When you are working on designs for new medical equipment, thinking about the components you will have to bring together and the systems they will create is essential.
Spring Assemblies and Medical Devices: What to Think About Before You Design
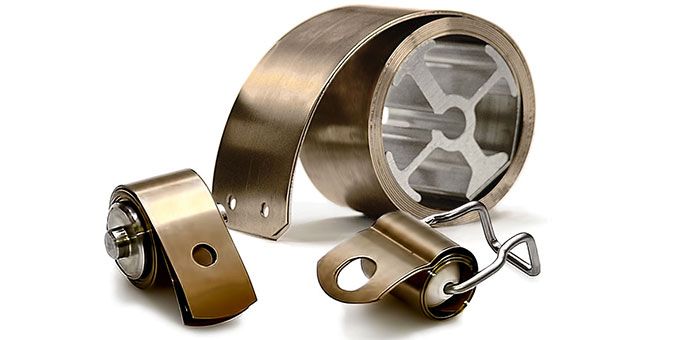
Ed Jones | John Evans’ Sons
The medical device industry has been booming for most of the past two decades. Healthcare research has led to a rapid expansion of specific devices that treat medical needs from the rare to the commonplace. Those devices range from the simple to the surprisingly complex, often incorporating automatic sensors, computer monitoring, or even remote monitoring by healthcare providers. Other devices remain simple, providing new designs for well-established concepts like the adjustable hospital bed, the wheelchair, or even an IV stand. Read on to learn more about the importance of designing a great custom spring assembly for your new device.
Forethought and Design Preparation
When you are working on designs for new medical equipment, thinking about the components you will have to bring together and the systems they will create is essential. That means breaking your design down to the level where you can visualize the components that need to go into items. That means individually designing each spring assembly after assessing the options available.
To help you with this, here are three of the most commonly used springs that are available for medical devices, and the common applications they are used for today.
-
Constant Force Springs: These springs are known for their consistent and smooth range of motion, and for the fact that they maintain a constant load whenever they extend or contract. This makes them ideal for certain surgical applications, because the need for exact movements and steadiness is vital under those circumstances.
-
Spring Reels: These components are designed to counterbalance moving parts. For example, they are quite popular in assemblies that regulate the retraction of pneumatic hoses. They can be used in a variety of similar applications, including as stabilizers for moving components.
-
Spiral Torsion Springs: These springs are used when creating devices that need a free range of movement with a “return to center” behavior. This means they work out great when used in monitors and other devices that might require components to be swiveled or moved to allow others to see, or where a component needs to be able to move freely to allow access to other parts of the device.
Choosing from among these types of springs means understanding their strengths and weaknesses, as well as the purpose of your custom spring assembly design.
Medical Spring Applications
There is no limit to the number of applications you might be able to put medical grade springs to if you think about their use, but there are limitations to the exact types of applications an individual spring will usefully cover. Even so, you can expect to see spring assemblies performing all of the following mechanical tasks as part of successful device designs:
-
Assemblies designed to aid in the retraction of parts
-
Ejection assemblies
-
Components designed to swing freely, while returning to a baseline state
-
Support structures designed to absorb shocks or minimize movement
-
Weight and pressure sensitive switches
-
Medical components that stabilize other components
-
Doors, access panels, and other enclosures
Design and Prototyping Process
When using medical springs in your device designs, it’s important to have a clear process for design and prototyping so you can efficiently dial in the exact spring size and tension you need. It’s not always easy to lock those numbers in, either, because your on-paper predictions can only get you so close to real-world behavior. The fact is, the math never lines up absolutely perfectly, and the more moving parts your assembly has, the more complex the calculation will be. This is further complicated by the fact that each spring assembly in your final product design will need to be constructed and tested separately to ensure functionality before being fully assembled and further refined to ensure the overall product works.
To navigate this process successfully, you need to be able to count on your supplier to maintain a level of consistency that allows you to rest assured that every piece you order will be manufactured according to the most stringent specifications. Medical devices are precision instruments, and while not every application that they are put to is a matter of life and death, you never know when a malfunctioning component could slow down a lifesaving process. That’s why your design and your supply line should reflect this.
The prototyping process may reveal design tweaks that require changes to the spring choices you make, and that should be expected too. When you work with a consistent supplier, though, those tweaks are easier to make successfully because the components are more predictable in their differences, just as individual components with certain specifications are more consistent.
Sourcing for Manufacture
As you move from the prototyping phase to full manufacture, your choice of supplier becomes even more critical, because you will not only need consistency in the manufacturing of your springs, you will also need consistency in their availability. Not every precision part source is going to be able to handle the constant demand for parts in quantity, so it is important to find a well-known source that can not only meet your design needs, but your production needs as well.
Keeping this in mind as you source spring components for each new custom spring assembly you design is important, whether you are building a single device for use in a single installation or testing out the production process for a new product you will introduce to the public in short order. That’s why you need to find knowledgeable manufacturers you can lean on for help as your design process unfolds.
Successfully using medical grade springs in your medical device design means breaking down your device into components and building custom assemblies that accomplish specific tasks. When you do this successfully, it gets easier to put together the full design for your product. More importantly, by finding the source who can handle support for your prototype stage and demand during your manufacturing stage, you prepare yourself for a level of consistency that should help to streamline your next project. That means less time tweaking the production process for a faster route to the market.
About Ed Jones
Ed Jones is the Marketing Manager of John Evans’ Sons, the international leader in design and manufacturing of constant force springs, constant force spring assemblies, and pusher springs (variable force).
The content & opinions in this article are the author’s and do not necessarily represent the views of ManufacturingTomorrow
Comments (0)
This post does not have any comments. Be the first to leave a comment below.
Featured Product
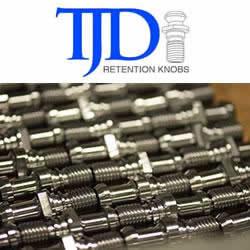