At the heart of IIoT is the way companies capture and share data. The ability to have data about inventory needs immediately available in the cloud and available to both plant floor managers and suppliers offers unheard-of visibility that heightens operational performance.
IIoT and Industry 4.0 are Transforming Manufacturing
Jim Hilton | Zebra Technologies
Who is Zebra Technologies and what is your role in the manufacturing industry?
I’m Jim Hilton, the Director of Global Marketing Strategy for Manufacturing, Transportation & Logistics. Zebra is the market leader in mobile computers, scanners, and barcode printers enhanced with software and services to enable real-time enterprise visibility solutions. With the unparalleled visibility Zebra provides, enterprises become as smart and connected as the world we live in. Real-time information – gleaned from visionary solutions including hardware, software and services – give organizations the competitive edge they need to simplify operations, know more about their businesses and customers, and empower their mobile workers to succeed in today’s data-centric world. Zebra gives businesses visibility into their manufacturing processes and maximizes profitability, creating room for growth.
Our manufacturing solutions capture, track and trace materials, verify parts and production schedules, and improve inventory controls, boosting productivity and ensuring materials get where they need to go. Zebra’s Enterprise Asset Intelligence solutions allow manufacturers to modernize into highly connected, agile, information-driven factories that can respond quickly and intelligently to change and realize potential for new revenue growth and customer satisfaction.
What were the top challenges faced by manufacturers and logistics companies in 2016? How do you think they will change in 2017?
Only about a year or two, manufacturers were looking for ways to save money on labor, overhead, and supply costs to effectively compete in the global marketplace. However, the rising number of product variants, the growing price of materials and higher customer expectations are shifting that model. Today, forward-thinking companies are embracing a quality-minded philosophy, and it is paving an alternate route to growth and profitability. New processes and technology advancements are enabling companies to focus on quality and reap the rewards that an automated and connected plant floor can deliver. Manufacturers are now introducing quality checkpoints and automation at more stages in the process. After all, checking the status of a product after it’s assembled and finding an imperfection not only slows down production and increases costs, but it also makes it significantly more difficult to identify the point-of-failure.
What is the current state of the manufacturing industry?
The global manufacturing industry is in the midst of a dramatic transformation that will profoundly alter plant floor operations. With a desire to connect every stage of the manufacturing process, including end-to-end supply chain fulfillment, manufacturers are turning to automation to improve quality and gain unprecedented visibility. A connected plant floor has become a necessity to ensure high-quality products. For the first time in decades, investment decisions are no longer being driven by short-term return on investment (ROI) calculations alone, but increasingly on long-term quality performance metrics. Companies simply can’t afford to produce defective or sub-standard products and maintain their competitive edge. The cost of poor quality in terms of scrap, reworks, returns and defects is simply too high. In their quest to achieve error-free production, suppliers and manufacturers are making incremental changes to their plant floor operations and moving toward a fully connected, smart factory. In fact, according to Zebra’s recent manufacturing vision study, by 2022, 64 percent of manufacturers expect to be fully connected compared to just 43 percent today.
What are the areas of growth you expect to see from the industrial segments in 2017?
No matter how it’s articulated, the primary motivator for growth generally involves achieving actionable visibility to the overall operation. This actionable visibility applies to:
- Goods, whether it is raw materials, WIP, line side components, or finished goods and if their location is on premise, in transit, or in distribution centers;
- Assets and their location, condition within parameters, alerts as it moves outside set parameters, diagnosis for repair, and the first time resolution of issues surrounding their repair;
- People and their location, productivity, safety, and other factors;
- Processes to ensure that compliance is maintained for both enterprise standards, and governmental/environmental requirements; and
- Places, whether it’s security, capacity, or functionally related.
