Discussing MITs new Professional Education course; Computational Design for Manufacturing
Computational Design for Manufacturing
Wojciech Matusik | MIT Computational Design for Manufacturing
Tell us a little bit about yourself and your position at MIT.
I'm a Professor of Electrical Engineering and Computer Science at the Computer Science and Artificial Intelligence Laboratory (CSAIL) at MIT. My lab is focused on computational fabrication: the intersection of computing and design and fabrication. My mission is to see how these multiple fields can be fused together to change how we manufacture and fabricate different objects and products in the future.
MIT recently announced the launch of 7 new professional education courses, one of them being Computational Design for Manufacturing. Tell us about that course and why it was created.
The Computational Design for Manufacturing course was designed to address emerging trends in the industry. Automation continues to expand. Products are quickly becoming more sophisticated and complex. We are starting to see the emergence of an entirely new class of advanced manufacturing that allows us to create devices and products that are highly customized and integrated with electronics and multiple functionalities. This transformation is redefining what it means to be a designer and an engineer. Computational Design can support professionals and help them adapt in this evolving environment. The idea is to create new types of workflows that rely much more on automated software tools, artificial intelligence (AI) and other advanced techniques to simplify the design process and enable mass production and customization at scale.
How are innovations in automation and robotics reshaping the manufacturing industry?
For one, you have much greater freedom of form, as you are no longer restricted by the traditional manufacturing process itself. We used to have production lines that were essentially fixed, so you could manufacture lots of products very quickly in a relatively automated way, but they were all the same product.
Now, as the manufacturing world embraces robotics and additive manufacturing, you see the pendulum starting to swing in the other direction. We can now manufacture increasingly small-scale structures—like micro-scale structures—that can be embedded in larger structures and so in terms of form, you can really develop parts at a much finer level. There is also much more flexibility. You not only can make complex products that couldn’t be made before, but each product that comes from the assembly line can be different from the next to meet the need of any given customer. Whether it is custom-made shoes and apparel or on-demand automotive parts – you are starting to see this transformation taking shape across multiple industries and domains.
What trends or patterns do you see taking shape?
I think that the trend is that we will be able to make more and more complex, tightly integrated products that are designed for many different functions and objectives at the same time – and that are manufactured on-demand by robotic systems. This change is already underway in a number of fields. 3D printers are revolutionizing production of metal parts in aerospace, automotive, and medical industries.
How do you think these changes will affect designers and engineers?
This affects the jobs of designers and engineers because they are the ones who will be tasked with taming this new complexity – and figuring out how to build large volumes of highly integrated, complex, customized products in an efficient, cost-effective manner – all at scale. From my perspective, it is going to be very difficult – if not impossible – unless we introduce new modelling technologies and allow a computational system to optimize it for a particular purpose. For example, you may want a car to be safe, but also light-weight and efficient. Or design a wrench that is both durable yet light and easy to hold. Computational design can help engineers balance can these trade-offs, and make the design process faster and easier. It could open the door to a new age of personal manufacturing.
What exactly is computational design?
Computational design effectively is a process of translating highly complex specifications provided by the user to manufacturing instructions that is being executed by machines or a group of machines to arrive with a complete physical object.
How is generative design different from traditional design, and why is it necessary?
There are two different classes of designing things. One of them is directly specifying your shape. And the other one is starting with an assumption; basically, you start with specifying what that product is supposed to do.
Generative design enables designers to simply specify what the product is – its’ use, function, and other considerations -- and then let software create the product automatically. It’s a completely different way of interfacing with software. Generative design will no doubt become more essential as we develop new products that integrate more functions.
Can you share an example of how generative design can be applied in industry?
Consider the manufacturing of a hearing aid. With generative design, a scan of the ear would be used to determine the shape of the device. An engineer or designer would specify what the overall dimensions of the device, list out the desired internal components and then the software would automatically determine materials, layout and the technology needed. This can be used for any type of product, including clothing or automotive parts, to reduce the use of materials while still providing the function of the overall component.
What kinds of skills or approaches do they need to develop in order to prepare for Industry 4.0 and why is this course and training so important for people that are going to be working in the manufacturing industry?
Whether you are a designer, an engineer, product managers, etc. – you want to be exposed to the new tools and workflows that are being developed because in the end it will help you create and manufacture a better product. In engineering, you are always trying to optimize performance – but as products integrate more functionalities these objectives will increasingly contradict each other. Computational design is going to become incredibly useful when it comes to balancing the trade-offs and finding the best of both worlds.
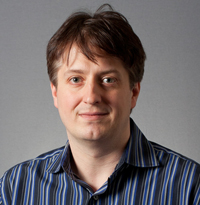
Professor Wojciech Matusik is an Associate Professor of Electrical Engineering and Computer Science at the Computer Science and Artificial Intelligence Laboratory at MIT, where he leads the Computational Fabrication Group. Before coming to MIT, he worked at Mitsubishi Electric Research Laboratories, Adobe Systems, and Disney Research Zurich. He studied computer graphics at MIT and received his PhD in 2003. He also received a BS in EECS from the University of California at Berkeley in 1997 and MS in EECS from MIT in 2001. His research interests are in direct digital manufacturing and computer graphics. He holds more than 40 US patents. In 2004, he was named one of the world's top 100 young innovators by MIT's Technology Review Magazine. In 2009, he received the Significant New Researcher Award from ACM SIGGRAPH. In 2012, PI Matusik received the DARPA Young Faculty Award and was named a Sloan Research Fellow. He currently serves on the DARPA ISAT Study Group.
The content & opinions in this article are the author’s and do not necessarily represent the views of ManufacturingTomorrow
Comments (0)
This post does not have any comments. Be the first to leave a comment below.
Featured Product
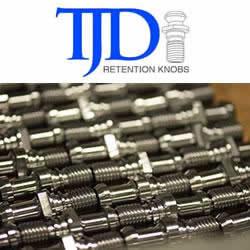