Fully connected machines eliminate the need for post-production stress tests. The end users locations becomes the test environment. The varying use cases of each deployment create variations in the testing.
Three Industrial Internet of Things Macro Trends of 2018
Tom McKinney | HMS Industrial Networks
Reprinted with permission from HMS Networks:
At HMS Industrial Networks we see 3 Macro Trends continuing in 2018 in regard to the Industrial Internet of Things.
- Cellular and Wired Data communication costs will continue to decline.
- The use of sensors and video/photos to monitor remote sites will continue to increase.
- Companies will continue to optimize operations by reducing the amount of time employees spend servicing systems in the field.
These Macro Trends will continue to expand the reach of automation by connecting more systems to the internet.
We expect the following transitions in 2018:
1. Secure remote connectivity will become common place on the factory floor:
At HMS we have been selling remote access solution for over 10 years. In the beginning of 2017 many of our sales calls focused on the security of connecting machines. Some customers hesitated to deploy remote access or data solutions based on the fear of exposing their networks to an outside threat. The idea of pushing data to a public cloud was commonly seen as a security risk. Companies debated if the risk was worth the value. At some point in 2017 the tide turned and customers went from debating value to taking the value discussion off the table. Today it is rare to see a customer still debating if AWS or Azure based solutions represent value. It is crystal clear these platforms are more reliable and lower cost when compared owning and deploying compute or data storage infrastructure. Taking advantage of these platforms and data from deployed products is a must have for any machine builder deploying and supporting products to a large market.
Today customers seek to understand how access control is implemented on Talk2M. They want to know how HMS protects the Talk2M and Argos cloud platforms from DOS attacks. They want to better understand how we leverage independent auditors to evaluation our network. Customers are committed to deployment and know it is possible to deploy a secure solution based on eWON technology. Every major player is enabling remote access to lower the cost of provisioning and support of machines.
2. Utilities and Industries with geographically distributed machines will leverage more cellular data:
The M2M communication market has evolved significantly over the last 5 years with cellular or wired connectivity becoming a clear alternative to proprietary radio communications systems. The cost to setup, support, and maintain a custom communication systems is significantly more than the annual data fee associated with LTE offerings from major cellular providers. As cellular cost per megabyte continue to fall and more wired access is deployed, most companies will move away from custom solutions.
In addition to lower costs, internet service providers offer additional benefits including private networks and security services. These benefits will force utilities other regional services to transition away from proprietary systems for remote monitoring. Additional higher bandwidth features can also be supportive such as video based monitoring. Rolling out this technology will allow vendors still physically visiting sites to perform virtual site inspections and significantly scale back the amount of time spent traveling to sites.
Companies looking minimize any security risk these public networks introduce will leverage VPN technology to encrypt all of their data. VPN technology is very mature and with coupled with a comprehensive access control solution the network is more secure than the typical corporate LAN.1
3. Quality teams will drive big data value:
The idea of improving a machine by including data service to monitor the product is common. The end user value varies depending on the machine up time, cost of down time and reduction in down time created by the monitoring solution. In many applications machines run reliably until standard service is required. The end user may not see any benefit from monitoring the device 24/7 if a failure is never detected. This limited value makes the feature less attractive to the end user but it can be invaluable to the machine manufacture.
Manufacturers of high uptime industrial machines can benefit from analyzing performance data across many deployments. This data becomes more valuable as the number of machines deployed increases and the failure rate decreases. Identifying ways to improve quality on a machine that is very reliable can be very challenging. Justifying a design change may be almost impossible without significant investments in lab based stress tests.
Fully connected machines eliminate the need for post-production stress tests. The end users locations becomes the test environment. The varying use cases of each deployment create variations in the testing. Data from fully operational machines can be evaluated for changes that could hint at failure modes. The biggest benefit is found when a system does fail. A complete historical data reference allows quality engineers the opportunity to accurately identify the failure mechanism. This information allows companies to invest their design resources more optimally lowering R&D costs and improving overall product performance. Not to mention the data helps to improve customer service and validate warranty claims.
HMS is working with a number of machine builders to capture real-time data from deployed machines and use that information to improve future products. Innovative companies like Tesla are using data collection to test and improve their products in similar ways.
The content & opinions in this article are the author’s and do not necessarily represent the views of ManufacturingTomorrow
Comments (0)
This post does not have any comments. Be the first to leave a comment below.
Featured Product
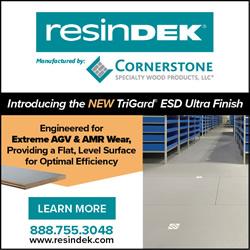