Additive manufacturing represents a seachange for the manufacturing sector. In many cases, 3D printing has resulted in an immediate, cost-effective solution to an issue. More importantly, it has resulted in a complete re-engineering of parts, so that they are now better suited for the dedicated function they are intended to serve.
Additive Manufacturing Technology Enables Radical New Designs
Kirk Rogers for | Canadian Manufacturing Technology Show 2017
For thousands of years, civilization relied on casting for the creation of elaborate and complicated objects, including copper statues and metal tools. Today, casting is used in manufacturing for the creation of small, intricate shapes that are otherwise difficult or uneconomical to make by other methods. The prime advantage is that, once the castings are created, the parts fabricated from these moulds can be mass produced quickly and at a low cost.
The creation of initial castings, however, can be expensive and time consuming. In addition, accessing large production facilities — where the use of castings is best suited — is a serious challenge for small companies looking to create prototypes or low-volume quantities during the early stages of development.
Warning, sharp turn ahead
The most popular technologies used in additive manufacturing today — typically associated with 3D printing — were developed by North American inventors in the 1980s. Over the past four decades, additive manufacturing technology has been enhanced, refined, and improved to the point where parts created from castings might soon be a thing of the past.
By giving virtually anyone the power to conceive, design, and create their own parts — without any of the limitations associated with traditional processes — creativity is returned to the design process. This can lead to significant innovation. Rather than taking an existing part, and simply reproducing it, we’re now able to completely re-engineer parts for the function for which that part is intended. In addition, what used to take years, can now be done in months, weeks, or even days.
This is a landshift change that has resulted in major innovation that promises to lower costs, improve flexibility, reduce complexity, and decrease time to market for new parts. Let’s look at some examples.
Implications for remote locations and legacy requirements
Two common implications for additive manufacturing are associated with the availability of legacy parts for older equipment and the accessibility of parts for operations located in harsh environments and/or remote locations. In some industries, it is common to find 30-year-old equipment still in operation. If a pump or other vital component breaks or fails, however, it can be difficult (or impossible) to find parts.
For off-shore oil rigs or research installations located in the high Arctic (to provide two examples), access to parts can be a serious constraint to productivity. Depending on season, delivering and installing a replacement part might not be possible for weeks on end. For remote-located facilities, distance can also be a factor, resulting in machinery being offline and production being halted for long periods of time. Today, additive manufacturing is being used to print a replacement part, in plastic or metal.
Improving time-to-market in the aerospace sector
The creation of major components in the aviation and aerospace industries is a hugely complex and expensive endeavor; despite the processes associated with their creation becoming more lean and agile than ever before. One example is the auxiliary power unit used to power on-board navigation and entertainment systems when aircraft are sitting at the gate or on the tarmac.
Typically, components like these take three or four years to develop; from concept, to prototype, to reality. With the help of additive manufacturing technology, this process has been reduced to just eight months. And, we’re not talking about derivative design concepts, but completely new ideas that can evolve from a ‘back-of-the-napkin sketch’ in April to a working prototype by December.
Removing traditional restrictions leads to profound new automotive designs
For decades, one of the most prominent features of nearly every car and truck on the market — the front grille — has been defined by the need to place the radiator in the front of the vehicle. Coolant that has been passed over the engine block (when running), where it is heated, makes its way to the radiator. The radiator then passes the hot coolant through a series of metal tubes that are designed to conduct heat away from the liquid and into the air. When the coolant has reached the correct temperature, it is pumped back into the engine block.
With the help of additive manufacturing technology, automotive engineers are experimenting with new solutions. These experiments have the potential to change the interaction between the fluid and the engine, resulting in dramatically smaller radiators with more active surfaces that, in some cases, won’t need to be located at the front of the vehicle. Production costs can also be reduced by 25%, while improving the vehicle’s performance by an additional margin. Removing the need to have a large radiator located at the front of the vehicle will inevitably result in significant changes to the look of the cars parked in our driveways in the future.
Improved efficiencies that level the playing field
Companies like BMW have massive prototype divisions that spend millions of dollars annually to improve the fit and finish of nearly every part that goes in to their precision-engineered automobiles. No commitment to tooling of a part is ever made until the prototype is perfect. In fact, most large automobile manufacturers are constantly looking for improvements that might come from combining, even eliminating, parts in an effort to reduce manufacturing time, lower costs, or improve performance.
Additive manufacturing levels the playing field for the basement inventors and start-up innovators in our industry. Instead of adding functions separately, one by one, parts can now be redesigned for multiple functions. If a single part can replace an assembly that used to consist of ten parts, for example, imagine the huge impact that could have on the supply chain management process. Instead of ten suppliers, there could be two or three. Instead of 60 people in the company supporting those 10 parts, there could be just a handful.
Conclusion
Additive manufacturing represents a seachange for the manufacturing sector. In many cases, 3D printing has resulted in an immediate, cost-effective solution to an issue. More importantly, it has resulted in a complete re-engineering of parts, so that they are now better suited for the dedicated function they are intended to serve.
After relying upon casting — and its inherent limitations — for centuries, the manufacturing sector has been revolutionized by the availability of 3D printers that now cost just a few thousand dollars.
Additive manufacturing will continue to generate cost savings, but will also continue to improve manufacturing flexibility, reduce complexity, and decrease time-to-market for new parts and the products that use them. Most importantly, in my opinion, is that additive manufacturing will remove most of the restrictions associated with the design and creation of new parts. The result will be a flood of new innovations and improvements for the manufacturing sector as a whole.

Kirk Rogers, PhD, Technology Leader, GE Center for Additive Technology Advancement
The content & opinions in this article are the author’s and do not necessarily represent the views of ManufacturingTomorrow
Comments (0)
This post does not have any comments. Be the first to leave a comment below.
Featured Product
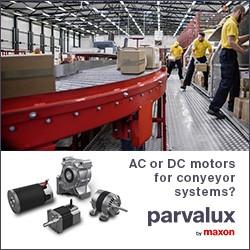