can be shared across systems, yielding meaningful insights that can be used to create a lean environment. The applications of a truly connected enterprise in manufacturing extend to bottom line results such as greater opportunities for reducing expenses and optimizing operations.
PRESENT-DAY OUTLOOK
We are in the midst of a major shift that is redefining how our manufacturing processes and industry operate. The amount of data collected from connected, digital devices is growing exponentially, enabling more robust business insights. According to a report from Deloitte, the top four ways companies are using IoT systems are for real-time analytics (31%), customer and/or supplier collaboration (28%), customer/market insight (26%), and quality control (25%). This information is already helping manufacturers today increase flexibility, optimization, and safety, but the IoT concept also applies to automated robotics.
Today, automation no longer implies standalone robots operating independently of one another and their human colleagues; instead, we are seeing more robust, holistic automation solutions, which leverage big data and the Internet of Things. By connecting hardware and software, as well as various different vendor solutions, manufacturers can maintain comprehensive control over, and visibility into, their entire operation.
Within the materials handling industry, plant managers are leveraging the data collected by their Industry 4.0 solutions to identify variance and make adjustments to improve their existing processes. By recognizing a consistent problem via data, the manager can understand if there is a global or local issue in a more comprehensive way than visually assessing problem workflows or processes.
THE INDUSTRY 4.0 LIFECYCLE
There is a fairly uniform process for the adoption of new technology in materials handling, regardless of industry vertical. Whether the solution serves automotive, food and beverage, e-commerce, or aerospace, the onboarding and implementation of new technology generally follows four steps.
STEP 1: GAINING CONFIDENCE IN NEW TECHNOLOGY
Installing new technology in a new environment always requires change, which comes with a learning curve as employees work to understand how it can make the company more productive and their jobs more efficient. The workforce, understandably, is often skeptical of new solutions, so the leadership must help them learn to trust that the technology will be a reliable part of their workflow, solving a pre-existing problem. This is the point in the process where the plant managers ask themselves, “Is there data to prove that this solution is reliable and effective?” and “How can I best utilize this data to demonstrate its value to my organization?”
In the fourth Industrial Revolution, technology and data sharing come as a packaged deal. Decision-makers track and analyze data to ensure that technologies like self-driving vehicles are performing the tasks as intended. Once the data substantiates that the self-driving vehicle is performing optimally, plant managers and their teams can begin to focus inwardly to optimize how the technology is working alongside existing processes and solutions.
One of the world’s largest manufacturers of home appliances put over 50 Seegrid self-driving vehicles to work in their Ohio facility. The initial measure of success was ensuring that they had an understanding of what the technology could accomplish and that it was performing accordingly. The company encouraged its workforce to learn the capabilities of the self-driving vehicles. They then tracked the usage and adoption of the change process, eventually focusing on a KPI of overall throughput once the vehicles were integrated into the workforce.
At this point in the adoption process, management’s main focus is to ensure that the workers believe in the technology. Management must take on the role of the change agent to help their organization adapt to new technology.
STEP 2: ADOPTION VERIFICATION
Once the workforce has gained confidence in the capabilities of the technology, they must adopt and even embrace the technology. Adoption is often the toughest step – companies must ensure employees use the new solution to its full potential. Adoption is often a stumbling block because it requires human change, and human change is hard, slow, and messy. The natural human reaction to change is resistance.
Before real change can happen, employees must be sold on the true value that new technologies can provide. In order to move on to the next step, the technologies must prove they can make significant improvements in efficiency and predictability. At the crux of Step 2 is educating employees and ensuring they are properly equipped to work with the new solutions to deliver optimal results. Management can then analyze the data to ensure the technologies are being utilized to their expectations.
STEP 3: MEASUREMENT OF PREDICTABILITY
In materials handling, unpredictability is the enemy, but there is always a productivity or throughput metric that can be measured to keep the solution on track. Extracting and analyzing data quantifies the predictability or variance of the technology against the initial throughput measurements or KPIs laid out prior to installation.
One of the largest U.S.-based automobile manufacturers utilizes many unique technologies to optimize the number of labor hours expended per vehicle produced. In a Detroit assembly plant, the company deployed over 75 self-driving vehicles to deliver parts predictably and reliably. By vastly improving throughput, self-driving vehicles help drive the company’s overall goal of reducing labor hours per vehicle produced by the plant.
Mail delivery is another example of an industry using self-driving vehicles to streamline processes. The top metric of interest for management is the number of pieces of mail per day that pass through their distribution centers. Self-driving vehicles are part of the ecosystem that moves mail along its path to distribution, but they are not the only technology that facilitates that movement. The data gathered by self-driving vehicles allows management to stay informed about the progress being made across vertical components of their operation and help make operational adjustments that increase predictability and optimize cost per move.
Materials handling throughput KPIs are certainly key to a business’s overall assessment of new technology, but they are only one component of a larger system. The connected data gathered in each technology vertical enables leadership to pinpoint pain points within the system that will have the most impact to their bottom line, allowing a new level of variance identification and increasing predictability.
STEP 4: OPTIMIZATION
Although it takes time for many businesses to reach this step, optimization is the point at which organizations are able to identify where technology is performing well and where there is room for improvement. By assessing quantified data, management can understand where variance is coming from and adjust processes accordingly.
Pinpointing variances in the data allows them to develop a corrective action, leading to optimization of all processes, which leads to meaningful improvement to the bottom line. The acknowledgement of insights provided by data, the ability to identify key points of variance, and the process of optimization is crucial to truly completing the last step in the journey toward Industry 4.0.
ENVISIONING THE FUTURE
When it comes to creating lean materials handling environments, the ease of information sharing across platforms is crucial. As we embark upon the Industry 4.0 shift, we are going to see creative solutions that make the materials handling industry even more productive and efficient. Be prepared to see self-driving vehicles working side by side with human employees, and plant managers staying up to date with reports and dashboards that monitor, control, and optimize their operations.
Industry 4.0 may still be taking shape, but today’s manufacturing innovators are already working within this new industrial revolution, with many following suit. Companies that have already introduced automation into their facilities are ahead of the curve. These are the companies that understand the need not just for self-driving vehicles, but for data-driven, connected systems. This new interconnected approach to automation introduces us to a bright future, leading us toward the next generation of smart factories.
The content & opinions in this article are the author’s and do not necessarily represent the views of ManufacturingTomorrow
Comments (0)
This post does not have any comments. Be the first to leave a comment below.
Featured Product
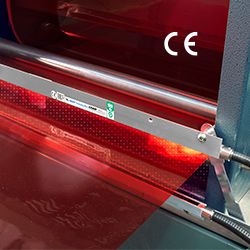