Manufacturers can now finally benefit from powerful visual QA systems with no downtime, very short implementation lead times, rapid diagnostics and far less testing, training and spare parts.
How Autonomous Machine Vision Saves Time and Money
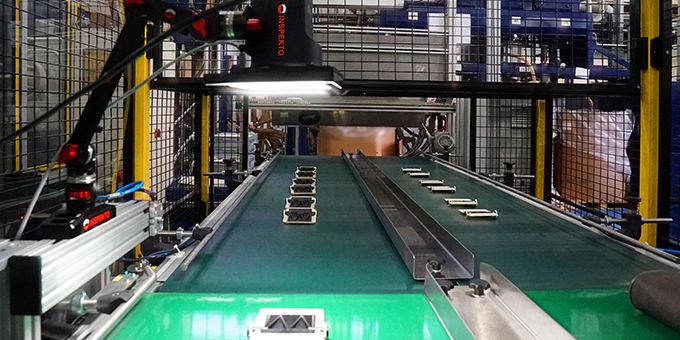
Contributed by | Inspekto
Traditional machine vision solutions wreak havoc on operational efficiency and the industry is ready for change. As the late Japanese industrial engineer Shigeo Shingo once said, “Improvement usually means doing something that we have never done before." Here Miki Gotlieb, VP of Operations at Inspekto, explains how Autonomous Machine Vision impacts operational efficiency in a way that has never been seen before.
Traditional machine vision solutions, which have been around since the 1980s, are implemented in a project-based approach. The process requires the selection and acquisition of numerous components, including cameras, lenses, lighting, filters, computing platform and software from a range of suppliers. The QA manager is therefore subject to the lead times of the vendor of each piece of equipment — while the resulting overall lead time is governed by the long lead item (LLI).
Once the integrator receives the components, they can then integrate them with one another, alongside the tedious task of preparing the software selected and then building a hard-engineered solution on the shop floor, before beginning the software training process. For a simple application, implementation can take several weeks to a few months. For a more complex solution, typical time frames are several months and, in some cases, go up to an entire year.
In addition to these lengthy waits, since traditional machine vision solutions are specifically designed for a location on the production line, it is nearly impossible to move the solution from one location to another. Alongside this, the diagnostic tools for a traditional machine vision solution are often unique too, which means they are an expensive investment.
In most cases the manufacturer is unable to diagnose a fault themselves, due to a lack of machine-vision specific knowledge and must instead rely on the integrator for assistance. This inability to address the issue immediately in-house delays manufacturing, which may have to be halted while the fault is addressed.
To further reduce the downtime should a machine vision solution become faulty is to stockpile spare components. A factory with several system configurations will keep spares of all unique system parts in order to achieve a decent MTTR and minimise the downtime in case of a malfunction. This increases costs and effort for the parts which must be maintained and managed.
A new way of working
Since the launch of Autonomous Machine Vision (AMV) first product entries in VISION 2018 in Stuttgart, these challenges can be completely overcome. While AMV systems can be purchased for 1/10th of the cost of a traditional solution and installed without the help of an integrator 1,000 times faster, they also bring about a vast array of operational benefits to the manufacturer.
The Inspekto S70 is the world’s first Autonomous Machine Vision system. Designed with the manufacturer in mind, the system is suitable for any quality assurance, gating or sorting application. The system’s arm is flexible enough to be installed on any machine, at any angle and position to get the required field of view (FOV). The system’s visual sensor, comprising all camera, lenses and lighting components, has a wide range of capabilities to suit different applications.
In addition, the fact that AMV systems are an off the shelf product – and not a lengthy integrator project – removes the lead time of ordering the components for traditional machine vision solutions. The Inspekto S70 can be delivered as soon as the purchase order is received, and it can then be implemented upon arrival in the plant. In addition, as Inspekto, as a vendor, represents the cost structure of one company. This means purchasing a system from Inspekto is unlike purchasing components from the many vendors involved in a traditional integrated solution, which generates savings that are passed on to the customer in the form of the very affordable prices.
Finally, thanks to the several artificial intelligence (AI) engines underlying the S70’s ‘brains’, very minimal configuration is required of the manufacturer’s employees and the system will self-adapt and self-adjust to its environment. For example, no proof of concept (POC) creation nor any solution development is required from an external integrator to set up the system. Once installed the system will self-adjust to any changes on the line or the lighting environment.
Furthermore, once the manufacturer has set up an Inspekto S70 system, it is not fixed forever to that point on the production line, unlike a traditional solution would be. If at any time in the future the QA manager identifies another point on the line that would benefit more from visual QA, the system can be moved from its original location to the new one. Additionally, if the system is not required for a period of time, it can be stored and then re-installed as necessary in a couple of hours.
This state of affairs is drastically different from that of machine vision solutions of the past, where moving a solution from location to another would in most cases be either impossible, due the new location’s specific physical and components requirements, or require a very notable bill of waiting time and cost for an integrator to make the necessary change.
Complete autonomy
If any adjustment is required with an installed Autonomous Machine Vision system, it will perform self-diagnosis to identify the issue, significantly reducing the mean time to repair (MTTR). It can set up its own parameters and use its intelligent capabilities to test itself and report back to the QA manager. The QA manager requires no specific training to achieve this, all is built into the system and it is easy to use.
Autonomous Machine Vision offers very fast MTTR. For example, if the system’s visual sensor apparatus is faulty it can be efficiently fixed or replaced by a member of the factory QA team. This is in stark contrast to traditional solutions, which would require the return of the integrator to suggest tests, figure out the problems and attend the site to correct it —a time-consuming and costly process.
The improvement in operational efficiency offered by Autonomous Machine Vision represents, as Shigeo Shingo said, something we have never done before. Advancements in machine learning, artificial intelligence and optics have made Autonomous Machine Vision possible, paving the way for the Inspekto S70. Manufacturers can now finally benefit from powerful visual QA systems with no downtime, very short implementation lead times, rapid diagnostics and far less testing, training and spare parts.
About Inspekto
Inspekto is a German industrial company with Israeli DNA. Backed by leading industrial businesses from across the DACH region, the start-up is out to reshape the machine vision sector, introducing the first powerful entries into the new Autonomous Machine Category.
The content & opinions in this article are the author’s and do not necessarily represent the views of ManufacturingTomorrow
Comments (0)
This post does not have any comments. Be the first to leave a comment below.
Featured Product
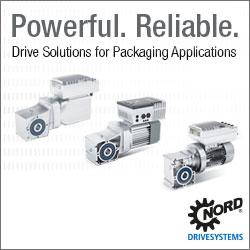