The 7 Wastes are tasks or processes that provide little to no added value to the product or to the user experience.
Lean Manufacturing: Eliminate the 7 Wastes With Self-driving Vehicles
Jim Rock | Seegrid
We live in an age when many aspects of our lives are continuously optimized and improved upon. We call up transportation at the touch of an app. Instead of waiting at a doctor’s office, we opt for medical consultations over video conference. Online orders arrive at our doorsteps in less than 24 hours. Such optimizations feed our need for instant gratification, setting new, higher expectations for many businesses, including manufacturers and their material handling and distribution systems.
Now, more than ever, manufacturers must find ways to operate more efficiently and meet consumers’ growing demands for faster shipments. Many facilities are investing in automation like self-driving vehicles for flexible and reliable delivery of goods. But it can be difficult to fully grasp the many facets automation impacts within manufacturing and distribution networks.
Below, we will illustrate how automation delivers greater optimization and reduces waste in multiple forms. We will explore how self-driving vehicles address the 7 Wastes (or “muda”) of lean manufacturing and distribution. The 7 Wastes are tasks or processes that provide little to no added value to the product or to the user experience.
THE 7 WASTES OF LEAN MANUFACTURING
TRANSPORT
Transportation of materials, in and of itself, is not considered a wasted step in delivering goods to a consumer, but unnecessary or costly transport steps are considered a waste. Self-driving vehicles eliminate the need for people to handle the movement of materials from one location to another. Personnel costs and injuries, not the cost of vehicles, account for over 75% of transport costs. Self-driving vehicles eliminate the human cost and error, assuring warehouse managers that the transportation process is running efficiently. Seegrid vision guided vehicles (VGVs) are also able to manage traffic conditions, faults, obstructions, and other throughput impediments either by alerting management to the issue, or rerouting transport steps as necessary. The traditional Lean approach to reducing transport waste has been to move tasks closer together. Self-driving vehicles address the costs of transport directly without the need to reconfigure facilities.
INVENTORY
Inventory has long been used to cover up inefficiencies in manufacturing, supply chain, and distribution. Excess inventory allows cover for operations’ poor responsiveness to changes in demand. Self-driving VGVs achieve a seamless flow between work centers and enable consistent delivery of goods, delivering the right part at the right time–without getting tired or distracted. When materials are picked up and dropped off consistently, manufacturing processes are standardized, which keeps inventory levels low. This allows for Just-in-Time (JIT) operations running around the clock, maximizing production while minimizing work in progress (WIP) inventory. Consistency equals efficiency.
MOTION
To prevent the excessive movement of people or machines within the workspace or workcells, self-driving vehicles deliver goods to a consistent position every time. This allows for optimization of the workspace, eliminating unnecessary movement by the operator when handling materials. It also allows for consistency or process within the cell, and eliminates potential for injury due to unexpected or extreme operations. In many cases, the automation systems can directly transfer materials from one system to the next, with no operator interaction.
WAITING
Self-driving vehicles are predictable and deliver goods on time, every time. Additionally, our fleet management tool, Seegrid Supervisor, shares real-time data, creating added visibility into workflow and statistics to reduce waiting and wasted time. It can even be used to plan and pre-position material handling resources as demand fluctuates throughout the facility. Compiling data allows operations managers to detect patterns that may point to discrepancies, giving them the chance to modify processes to increase efficiency.
OVER-PROCESSING
Non-standardized working practices caused by operators using different methods between different shifts can result in over-processing or over-handling. Self-driving VGVs enable consistency within the warehouse and ensure that the best and most efficient practices are being followed.
OVERPRODUCTION
Self-driving vehicles reinforce consistent Just-in-Time delivery, allowing companies to schedule and produce only what can be immediately sold and shipped. By reducing human error, self-driving vehicles ensure that all processes are completed according to production schedules. Predictable behavior by the VGVs reduces the need to create buffer inventory to compensate for shift surge, employee break time, and other inconsistencies.
DEFECTS
Improper handling techniques can result in visible and invisible damage to product and goods. Driving and stopping too quickly, colliding with obstacles, racing over rough floors, and cutting corners all impart shock loads to the goods being transported, causing significant damage. VGVs always drive with consistent speed and acceleration, following well-defined routes that avoid damaging the products being transported. This results in higher production yields and fewer losses in the distribution steps, reducing waste and satisfying customers.
NEXT STOP: INDUSTRY 4.0
Lean processing is becoming an attainable goal for the companies that are proactively taking the steps needed to embrace Industry 4.0. While there are still many businesses that are reluctant to make a change, at Seegrid we have seen first-hand the benefits of implementing connected materials handling technology like self-driving vehicles.
As companies are finding, the implementation of automation to solve the 7 Wastes doesn’t signify an end to the role of the human workers. Instead, it sparks new opportunities for warehouse workers who perform dangerous and often tedious tasks. Automation also eliminates factors such as human error, damage to product, and production downtime–a few of the most common manufacturing wastes.
The content & opinions in this article are the author’s and do not necessarily represent the views of ManufacturingTomorrow
Comments (0)
This post does not have any comments. Be the first to leave a comment below.
Featured Product
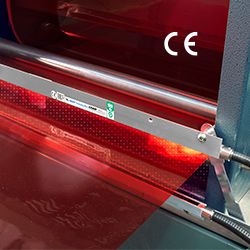