Human Machine Interface (HMI) is present when human interaction with an automated device becomes necessary. HMI is present now more than ever due to the need for more reliable hardware, higher data security, and efficiency.
Successful Digital Transformation in Industry 4.0 Starts With Human Operators
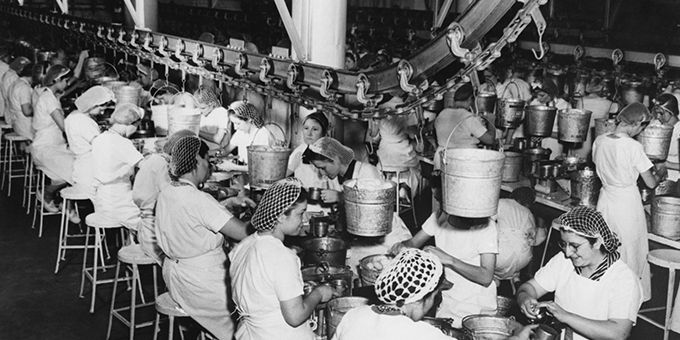
Porfirio Lima | Sensai
Can you tell us a bit about Sensai and its role in the advanced manufacturing industry?
In our personal lives we are surrounded by technology -- smart devices constantly make our lives easier. However; many industries are lagging, including the manufacturing industry. While several manufacturers have advanced in this 4th industrial revolution, the vast majority of them are in the mindset of, “If it's not broken, don’t fix it” and therefore make the mistake of placing the digital transformation low in their priorities. Traditional manufacturers that fail to make this digital transformation will lose competitiveness and are doomed to be replaced by those who lead the 4th industrial revolution. Sensai’s role is to help manufacturing leaders from the shop floor to the top floor to make better decisions empowered by our technology.
How is Industry 4.0 changing human-technology interactions?
Shifts in manufacturing will require industries to change and come up with smarter ways to increase production. This means adopting technologies that are both agile and innovative that can augment human labor. Human Machine Interface (HMI) is present when human interaction with an automated device becomes necessary. HMI is present now more than ever due to the need for more reliable hardware, higher data security, and efficiency.
The aim is to decrease dependence on human interaction regarding operations but increase the quality of human interaction. Humans should not be “wasting time” supervising and monitoring normal flowing processes, but should be readily available whenever an abnormality presents itself and the machine can not fix it by itself. Human Interaction will mainly be present in critical decision-making, in maintenance & repair, as it is necessary to quickly interpret the data and make quick decisions to save time and money.
What are the roadblocks manufacturers experience when seeking harmony between humans and technology?
The biggest roadblock is culture. As a leader, if you don’t have a culture built to embrace disruption, the response of the employees will almost always be negative and in turn they could end up sabotaging the disruption. This is because the first thing that comes to their mind when they hear about a technological change is job instability with the fear of being replaced by robots that can do the same job with less mistakes. However they should learn to see it as working side-by-side with a tech assistant to help augment their productivity and produce better results. This is why managing your culture and change is imperative to organizational success.
How can these roadblocks be overcome?
Digital transformation leaders can overcome these roadblocks by gaining a better understanding of how their business values need to be modified and challenging their employees with a technological optic. The new blood on the market is aware of the changing landscape and how that information can be used against them. As the leader you need to change the perspective to a positive way of analyzing how the tech improvements can help your organization and your crew at work and give them the possibility to deliver better results. But the most important thing to note when overcoming the roadblock is transparency, Show your employees how you are leveraging the information and grant them access so they are able to use it at their advantage.
What is your response to manufacturing professionals who fear technology will replace their jobs?
History has shown over and over again through each of the industrial revolutions that the fear of losing jobs is unfounded. Experts agree that technology creates more jobs rather destroys them. Hard, dangerous, repetitive and even boring jobs have indeed shown a decline over time. Thanks to technology, jobs are safer, more dynamic and more interesting. My response is this: Do not fear change, embrace it. It will happen either way. Professionals need to prepare and focus on high value added jobs and activities. Make it clear that machines and humans are never going to be the same, so focus on those differences. Think of the basic definition of what makes us human and use technology to augment this humanity within everyone of us. Machines and technology works for us, not the other way around.
How can business leaders build a culture that fosters the acceptance of technology to augment humans potential?
The way to approach this is by putting people first - emphasizing transparency. As a leader you need to share your strategy internally and how you will move the pieces around the board so your employees are aware of what's next and they will play a role in impacting productivity. Doing so will make workers feel at ease as things change. If you involve them enough and they are now part of your project, it is almost impossible for them to try to sabotage the digital transformation.
How would you describe the utopian factory of the future in terms of human / machine interaction?
The utopian factory is a smart factory where every system is interconnected -- facilitating the interactions from machine to machine, machine to people and even people to people. In this utopian factory, there is zero waste: zero defects, zero overproduction, zero waiting, zero unused talent, zero unnecessary transportation, zero inventory, zero unnecessary movements and zero extra-processing. You get it! Machines and their parts will always be subject to wear and will always have failures. In an utopian factory having all the systems connected allows managers to map the assets and the working status of each machine. Thus, people will be able to know when a part is going to fail. Systems will even automatically schedule a purchase order in advance from the vendor to minimize the programmed downtime. The end game is having the whole manufacturing facility operating with clockwork precision so that people can enjoy their personal time and be at ease knowing that everything is taken care of. While there is currently a large gap between this utopian factory and industry leaders, Sensai can help to close this gap. Most importantly, the utopian factory of the future is a place where every person can reach their fullest potential and be happy.
About Porfirio Lima
Porfirio is the CEO and Founder of Sensai. As an experienced entrepreneur in innovation, marketing, technology & strategy, he believes in the transformational power of leadership, collaboration and purposeful happiness. With over 10 years of manufacturing experience, Lima serves to successfully create a disruption in the way productivity is increased in manufacturing environments across the world and build a world-class team of entrepreneurs that are passionate about technology, human behavior and that want to make a dramatic change to the status quo.
The content & opinions in this article are the author’s and do not necessarily represent the views of ManufacturingTomorrow
Comments (0)
This post does not have any comments. Be the first to leave a comment below.
Featured Product
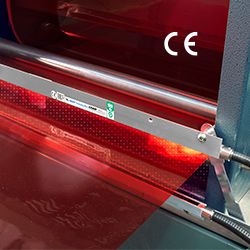