The proven impact of machine learning models has pushed more investment toward their development. Still there are plenty more gains to be realized.
6 Ways Machine Learning is Revolutionizing Manufacturing in 2019
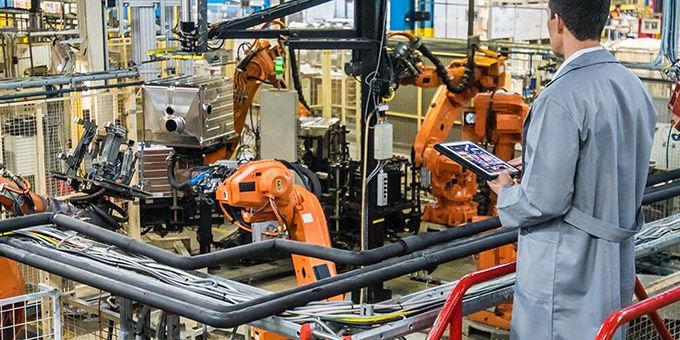
Kara Lanio | rapidminer
From the first harnessing of economies of scale to the introduction of the assembly line, the search for new efficiencies has always been at the heart of manufacturing. Today, the greatest new gains come from the innovative combination of hardware and software. In particular, robotics has revolutionized manufacturing, allowing for greater output from fewer workers.
But while robotics has been making an impact for decades now, machine learning is just beginning to live up to its full potential. A 2017 survey by PWC found that only around half of all companies were already using it. Yet when implemented, machine learning can have a massive impact on companies’ bottom lines.
Ultimately, the biggest shift has been from a world where the business impact of machine learning has been largely theoretical to one where it is now quite real. The proven impact of machine learning models has pushed more investment toward their development. Still there are plenty more gains to be realized. To better understand the potential (and how you can harness it for your business), here are 6 ways machine learning is revolutionizing manufacturing.
1. Machine Learning is Revamping Quality Control
You’ve likely seen plenty of clips showing workers sifting through products whizzing by on an assembly line, looking for flaws. This is overwhelming and exhausting work, and you probably wonder how anyone can maintain the focus necessary to find small flaws for hours at a time. In a real world example, quality control was crippling GM throughout the 1970s. This led them to take the Toyota Manufacturing Technique and implement it in many of their factories.
Even when advanced manufacturing techniques are implemented, using humans to spot defects and errors is inherently limiting. Our senses and attention span simply have natural limits far below what machine sensors can offer. What does that difference add up to?
Forbes found that machine learning increased defect detection rates by up to 90%.
Quality control is often done by humans because it’s usually visual. If weight or shape is the main quality factor, it’s far easier for a machine task. Scanning for misaligned labels, off-colors, shine levels, and even cracks is fairly simple for a human but very difficult for a machine. Machine learning, however, allows algorithms to visually inspect products and identify flaws more quickly.
A case study involving steel manufacturing uncovered the impact that machine learning might have when defects are identified earlier in the process, leading to less waste. Factories are also able to efficiently identify possible causes of these defects. Besides the products themselves, machine learning can even improve the machines that make the products.
2. Machine Learning can Minimize Equipment Failures
Determining when to conduct maintenance on equipment is an exceptionally difficult task with huge stakes. Each time a machine is taken out for maintenance, it’s not doing its job and may even require factory downtime until it is repaired. Frequent fixes mean losses, and infrequent maintenance can lead to even more costly breakdowns. Global costs of equipment downtime adds up to $647 billion dollars annually. Looked at another way: The average international cost of said downtime is $5,600 per minute.
With those costs in mind, it’s no surprise that preventing even a single unplanned outage can pay for the cost of implementing machine learning. How does machine learning minimize these issues, exactly?
Machine learning algorithms are excellent at balancing multiple sources of data to predict and determine optimal repair time. This can be done simply by identifying errors and defects as they occur so they are addressed immediately – not once a human has discovered them at a later time. In addition, machine learning algorithms utilize historical data to identify patterns of equipment failure, helping them determine when regular maintenance should occur.
Data can also be taken automatically from inside the equipment, eliminating the need for a manual check. Increased speed and efficiency – plus decreased manpower costs – translate into substantial ROI for most firms, but the biggest gains come from a change in how maintenance is conducted.
3. Predictive Maintenance
This data boils down to a shift from reactive to proactive repair work. Generally, maintenance is conducted once a problem occurs, due to the high cost of taking equipment offline to have it manually checked for potential problems. When this occurs, managers constantly face an impossible choice: Take equipment offline and incur a loss now, or risk even greater losses down the line.
The role of machine learning is to identify the ideal moment to make that choice, and remove the costly and stressful guesswork. By using machine learning to predict when equipment breakdowns are likely to occur, your company can be far more proactive and ensure they are serviced before that happens. This results in fewer errors, less downtime, and lower human-capital costs because managers and other workers need to be less involved.
