This bimodal distribution is rampant throughout industry. It can be very simply described as “too much of the wrong and too little of the right” at any point in time and “too much in total” over time.
Why Conventional Planning Fails
Chad Smith and Carol Ptak | Demand Driven Institute
At the heart of most supply chains lies a planning tool called Material Requirements Planning (MRP). Invented in the 1950’s, codified in the 1960’s, and commercialized in the 1970’s, MRP became THE way of life for supply order generation and synchronization throughout the world. Yet the people that interact with MRP everyday know that something is very wrong. They may not be able to explain exactly why, but they know that if they did exactly what MRP told them to do, it would have disastrous consequences for their company and career.
There is one fatal flaw in MRP that makes it distort the relevant information that planners, companies, and supply chains are desperately seeking. Correcting this one fatal flaw allows the promise of MRP to be attained and the bullwhip to be effectively mitigated.
As the inventory quantity expands out of the optimal zone (see illustration) the return on working capital captured in the inventory becomes less and less as the flow of working capital slows down. The converse is also true; as inventory shrinks out of the optimal zone and approaches zero or less, revenue flow is impeded due to shortages. When the aggregate inventory position is considered in an environment using traditional MRP, a bimodal distribution is frequently noted.
Bimodal Inventory Distribution
Not only is the smallest population in the optimal zone, but the time any individual part spends in the optimal zone tends to be short-lived. In fact, most parts tend to oscillate between the two extremes. The oscillation is depicted with the solid curved line connecting the two disparate distributions. That oscillation will occur every time MRP is run. At any one time, any planner or buyer can have many parts in both extremes simultaneously.
This bimodal distribution is rampant throughout industry. It can be very simply described as “too much of the wrong and too little of the right” at any point in time and “too much in total” over time. In a survey by the Demand Driven Institute, 88 percent of companies reported that they experienced this bimodal inventory pattern. The sample set was over 500 organizations around the world.
There are three primary effects of the bimodal distribution event in most companies:
High inventories. The distribution can be disproportionate on the excess side, as many planners and buyers will tend to err on the side of too much. This results in slow-moving or obsolete inventory, additional space requirements, squandered capacity and materials, and even lower-margin performance, as discounts are frequently required to move out the slow-moving items.
Chronic and frequent shortages. The lack of availability on just a few parts can be devastating for many manufacturing environments, especially those that have assembly operations and common material or components. The lack of any one part will block an assembly. The lack of common material or component will block the manufacture of all parent items calling for that common item. This means an accumulation of delays in manufacturing, late deliveries, and missed sales.
High bimodal-related expenses. This effect tends to be undermeasured and underappreciated. It is the additional amount of money that an organization must spend to compensate for the bimodal distribution. When inventory is too high, third party storage space may be required. When inventory is too low, premium and fast freight are frequently used to expedite material. Overtime is then used to push late orders through the plant. Partial shipments are made to get the customer some of what they ordered but with significantly increasing freight expenses.
These three effects are indicative of major flow problems in most organizations. Furthermore, these effects are directly tied to conventional planning activities and efforts in these organizations.
Read more at: https://www.demanddriveninstitute.com/ddmrp.
About Carol Ptak
Carol Ptak, CFPIM, CIRM, DDPP, DDLP, is a co-founder and partner with the Demand Driven Institute. Ms. Ptak spent decades in supply chain management first as a practitioner and then as a consultant and software executive. She is also a past president of APICS, and has authored several books on demand driven methods, MRP, enterprise resource planning, lean, and the theory of constraints (TOC).
About Chad Smith
Chad Smith, DDPP, DDLP, is a co-founder of the Demand Driven Institute. Mr. Smith spent 20 years in supply chain and management consulting and software co-founding industry innovator Constraints Management Group and working personally with Dr. Eli Goldratt. He has co-authored and contributed to several books on demand driven methods, MRP and the Theory of Constraints (TOC).
The content & opinions in this article are the author’s and do not necessarily represent the views of ManufacturingTomorrow
Comments (0)
This post does not have any comments. Be the first to leave a comment below.
Featured Product
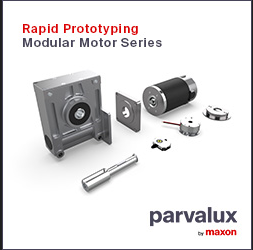