It appears Japanese factories, companies are looking beyond the IOT and or IOE; aiming to connect a variety of assets, e.g., machines, data, technologies, people, and organizations, as well as the existing industries and digital technologies, thereby bringing about the creation of new added value and the solutions to societal problems, bringing “Connected Industries” to fruition.
Japan is moving towards Neo-Industrial Manufacturing - Formation of Flexible Factory Partner Alliance
Junko Nirmala for | ManufacturingTomorrow
Industrial sensors,data and communications are becoming the core topic among factories, companies that foresee themselves in advanced industrial automation. IOT, smart solutions are at surge for individual customer; where as for factories it seems the challenges are more especially getting the machines to communicate in safer environment.
No wonder Japan introduced “Just in time Manufacturing” , Kaizen ,TQM, TQC concepts in the past; In response to fierce international competition resulting from increased globalization, as well as labor shortages and a reduced number of skilled workers due to falling birthrates and aging populations, the companies in Japan have come up with new concept called as “Flexible Factory Partner Alliance” .
The formation of this alliance or this concept is pretty simple and straightforward, utilizing advanced automation technologies of ICT in manufacturing to improve productivity and to tackle to seamless communications among machines, factories , plants in an secured wireless network.
Japanese companies always stressed upon ‘visualization’ in production equipment and production status is the stepping stone to moving forward for improving productivity, and as product development cycles have shortened in recent years, there has been a demand for greater flexibility in the configuration of production facilities equipment and in modifying the production line construction. As a means of achieving greater flexibility, there are rising expectations for wireless communications among machines, different plants and factories.
A major issue in wireless communications in factories where various wireless systems coexist is communication instability due to interference between wireless systems and the impact that has on equipment operation. There had previously been few efforts, however, to resolve this sort of wireless communication issues in manufacturing facilities; To find solutions Alliance of 7 companies in Japan have been formed .
OMRON, ATR, Sanritz, NICT, NEC, Fujitsu, and Murata Machinery have been conducting trials of wireless communications and evaluating the wireless environment in factories. These companies and organizations have at academic conferences and other venues broadly proposed coordination control technology that would enable stability in communications. This would work by controlling independent wireless systems for each piece of equipment, with specific use cases in actual manufacturing facilities.
These companies have come together to form the Flexible Factory Partner Alliance to promote the formulation of standards for coordination control technology. This will thereby ensure stable communications in an environment where various wireless systems coexist, as well as promote their use and further accelerate the adoption of wireless systems in manufacturing facilities.
Through the initiatives of this alliance, the partners will work to meet expectations for a new industrial revolution 4.0; 5.0; accompanying the spread of the use of IoT in manufacturing facilities. Sensors, Data and Communication in safer Wireless communications in manufacturing factories that are expected to accelerate wireless-connected devices to increase productivity, and disseminate the standards.
Few companies were working on trial specifications; last month the first set of 7 companies announced the first alliance . OMRON Corporation, Advanced Telecommunications Research Institute International (ATR), Sanritz Automation Co., Ltd., National Institute of Information and Communications Technology (NICT), NEC Corporation, Fujitsu Limited, and Murata Machinery, Ltd., while Professor Andreas Dengel of the German Research Center for Artificial Intelligence (DFKI)) is appointed as Chairperson.
Experts say "Based on the traditional concepts safe manufacturing concepts; Japanese companies aims at IoE (Internet of Everything)" that connects people as well as machines and things; smart factory is one main part where people /humans take leading role.The use and communication of on-site data, ideas of people seamlessly are important.The data utilization evolves and impacts equipment and factory facilities, Many companies are working towards a thorough process Specifically, Connecting objects (connecting), Connect information (visualize), Improve (Collect and analyze information, create value) and Expanding the scope (sharing data).
Although the Implementation and utilization of IoT in many Japanese factories has been existing for many years now ; or being started, it is merely an extension of the traditional Kaizen effort for the purpose of "productivity improvement" to the last step of product manufacturing.
Few of the Japanese factories feel that to understand the magnitude of change that can be brought by connecting machines, factories and various things in manufacturing plant and to understand the ROI for the given product , line and market these things can not be taken only at the manufacturing site.
While Private companies are working at group factories alliances program; Recently, Japan Ministry for Economy, Trade and Industry [METI] proposed a Policy Concept Titled “Connected Industries” as a Goal that Japanese Industries Should Aim for an ideal approach that Japanese industries should strive for.
As one of the efforts for promoting the Connected Industries policy concept, a goal to create value through connecting a variety of industries,last month the Ministry of Economy, Trade and Industry (METI) held the first symposium for this policy concept, bringing together approximately 600 stakeholders.
It appears Japanese factories, companies are looking beyond the IOT and or IOE; aiming to connect a variety of assets, e.g., machines, data, technologies, people, and organizations, as well as the existing industries and digital technologies, thereby bringing about the creation of new added value and the solutions to societal problems, bringing “Connected Industries” to fruition. To this end, the Japanese government is advancing a wide variety of policy initiatives in cooperation with private sector parties.
Junko Nirmala is a Tokyo resident with 17 years of Professional experience in Technology and business consulting services. Her diverse background includes Advisory assignments completed for 70 plus Japanese companies on Globalization, Founder of startup company in Green Technology, conducting Training and seminars for Global Workforce in Japan and so on. Currently she is involved in Promoting Japan Robots Industry. She has authored 3 books and consistently writes for newspapers and magazines in Japan.
The content & opinions in this article are the author’s and do not necessarily represent the views of ManufacturingTomorrow
Comments (0)
This post does not have any comments. Be the first to leave a comment below.
Featured Product
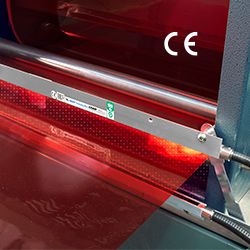