What do those benefits add up to? A recent study by Deloitte found that poor maintenance can decrease production by 5-20%. It’s clear that putting machine learning at the core of equipment care is essential to avoid costly inefficiencies.
The Advantages of Machine Learning Go Beyond the Factory
Even after machine learning has helped with quality control and machine maintenance, the resulting product still has a long way to go. For storing and shipping, machine learning has a role to play in identifying inefficiencies, and here’s how:
4. Supply Chain Optimization
Whether you’re looking at replacement parts for your factory equipment – or the products that equipment produces – reliable supply chains are essential for any manufacturing business. As the global economy becomes more complex, so does the challenge of optimizing these supply chains.
A single shift in weather, damaged ships, or change in fuel prices can reverberate throughout your supply chains, greatly impacting your business. Remember that the average time of equipment that’s down is $5,600 per minute. This cost applies just as much if you’re waiting for raw materials as if the equipment is broken.
Machine learning takes all of these complex factors into account and optimizes each element of your supply chain in response. This could mean calculating how much extra time to give a shipment (to account for the probability of a delay and/or its financial impact), or deciding where to ship a product from, based on possible weather patterns or other potential hurdles.
Put simply, a machine learning algorithm can take dozens – or even hundreds – of factors into consideration before making the best possible choice for your business.
The importance of minimizing these delays comes down to inventory and cash flow. If, for example, you can increase the efficiency of your supply chain by 10%, that means you can produce 10% more product while decreasing the level of unpredictability in the production process. Efficient and reliable production are essential for a successful manufacturing business, and machine learning makes both accessible in a way it never has been before.
5. Inventory Optimization
Closely connected with supply chain optimization, machine learning can have a similar impact on optimizing inventory. Holding costs (the cost of storing inventory) are massive, usually hovering around 20-30% of the cost of a product. Even a modest reduction of 10% in holding costs can reduce your per-unit costs by 2-3%. Holding unsold or undelivered products means paying for storage space. This may not sound like a major problem, but its effect on cash flow is immense.
Here, the role of machine learning is to calculate when it makes economic sense to hold on to or sell inventory, or even increase/reduce production of inventory. This is done by monitoring the supply chain elements mentioned above, as well as market prices, holding costs, and production capacity.
Carefully considering and balancing all of these elements has traditionally been a human’s job. With the ever-increasing amount of data reflected in each of these areas, however, humans are a poor choice for the task.
Therefore, the role of machine learning is an obvious one. By analyzing thousands or even millions of bits of information to make decisions, these algorithms go far beyond anything a human analyst is capable of. No surprise then that the results on overall efficiency can be substantial.
Factory-Wide Efficiency Gains from Machine Learning
There are also applications for machine learning that fall further outside of the areas already mentioned. Factories have more inputs than raw materials for production or information for analysis: Factories also run on commodities like electricity.
6. Using Machine Learning for Electricity Consumption
Obviously, one of the greatest inputs for any factory is electricity. While most factories operate 24 hours a day for optimal efficiency, it’s possible to schedule more energy-intensive activities for different times. The idea is to ensure those activities occur when power is cheapest. Depending on its source, this could be during the day (if solar power is prominent) or during the night (when demand is generally lower).
Of course, it’s not quite that simple. You obviously need to take a myriad of other factors into consideration. Once again, this is where machine learning’s ability to process large amounts of data comes into play. By considering energy prices alongside labor costs, equipment maintenance, and minimizing inventory, these algorithms can schedule the perfect time to perform energy-intensive activities for maximum cost savings.
Working backwards, this information can also allow you to intelligently invest in electrical infrastructure, whether that’s energy storage or solar power. Essentially, machine learning algorithms can allow you to precisely quantify the value of your factory’s electricity at any particular moment.
You can more precisely determine where such investments make sense, use your resources more strategically, and get more out of your factories.
Bringing Greater Efficiency to Every Area of Manufacturing
It’s not surprising that machine learning continues to impact manufacturing, but it might be more shocking that does so at nearly every stage. Machine learning can offer substantial cost savings in many areas, from buying raw materials to maintaining equipment. The flexibility of this technology explains its rise in popularity as it has become far more user friendly and less reliant on hiring teams of data scientists.
What’s stopping you from using machine learning today? RapidMiner makes data science more accessible than ever. Year after year, more case studies and research reports get published, providing concrete evidence for its benefits. The challenge is simply understanding how to best apply it to your business. We have lots of experience working with manufacturing organizations, but each company offers its own unique set of complexities and challenges so contact us about your use case and get started today.
The content & opinions in this article are the author’s and do not necessarily represent the views of ManufacturingTomorrow
Comments (0)
This post does not have any comments. Be the first to leave a comment below.
Featured Product
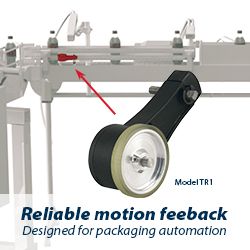