Many companies that know how to design for metal 3D printing have found suitable applications and have ordered parts. But these applications are still in their infancy.
The Future of 3D Printing
Gordon Styles | Star Rapid
What would you consider the biggest industry milestone of 2017?
From a technological standpoint, the launch of the 3D “production system” from Desktop Metal was significant this past year. Until now, no machine had combined spreading, compacting, high-resolution printing and drying into a single pass, back and forth without wasted motion. The increased speed, reduced cost of metal powder, and the ability of the production system to utilize the entire build volume to produce parts, has started to open an entirely new market for metal 3D printing. If the cost-per-piece and quantity volume meet the company’s claims, it’ll be able to meet full-scale production requirements at a fraction of the cost. Note, however that while the parts manufactured with this machine are suitable for low-stress applications in consumer goods, it still cannot compete in terms of strength with the fully-welded parts created using Direct Metal Laser Melting.
Where are 3D printing technologies headed?
When it comes to metal 3D printing, it wouldn’t be surprising for 2018 to be a bit uneventful. The reality is that we are still in a sort of trial period and many companies are testing the water to see how the technology can be leveraged for their specific purposes. This year we’ve seen many companies take the plunge and reach out to us about metal 3D printing. This has exposed a knowledge gap when it comes to design-for-manufacturing practices about the process. To help combat this issue, Star Rapid launched online tutorial videos and in-person training at our factory, and other companies have launched various educational initiatives as well.
Many companies that know how to design for metal 3D printing have found suitable applications and have ordered parts. But these applications are still in their infancy. Companies are testing small batches of parts to ensure that they successfully operate under real-world conditions with the intended performance. Once this is completed and doubts are erased, the industry will explode with demand. This likely won’t begin to happen until the latter part of 2018.
Are there emerging applications for 3D printing?
The automotive space is an interesting one to watch unfold. Europe seems to be in an electric car race. Emission limits and electric car incentives are becoming commonplace in this region. Even China has gotten in on the action with electric car mandates. For gas and diesel vehicles, manufacturers continue to seek ways to reduce weight to increase miles per gallon and reduce emissions. Have you noticed that many new cars don’t have a spare tire? That not only reduces weight, but lighter vehicles also have fewer flat tires! 3D printing’s ability to reduce weight, without sacrificing safety or the driver’s experience makes it attractive. The same logic can be applied to electric vehicles. The battery technology is extremely dense and heavy. Lowering weight increases the range a car can get on a single charge – which is very attractive to vehicle manufacturers.
In China and globally, we’re seeing renewed interest in additive manufacturing for medical use. In addition to prosthetics that have become quite popular over the last year, we’re also seeing interest in creating medical models and cranium replacements. There is also a growth in micromolding. Micromolding can provide an excellent alternative to designing and manufacturing medical devices used in minimally invasive surgery (MIS). With micomolding, MIS designers don’t have to deal with limitations placed on size or the complexity of material selection for production yields. Medical equipment can be quite expensive so parts created using additive manufacturing present cost-effective, functional alternatives.
Do you think plastic 3D printing will one day replace plastic injection molding?
3D printing won’t replace plastic injection molding anytime soon. These processes are much more complementary than competitive. If you need 1 to 10 parts created, 3D printing is the best option as there are low initial costs for small production runs. However, once you start to get into larger quantities and move beyond the prototyping phase, plastic injection molding makes more sense in the long term.
Which metals can you currently use in 3D printing processes?
At Star Rapid, the main metal powders we use are titanium, aluminum, maraging steel and stainless steel. When it comes to the development of powders for 3D metal printing, it’ll be important to keep an eye on China, which has been able to successfully produce metal powders at a lower cost than other countries. In the past few years, there have been many metal powder manufacturers emerging – a trend that is expected to continue. With increased competition, material costs will gradually become more affordable and there will be an emphasis to develop new types of metal powders.
Is 3D printing of metal parts a feasible replacement for current assembly line methods?
At the moment, it does not provide a feasible replacement. The main reason is speed. However, the studio system and production system from Desktop Metal is a huge leap forward in making metal 3D printing a higher-volume production solution. If they’re even somewhat successful then I suspect other suppliers to create new machines that follow a similar design logic. But it’s important to understand that traditional manufacturing has a head start of 150 years – that’s hard to beat in terms of efficiency.
Most metal 3D printed parts also require post-machining work. For example, a printed part may need to be CNC machined to remove the supports implemented for structural integrity during the building process. CNC machining may also be needed to create a more desirable surface finish – since 3D printing is completed in rough layers – or to make sure precision features such as threads are formed properly. Roughly 90 percent of the metal parts we print require some sort of post-machining. This is what makes the idea of a hybrid technology, which combines subtractive and additive manufacturing, so exciting. Despite it being years away from true commercial viability, it can certainly find niche applications right now.
Do you see new materials being developed to replace metals and plastics for use with 3D printing processes?
Plastic compounds and metal alloys work very well for their intended purpose, and right now there are no viable alternative for either – no matter the manufacturing method. That said, 3D printing is a process that can use all kinds of substrates, as we’re seeing with food processing (chocolate), construction (concrete) and medical (tissue). I see additions to plastic and metal, but not substitutes for them. Maybe the most interesting future application will be with some form of nanomaterials like graphene – but that remains to be seen.
What trends within the manufacturing industry do you see emerging in 2018?
Conformal cooling for plastic injection molding is emerging as a technology that could be quite advantageous for making mold tools. With additive manufacturing techniques like metal 3D printing, complex cooling channels can be optimized during the mold design phase rather than post-processed at suboptimal locations. This trend is already established in Germany and we will see more widespread adoption globally in 2018.
About Gordon Styles
Gordon Styles is the founder and president of Star Rapid, a provider of rapid prototyping, rapid tooling and low-volume production services. Utilizing his background in engineering, Gordon founded Star Rapid in 2005 and under his leadership the company has expanded to 250 employees. With an international team of engineers and technicians, Star Rapid combines advanced technologies – such as 3D printing and multi-axis CNC machining – with traditional manufacturing techniques and high-quality standards. Prior to Star Rapid, Gordon owned and managed the United Kingdom’s largest rapid prototyping and rapid tooling company, STYLES RPD, which was sold to ARRK Europe in 2000.
The content & opinions in this article are the author’s and do not necessarily represent the views of ManufacturingTomorrow
Comments (0)
This post does not have any comments. Be the first to leave a comment below.
Featured Product
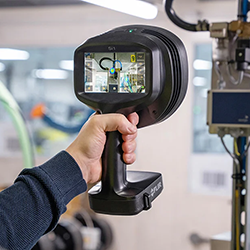