PLCs are special computers designed to control industrial processes and machines. Software PLCs offer great communications functionality through communicating with other computer equipment or controllers.
Understanding the Basics of PLCs
Daron Underwood | Kingstar
PLCs (Programmable Logic Controllers) are mainly used in industrial and commercial applications. Industries rely on a wide range of machines that are complex to operate. Every machine has parts that are operated by motors, pneumatics or hydraulic drive systems. Sensors are used to sense when machine parts are about to move or malfunction and external objects that are processed by the machines in order to facilitate effective machine operations. PLCs are used to expedite these industrial machine operations. PLCs monitor machine inputs, make appropriate decisions based on their programs, and control outputs to trigger machine and process automation.
Basic PLC operations
PLCs are made up of input points or modules, output points or modules, and a CPU (central processing unit). Inputs accept a wide range of analog and digital signals from different sensors/ field devices and work to convert them into logic signals that are CPU compatible. The CPU then makes appropriate decisions and executes control instructions as per the set program instructions within the memory. Output modules are tasked to convert the CPU control instructions into analog or digital signals that are in turn used to control different actuators / field devices. Programming devices are used to input instructions that determine what PLCs do for specific inputs. Finally, an operator interface device facilitates the display of process information and input of new control parameters.
Before PLCs were introduced, most of these industrial tasks were executed using relay controls or contactors. This approach is known as hard-wired control. It relied on circuit diagrams, electrical components, and wiring lists to get the job done. Electricians would install specified electrical components required to perform particular tasks. If an error occurred, electrical wiring had to be reinstalled. Hence, a machine functionality change or expansion required extensive electrical element changes and rewiring.
Advantages of PLCs
Complex tasks are easier to tackle with PLCs because wiring between relay contacts and devices is conducted within the PLC program. This makes correction of errors and modification of applications easy to handle. In fact, it is easier to develop and alter a PLC program as compared to wiring and rewiring a circuit. Other PLC advantages include centralized diagnostics, small size, faster and cheaper duplication of applications, immediate documentation of applications, integrated diagnostics, and the ability to override functions and facilitate fast and easy system alterations.
PLCs eliminate the need for external wiring that would be required to control industrial processes. A PLC control system increases reliability since logic is stored in the PLC’s memory, thus reducing the occurrence of logic wiring errors. It also ensures flexibility because it is easier for end users to develop and modify a PLC program.
In summary, PLCs are special computers designed to control industrial processes and machines. Software PLCs offer great communications functionality through communicating with other computer equipment or controllers. They are easily networked to execute tasks like data gathering, supervisory control, program downloads and uploads, and process and device monitoring.
About Daron Underwood
Daron Underwood has more than two decades of experience and expertise in embedded technology and real-time systems – from machine control to Human-Machine Interface development. He headed the embedded product and services group for Ardence, a Citrix Company prior to the formation of IntervalZero in 2008. During his career at VenturCom/Ardence and as a customer before he joined the company, Daron was instrumental in the development and advancement of the company’s market-leading RTX real-time software. He provided technical knowledge and guidance that helped shape the earliest version of the product.
The content & opinions in this article are the author’s and do not necessarily represent the views of ManufacturingTomorrow
Comments (0)
This post does not have any comments. Be the first to leave a comment below.
Featured Product
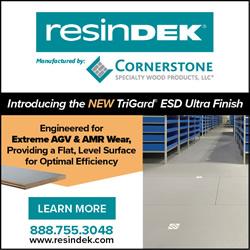