Nobodys bottom line is more valuable than the human lives that help create it. To that end, consider the following best practices for shoring up safety in your facility.
Distribution Center Best Practices to Improve Safety & Efficiency
Megan Ray Nichols | Schooled by Science
Doing business anywhere and in any sector requires a keen mind for balance. And no balancing act is more demanding than the one between safety and efficiency. If you oversee a distribution center and you’ve struggled with either of these, you might be surprised by the opportunities at your disposal to tackle them both with a simple, but decisive, change.
Best Practices for Safety
Nobody’s bottom line is more valuable than the human lives that help create it. To that end, consider the following best practices for shoring up safety in your facility.
1. Cut Down on Clutter
We’re looking at safety and efficiency as discrete demands on your time and attention, but this first element applies to both.
Clutter and disorganization are productivity killers — but more importantly, they’re a significant threat to safety. If a recent walkthrough of your distribution center turned up trash where it shouldn’t be, poorly stowed merchandise or a general lack of employee pride in the state of your facility, that’s a big problem.
Disorder is of particular concern in locations that rely on heavy machinery to stow merchandise or pick orders. Think about the consequences if one of your reach trucks’ tires slip on unattended shrink wrap or broken pieces of a wooden storage pallet. No matter how skilled your operators are, they can’t account for every unforeseen hazard. But making sure they don’t have to is a team effort.
Next time you find yourself in a late-afternoon work slump or a slower season, organize a work detail to have them tidy up your most critical areas. But don’t just make it a one-and-done proposition — look for ways to sneak in regular cleaning efforts and encourage your employees to bring outstanding problems to your attention as they discover them.
It’s not just safety and efficiency that benefit from a clean workplace, either — it could also boost your team’s morale.
2. Consider Incentives to Encourage Safety
It’s pretty common for insurance carriers to give their customers annual or quarterly perks in exchange for, say, maintaining a safe driving record. This kind of incentivizing could work similarly in your distribution center.
Think about it. Would you prefer to make a potentially huge payout because somebody got hurt on your property, or because one of your drivers endangered another? Punitive measures from safety-minded organizations such as OSHA exist for a reason.
But weigh this against the cost of, for example, offering a $100 bonus for each quarter your employees maintain a clean safety record. Even in larger organizations, the cost-to-benefit ratio is likely an attractive one compared with the price of litigation.
3. Take a Serious Look at the ‘Health’ of Your Facility
Distribution centers are built with heavy and potentially dangerous applications in mind — but that doesn’t mean they always age well. If it’s been a while since you’ve taken a hard look at the health of your building, it’s time to do so.
One of the most important things to appraise honestly is the state of your floors. We’re not doubling back to our clutter tip from above — we’re talking about the physical condition of the floors themselves.
Whether it’s heavy machines or pickers fulfilling orders on foot, everything that happens in your facility happens on this surface. Unfortunately, older buildings are no strangers to cracking, sloping or uneven surfacing — and the longer you’re in business, the worse these issues can get.
The answer may involve professional floor remediation, up to and including leveling off uneven and potentially hazardous floor surfaces. It may not be the most attractive fix on this list in terms of cost, but it delivers considerable peace of mind and a solid return on your initial investment.
And let’s be honest: The cost of bringing your floors back up to safety-friendly condition is far more affordable than the expense of dealing with an employee injury. Plus, as with several of the other suggestions here, your employees’ pride in their work and your company could see a boost if you have this work done.
Best Practices for Efficiency
After you’ve taken an honest look at your safety policies, you’re ready to move on to optimizing your efficiency. Here are three ways to get started.
1. Reduce Duplicated Effort
Waste is the arch-nemesis of efficiency. You’ll often hear waste described in terms of “touches” — for example, the number of employees who have to handle a particular product in your inventory before that product makes its way out the door.
Waste frequently rears its head during order picking in distribution hubs. So spend some time thinking about how you store and retrieve your most popular merchandise. Consider picking orders directly from shipping containers instead of moving incoming shipments to an intermediate location or container first.
In other words, make sure neither your employees nor your processes require more product movement than is necessary. It probably does make sense to shift slower-moving products to an appropriate location, but for items that remain in high demand, keep them close and don’t unpack the shipping cartons more than you need to.
2. Consider Alternatives to Traditional Inventory Counting
Unless you’re a masochist, you probably loathe performing inventory. It’s nobody’s favorite part of distribution. Unfortunately, it’s absolutely vital if you want to keep your operation running smoothly.
You may be relieved to learn that the lengthy slog of the “traditional” inventory counting technique may not be long for this world. You can help hasten its demise by implementing an ongoing system for cycle counting instead of waiting until the “appointed” inventory time.
Instead of performing a full-on physical inventory count, you can commit smaller chunks of time on a regular basis to counting portions of your inventory that are particularly sensitive to errors. High-demand products, for example, benefit from this kind of ongoing inventory appraisal because miscalculations here will hurt you the most. Receiving orders in excess of your available inventory is one of the fastest routes to customer dissatisfaction — and lost revenue.
3. Develop Reasonable and Predictable Standards for Vendors
Vendors who don’t comply with established compliance programs and operational standards will slow you down. But vendors who don’t have any guidelines to work with in the first place don’t even stand a chance.
Your livelihood relies on a smooth and harmonious relationship between your distribution center and your vendors. So if you’ve found yourself dealing with slapdash or wildly inconsistent performance from your suppliers, it’s probably time to impose some kind of order. If problems persist even after you’ve done so, it might be time to find a new vendor.
What does this look like? Frankly, your vendor standards should touch on any element of the process that you find particularly sensitive or which you’ve had trouble with in the past. For example, you should consider drawing up standards for things like shipment labels and case pack quantities. There should be as few unknowns in this process as possible.
Standardizing wherever you can and holding your partners accountable is a great way to introduce small efficiency boosts all the way up and down the supply chain. It’ll help you iron out frustrating kinks and create more stable, repeatable and predictable processes.
It’s About the Details
What all of these suggestions have in common is that they require a mind for details — and priorities. If you’ve been barely scraping by with lax vendor standards or your facility is in disrepair, it’s time to reassess. With the help of your team, even some of these smaller operational improvements can help elevate your organization to greatness.
The content & opinions in this article are the author’s and do not necessarily represent the views of ManufacturingTomorrow
Comments (0)
This post does not have any comments. Be the first to leave a comment below.
Featured Product
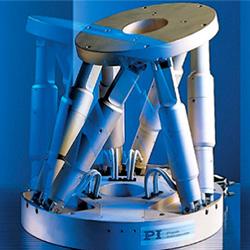