Essentially, we’ve reigned in the power requirements of our devices by up to three orders of magnitude, which lets us do everything we need to do off that small form-factor harvesting budget.
Batteryless IoT Sensing
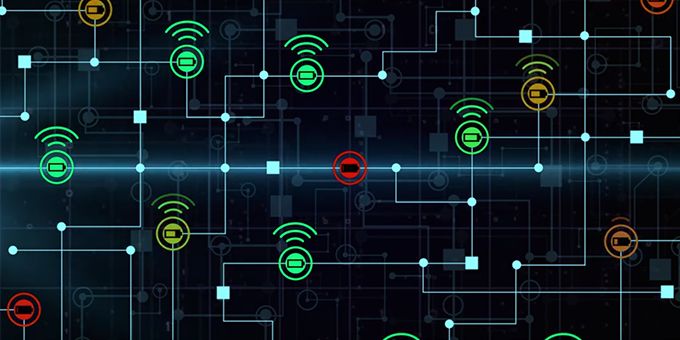
Brian Alessi | Everactive
Who is Everactive?
Everactive is focused on batteryless industrial sensing solutions that will lead the revolution in physical-world data. This idea—generally, “the Internet of Things” or “IoT”—is all about extracting digital “intelligence” from previously “dumb” physical assets in order to utilize them more efficiently. The data from trillions of items will dwarf today’s primarily user-generated digital content and will have an enormous and meaningful impact on how we live our lives and operate our businesses, cities, governments, etc.
Despite the hype, the IoT hasn’t really taken off. We think that’s due to the significant challenge in powering all these devices and the fundamental limitations of batteries. The logistics of having to replace batteries at scale is mind-numbing. It’s prohibitive. The simple cost-benefit analysis often doesn’t make sense.
Everactive systems consist of batteryless Eversensors that are placed throughout a facility to provide a continuous view into the operating health of various equipment and infrastructure, reporting through a gateway that connects thousands of Eversensors back up to our Evercloud, a cloud-based analytics service that displays the insights, alerts, and raw data from these Eversensors. Our key differentiator is that our Eversensors operate entirely off harvested energy, without the need for any batteries. This offers the ability to realize the goals of the IoT by scattering wireless, connected devices at scale without ever requiring any maintenance.
No batteries, how does that work?
It’s all based on circuit breakthroughs that our co-founders have been working on since their days at MIT, where they first asked what it would take to make truly self-powered wireless devices. There’s a sizeable delta between the power required by most sensor devices and that which can be provided by small form-factor energy harvesting sources. Essentially, we’ve reigned in the power requirements of our devices by up to three orders of magnitude, which lets us do everything we need to do off that small form-factor harvesting budget. For reference, we can use about a 10 degree Fahrenheit temperature differential to power our devices entirely. If you think about a manufacturing setting, there are a lot of areas where that delta exists. We can also power off about 150 Lux, which is the light level of a dimly lit room.
It’s important to note that we did not do this by scaling back how often our sensors collect and send data. In fact, our devices are always-on, always listening, and continuously sending data—all off that same harvested energy source. Achieving both our low power levels and continuous monitoring is a monumental breakthrough and a testament to the work of our entire engineering team.
How big of a problem are batteries in industrial environments?
It is significant, especially when thinking about scale. Even for a mid-sized plant, the numbers of batteries quickly add up as sensors are deployed across probably thousands of assets—think, motors, pumps, relief valves, steam traps, heat exchangers, etc. A major reason to monitor these assets in the first place is to reduce maintenance costs. Now, if companies have to add thousands of batteries to their maintenance schedule, how much value would they see when their staff is spending full weeks or months per year hunting down and replacing dead batteries? It’s like the household smoke detector problem on steroids.
In addition to the logistical and financial costs of trading one maintenance event for another, there are real safety and environmental concerns. The very existence of a battery presents challenges to achieving hazardous location certifications. Plus, the ultimate disposal of batteries at such a large scale is harmful to the environment.
Finally, most battery-powered devices will employ duty-cycling techniques in order to conserve power. The result is that data is typically measured and sent in bursts, meaning, by default, you will have less-than-real-time insight into the status of an asset’s health and performance.
Can you talk about your first application, the Steam Trap Monitor? Why Steam Traps?
