The main purpose of the Machining Simulator is to promote learning about manufacturing in a classroom setting. Each simulator reacts exactly like a real machine and allows students to design, create CAD/CAM models and command the machine tool to produce simulated end product
Axiomtek and FANUC America Case Study: Machining Simulator
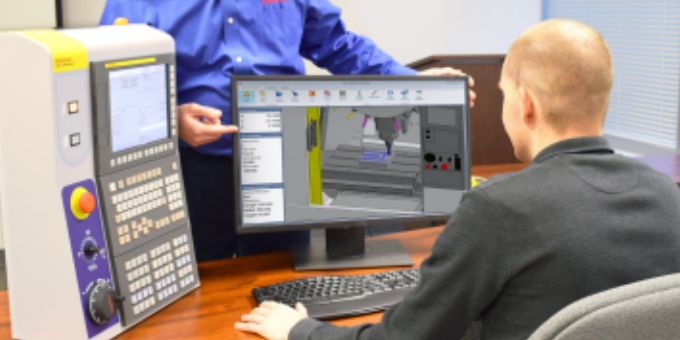
Contributed by | Axiomtek
The future of automation is influenced by computer technology that enhances the manufacturing process in order to achieve higher levels of efficiency and productivity. Today’s manufacturing design and production process requires significant knowledge and a well-developed skill set. Integrating the design, engineering and manufacturing processes can lead to greater production effciency, precision, and quality, but it adds a layer of complexity to the process of learning how to make the best use of all the tools available.
FANUC America Corporation, a world-renowned manufacturer of Computer Numerical Control (CNC) systems, robotics and factory automation solutions developed a machining simulator that allows students, educators and hobbyists to learn Computer-Aided Design (CAD), Computer-Aided Manufacturing (CAM) as well as CNC and machine tool operations. Students can sign up for a free education account for Autodesk Fusion 360 CAE/CAD/CAM software, while small businesses can receive a free one-year subscription through a special promotion with FANUC. The main purpose of the Machining Simulator is to promote learning about manufacturing in a classroom setting. Each simulator reacts exactly like a real machine and allows students to design, create CAD/CAM models and command the machine tool to produce simulated end products. The Machining Simulator is applicable for training students from the high school level upwards as well as manufacturing professionals who want to explore additional areas of their manufacturing processes.
Industry Challenges
The current method of classroom instruction typically separates design from manufacturing. The structure of the learning process and the resulting challenges are as follows:
- CAD is taught in the classroom. The students might never learn the basics of CAM or they might be taught CAM in a different class.
- CAM requires CNC machine knowledge.
- CNC machine operation is often taught in a shop environment. This leads to a disconnect between the classroom and the shop process and makes overall learning more difficult.
- Separation of these critical aspects can create barriers for the student’s understanding of all the related principles of manufacturing.
- CNC machines are expensive. They require training and safety equipment to operate. All of these are limiting factors that can create major constraints for learning.
- Downtime for training in a manufacturing environment is costly - both in labor and lost machine productivity.
The Machining Simulator’s Principles and Elements
FANUC’s Machining Simulator integrates all of the following areas into one learning platform:
- CAD/CAE, CAM
- CNC Programming
- CNC Operation
- Machine Operation
- Program/Part Prove-out
Challenges and Requirements
FANUC faced the following challenges in developing the Machining Simulators:
- Space constraint. The simulator required compact hardware. The PC was to be installed in a tight CNC enclosure along with additional electronics.
- Heat dissipation. The enclosure had no ventilation, low airflow and heat margin was a concern. A fanless computer with high heat tolerance was required.
- Power supply. 24VDC was preferable and the supply must have a maximum current of 2A.
- Performance. Running CAD/CAM and 3D simulation software requires good computing power such as an x86-based industrial computer with good CPU performance and high reliability.
- Memory. A significant amount of RAM and SSD storage capacity are crucial for fast processing and software program storage.
- Ease of integration. The simulator combined hardware and software from around the world. They had to integrate well and deliver optimum results.
Solutions
Axiomtek offered its ICO310 DIN-rail embedded system as the solution to help FANUC, and it met all of their challenges. The ICO310 provides a good balance of CPU performance and reliability, and it met all of FANUC’s required features without driving up costs. The scalable ICO310 allowed FANUC to configure a quad-core, Intel Celeron N3160 with 8GB of RAM and a 32 GB SSD to deliver the high performance levels needed while remaining cost effective.
The ICO310 can withstand high operating temperatures and continuously deliver reliable operation. It uses low wattage components and is fanless, while its compact size fits within the FANUC Machining Simulator enclosure. In addition, the ICO310 offers high performance CPU options, a wide power input range, and low power consumption. The Axiomtek ICO310 met all of FANUC’s requirements.
The following are standard ICO310 features:
- A fanless design
- Intel® Celeron® processor N3060 (1.6 GHz/2-core) or N3160 (1.6 GHz/4-core)
- 2 RS-232/422/485 ports
- 4 USB ports
- 2 isolated 10/100/1000 Mbps Ethernet ports
- 1 PoE PD compliant with IEEE 802.3at standard through LAN 1
- 1 DIO port
- Supports wireless (3G/GPRS & Wi-Fi)
- 1 mSATA & SATA SSD (or HDD)
- 12-24 VDC wide range power input
Why Axiomtek
“We have worked with Axiomtek on several previous products and have used the ICO300 and various eBOX IPCs in the past. The Axiomtek products have always been very reliable. Axiomtek has provided us with a customizable yet cost effective industrial PC solution.” Engineering Manager, FANUC America Corporation.
The Machining Simulator project was a challenge because of the requirements and the unique environment in which it is used. It is made for a classroom but many of its specifications and reliability requirements are those of industry. Axiomtek’s product, the ICO310, and the personalized service provided met all of FANUC’s expectations
Axiomtek’s ICO310 was chosen partly due to FANUC’s past positive experience with other Axiomtek products and because of the consistent personalized service delivered by the Axiomtek team.
“The comprehensive range of industrial PC products to choose from and the ease of configuration are key factors. FANUC is a low volume, high mix business so the quick replies to technical and commercial requests by the Axiomtek team have helped us a lot. Easy, early access to new products as well as technology provided by Axiomtek made a difference during the selection and testing phases. Their partnership focus and understanding of their customer needs allowed for low minimum order quantities while we ramped up demand and production.” Engineering Manager, FANUC America Corporation.
Future Plans
FANUC plans to continue their partnership with Axiomtek to deliver the best solutions to their customers. FANUC America will remain dedicated to helping North and South American manufacturers increase their global competitiveness by “maximizing their efficiency, reliability, quality and profitability.”
Axiomtek believes in fully supporting its customers to achieve their goals with the best products and services it can provide. The company looks forward to their continued partnership with FANUC and to helping them meet all of their future challenges. The Axiomtek team takes pride in its ability to develop long-term relationships with its customers and will continue to deliver excellence in both products and services.
For more information, please contact Axiomtek at solutions@axiomtek.com
or call us at 1-888-GO-AXIOM (1-888-462-9466)
The content & opinions in this article are the author’s and do not necessarily represent the views of ManufacturingTomorrow
Comments (0)
This post does not have any comments. Be the first to leave a comment below.
Featured Product
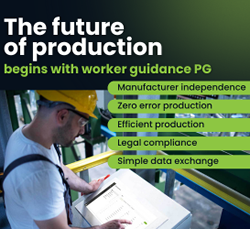