The climate for growth accommodates investments in overall improvement and applies to aspirations for international or organic increases. Achieving more volume and managing that expected growth, while maintaining current levels of resources will require advancements in technology across the operation(s). Specific priorities are:
- Increase total production / throughput
- Improve ability to adjust to fluctuating market demand
- Increase number of product variants
- Increase visibility across the enterprise
- Decrease cost of production
How is the Internet of Things impacting the industrial segment?
At the heart of IIoT is the way companies capture and share data. The ability to have data about inventory needs immediately available in the cloud and available to both plant floor managers and suppliers offers unheard-of visibility that heightens operational performance. Currently, 27 percent of those surveyed are collecting data from production, supply chain and workers, however the data is remaining in silos rendering much of the intelligence it can provide untapped. That number is expected to drop to 19 percent by 2022, thereby signaling the importance of providing access to this type of critical data to improve productivity and streamline operations.
What is “Industry 4.0” and how are manufacturers embracing it?
Smart factories are the core of Industry 4.0 where real-time communication between the supply chain and the production line enable a high-level of automation and digitization. Making this possible are machines that can self-optimize and share data in real time to deliver better quality goods, unprecedented visibility and impressive cost efficiencies. To be clear, “supply chain” in the context of Industry 4.0 includes the Just in time (JIT) needs for materials management coming from an enterprise vendor and extending outbound to the final resting place of the finished good. Increasingly, companies are focusing less on keeping materials on hand and depending more on suppliers to provide goods on-demand. Industry 4.0 brings with it a move toward JIT shipments in which suppliers anticipate the needs of manufacturers and deliver materials when needed to meet production cycle requirements.
Currently, 26 percent of those surveyed require suppliers to provide JIT shipment notifications. This is anticipated to increase in the next five years with 35 percent of manufacturers expecting JIT notifications. This also means quality assurance must be top of mind for suppliers as well. If manufacturers aren’t keeping extra inventory on hand and receive a bad batch from their supplier the entire production chain can slow down, thereby decreasing efficiencies. However, suppliers aren’t the only ones who will need to start adhering to JIT shipment requirements; manufacturers are being asked to do the same thing by their customers. Twenty-seven percent of those surveyed state their customers currently require JIT shipment notifications and they anticipate that number to go up to 36 percent by 2022.
Which technologies are transforming the plant floor?
Mobile technologies fully integrated to the automation systems of record. Mobile Human-to-Interface (Mobile HMI) simply stated means immediate alerts to mobile workers that result in more visible WIP, more responsive activity, and a more productive line. Wearable Technology expanding the idea of hands-free data capture. Voice Direction (Application-to-worker) and Voice Recognition (worker-to-application) both accommodate a wearable use. Location Tracking (Real Time); RFID (active and passive) and BLE sensors.
What’s new at Zebra Technologies in the way of products and services for the manufacturing industry?
Some of the latest solutions for the plant floor include, purpose-built mobile computers including tablets or handheld devices that accommodate Mobile HMI. Zebra active RFID platforms and services bring to life critical locationing, status, and compliance metrics across operations. In addition, wearables and voice solutions for both the plant and warehouse are leading to new productivity gains. Designed for inventory management, yard management and picking and put-away applications in warehouse and manufacturing environments, Zebra’s Total Wearable Solutions deliver double-digit productivity (15 percent) improvements, with a 39 percent reduction in errors versus traditional voice-only solutions.
Jim Hilton
As a member of Zebra Technologies vertical team, Jim leads strategic initiatives for Manufacturing verticals and Field Mobility initiatives across the all manufacturing segments of the industry. Working alongside a team of seasoned professionals from strategic verticals, his view includes the most advanced mobile solutions around the world and across the enterprise.
The content & opinions in this article are the author’s and do not necessarily represent the views of ManufacturingTomorrow
Comments (0)
This post does not have any comments. Be the first to leave a comment below.
Featured Product
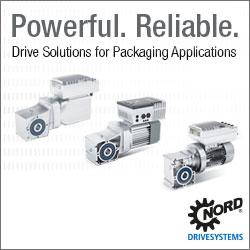