Steam traps are everywhere. Worldwide, there’s somewhere near 100 million steam traps used across a range of industries. The ~20% annual failure rates are not a secret. Neither are the easily quantifiable losses from a blowing trap. The problem is that given the number of traps and their difficult-to-reach locations, they’re tough to monitor at scale. They’re a perfect example of the following line of reasoning: “well, if I’m going to have to send someone around to change batteries every year, I might as well just continue to manually inspect the asset.” The problem, of course, is that if someone inspects the trap in April and the trap fails in May, it could very well waste energy for a full 11 months before it is noticed and fixed. Wireless monitoring is a great solution to this challenge, but batteryless monitoring really adds value because it can fully replace an antiquated process. Instead of having your team manually inspect 1,000 traps each year just to find that 800 are good and 200 are failed, you only need to tend to the 200 that actually need attention.
So, the logic behind steam traps was: (1) they’re prevalent, but largely unmonitored assets, (2) the economic case is clear based on known data and (3) a key reason why IoT hasn’t worked so far for monitoring them is due to the “battery problem.”
What other applications are you envisioning in the near future?
On top of the core batteryless sensing technology, we’ve identified a number of other applications for our “full-stack” systems. What that means is that these systems handle everything from the data acquisition (using Eversensors) to the data analysis in the Evercloud interface. So, for a given asset, we provide the necessary hardware and software to deliver insights about the given asset – its operating health, failure mode, etc.
The hardware platform allows us to be really “plug-and-play” about what we’re sensing—meaning we can add sensors that monitor temperature, humidity, vibration, pressure, etc.—while the software platform allows us to reconfigure the analytics to deliver insights based on the sensors in use. So, you can see pretty quickly how we can take this technology and adapt it to a number of different asset monitoring solutions, with the same two high-level goals: (1) completely maintenance-free, batteryless sensors and (2) a seamless cloud-based insight delivery service.
Up next: we are prototyping two products in parallel. Our Flare System Monitoring solution uses the same Steam Trap Monitoring hardware to monitor pressure relief devices in headers to let refineries quickly track down the culprit in a flare event. Our Machine Health Monitoring solution is built on our next-gen hardware that incorporates the ability to do vibration analysis on a variety of rotating equipment—motors, pumps, fans, etc.
Would your technology be compatible with 5G sensors in an industrial environment?
Right now, we could utilize 5G to backhaul data from our gateway to our Evercloud. Ultimately, as the 5G mMTC standard evolves, we imagine being able to backhaul data directly from our batteryless Eversensors to the Evercloud. That would be an extremely exciting development and one that our engineering team is actively tracking.
What is your business model?
We’ve taken a services approach. Rather than charge for the hardware, we charge a subscription for the data insights. Think: “hardware-enabled SaaS.” We’ve found it to be a lighter lift for a lot of our customers because it avoids steep capital expenditures and they prefer to have us handle the hardware, networking, and data management and analysis. Ultimately, what matters to the customer is the insight from the data streams that we generate and analyze. We’ve abstracted out all the complicated technology pieces to deliver just that.
What’s next for Everactive?
We’re thrilled to use our recent $30 million in funding to drive adoption of current products, refine and take to market in-development products, and continue to look at what’s next. The grand vision is to deploy stamp-sized, self-powered Eversensors that build in an increasing number of sensing modalities and can communicate at even longer ranges in industrial settings back to the Evercloud (either via a gateway or not). We see a clear technology path to being able to do that and are confident we will achieve that in the coming years. For now, our immediate goal is to continue to demonstrate the value of batteryless sensing to our target industrial market and grow the business product-by-product.
About Brian Alessi
Brian Alessi is the Director of Product Marketing at Everactive, a technology company that sells completely batteryfree sensors for a range of industrial assets. Brian drives product positioning and messaging, customer development, and overall go-to-market strategy for the company. In this capacity, he works closely with customers responsible for maintenance & reliability, innovation initiatives, and overall plant management.
The content & opinions in this article are the author’s and do not necessarily represent the views of ManufacturingTomorrow
Comments (0)
This post does not have any comments. Be the first to leave a comment below.
Featured Product
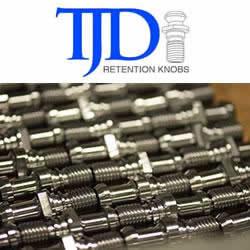