Specialty materials that have different mechanical, thermal, chemical, temperature, and conductive properties will continue to enable use cases where designs can be further optimized through the specification of specialty materials that best suit the part requirements.
Specialty Materials for 3D Printing
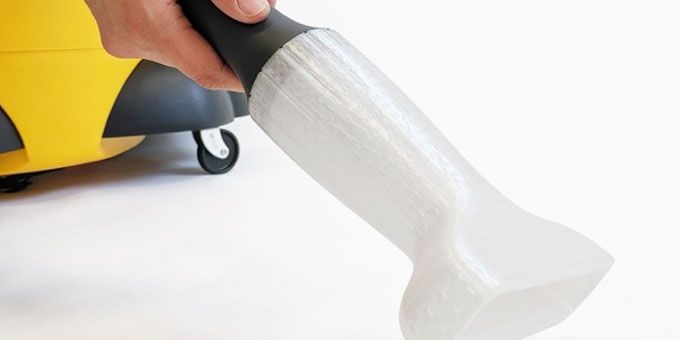
Dave Veisz, Vice President of Engineering | MakerBot
Tell us about MakerBot and your role with the company.
As the Vice President of Engineering at MakerBot, I oversee the hardware and software engineering teams. Founded in 2009, MakerBot is a global leader in 3D printing and a subsidiary of Stratasys Ltd (Nasdaq: SSYS). We also own and operate Thingiverse, the largest 3D printing community in the world.
Beyond 3D printing hardware, we have developed a full suite of connected solutions that address the wider needs of professionals and educators for an altogether better experience, evolving ideas from inspiration to innovation. Professional users are bolstered by seamless, cloud-enabled platforms, suited to their workflow and production needs, while educators can harness the largest collection of 3D printing lesson plans and ISTE-certified MakerBot Certification Program to help prepare students for the jobs of tomorrow.
How do Specialty Materials differ from other materials used for 3D Printing?
We offer two different lines of materials for the MakerBot METHOD - Specialty and Precision Materials. MakerBot Precision Materials are the primary materials developed for METHOD that cover the majority of use cases and are recommended as the default choice for most users. These materials have been extensively-tested for the highest reliability and measurably accurate parts. MakerBot Precision Materials currently include MakerBot Tough, MakerBot PLA, and MakerBot PVA.
Specialty Materials provide basic print performance and may require additional workflow steps to print successfully. PETG, for example, requires the application of adhesion stick to the build plate prior to printing. PETG is for users looking for advanced material properties, such as higher heat resistance, chemical resistance, and better durability.
Tell us about your product PETG
PETG is the first in a new line of Specialty Materials for the METHOD 3D Printer. PETG offers advanced mechanical properties, combining high toughness and durability with chemical and moisture resistance. PETG is designed to provide advanced material properties for engineers who demand even higher performance.
This industrial-grade material has a heat deflection temperature of 70°C and strong layer adhesion. PETG is resistant to moisture and many chemicals, including some alkali and acidic substances. It can be used with METHOD’s water-soluble PVA for complex parts and effortless support removal.
PETG has greater strength and flexibility qualities than other materials, such as PLA and ABS, and is odorless when printing. Further, the material prints with a glossy finish and has a good degree of ductility.
Why did you decide to develop PETG as your first Specialty Material?
Our customers have been asking for different materials to use for a wide range of applications that require high strength and durability. PETG is one of the most widely used polymers today. Because of its advanced properties and versatility, we view PETG as an excellent material to be used on the manufacturing line and for short-run production parts.
What types of applications are best suited for PETG?
PETG can be used for functional prototypes, jigs & fixtures, and end-use parts that need to withstand a high degree of wear, moisture, or chemicals. It can also be used for parts that require higher heat resistance than PLA or Tough PLA. The ductility of the material works well for fitted parts, snap fits, or living hinges. Customers have used PETG for parts that contact coolant in CNC machines where other plastics would break down over time.
What are its advantages over other materials?
Comparing PETG against PLA and Tough, PETG has improved mechanical and thermal properties. It has a higher heat deflection temperature than PLA and Tough (70C vs. ~49C). PETG also has better chemical and moisture resistance and is very durable. It has a glossy finish and a good degree of ductility. PETG has greater strength and flexibility qualities than Tough and PLA, and is odorless when printing.
What should engineers consider when deciding which material to use?
There are several factors that you should consider before selecting a material for your project, including application, function, aesthetics, and timing. For example, if you’re producing a water bottle or food container, you would need a material that has excellent chemical and moisture resistance properties, like PETG. But if you’re prototyping a concept, you won’t necessarily need expensive materials like metals; you would simply need materials that have similar properties as that of your end product. This will give you an idea of the look and feel of the end product without having production become costly or time consuming. Ultimately, your project needs will dictate your material needs.
Over the last several years how has 3D printing changed the way engineers prototype?
With the proliferation of desktop 3D printers, 3D printing has become much more accessible and easier-to-use. More engineers and designers have easier and immediate access to a 3D printer to test their ideas. This has opened opportunities for hardware companies to design, test, and iterate their innovations faster than before.
Previously, businesses heavily relied on expensive industrial 3D printers which can be large, bulky, and costly; or they would need to outsource their 3D printing needs to service bureaus, which can also be time-consuming. However, as the demands of hardware companies evolved, so did desktop 3D printers. Current desktop 3D printers are insufficient for manufacturing needs; they do not deliver the accuracy or precision that industrial-grade 3D printers do and that engineers need.
We engineered the MakerBot METHOD to deliver industrial precision and reliability in an accessible form and at a significantly lower cost than industrial machines. METHOD leverages industrial technologies and expertise from Stratasys and combines it with the accessibility and ease of use for which MakerBot is known. By providing engineers with direct and immediate access to an industrial 3D printer, they can design and create better products in the future.
Look down the road a few years, how do you see Specialty Materials changing how we manufacture.
With new materials, come new use cases. The capabilities of FDM 3D printing changes the traditional rules of design; you can now design parts with voids, living hinges, and other complex geometries that are simply not possible to create with traditional manufacturing methods. Specialty materials that have different mechanical, thermal, chemical, temperature, and conductive properties will continue to enable use cases where designs can be further optimized through the specification of specialty materials that best suit the part requirements. Material advances plus the design freedom that 3D printing provides will enable another level of optimization.
The content & opinions in this article are the author’s and do not necessarily represent the views of ManufacturingTomorrow
Comments (0)
This post does not have any comments. Be the first to leave a comment below.
Featured Product
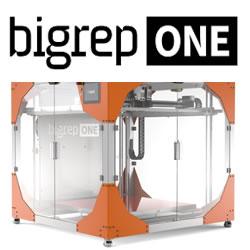