Ensuring compliance with an electrical safety program isn’t always easy, but there are plenty of tools available to help you succeed.
How to Ensure Your Electrical Safety Program is Driving Compliance in 2019
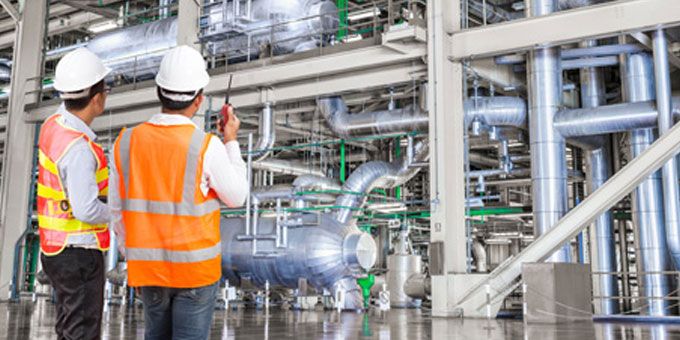
Karen Dziekan | Panduit
As a safety manager, your job is not only to be prepared and consistent with regards to all aspects of plant safety, but also to make sure that everyone else – from management through to janitorial and office staff – prioritize safety as much as you do. Being proactive will result in your facility being in compliance – or not – as well helping to avoid serious injuries and fatalities around the workplace.
A good place to begin preparation is in places that are frequently overlooked. OSHA’s top cited violations tell us that electrical safety falls into this category. Being knowledgeable on the latest updated standards can help modernize your electrical safety programs, while also providing opportunities to address evolving safety concerns with employees so that all are up-to-date on best practices in electrical safety and incidents are avoided.
As one example, OSHA found failing to properly control energy accounted for nearly 10 percent of serious accidents in many industries. Realizing that its existing measures weren’t enough, OSHA recommended the creation of NFPA 70E, a requirement for safe work practices to protect personnel by reducing exposure to major electrical hazards.
OSHA’s general duty clause requires facilities to provide employees with a place of employment that is “free from recognized hazards that are causing or are likely to cause death or serious harm.” While NFPA 70E is a voluntary standard, with its compliance not required by law, it effectively describes electrical hazards and best practices to mitigate them. Because OSHA regulations are not frequently updated, they will often reference consensus standards such as NFPA 70E as a best practice when issuing citations to the general duty clause.
Implementing NFPA 70E In Your Facility
NFPA 70E helps facilities and employees avoid workplace injuries and fatalities due to shock, electrocution, arc flash, and arc blast during maintenance and construction in industrial plants. There are a couple of areas where you will need to update training procedures within your facility in order to comply with NFPA 70E:
Lockout/Tagout (LOTO). Every year workers are unnecessarily exposed to hazardous energy sources during servicing, maintenance, or setting up equipment. By implementing a lockout device to ensure that equipment on the energy isolating device cannot be operated until the lockout device is removed and a tagout device to indicate that an energy isolating device may not be operated until the tagout device is removed, risks such as injuries, asset damage and production downtime are diminished.
When it comes to implementing a LOTO program to adhere to NFPA 70E, three types of employees need to be covered:
- Authorized Employees are responsible for implementing energy control procedures and performing the required servicing or maintenance. Training for Authorized Employees includes details about the type and magnitude of the hazardous energy sources present at the facility, and the methods for isolating and controlling these energy sources. Authorized Employees must also receive training on machine-specific procedures.
- Affected Employees operate equipment or work in an area in which an energy control procedure is being implemented. Affected employees are not themselves responsible for locking and tagging out, but must understand their purpose in order to avoid attempts to start up or use equipment during these procedures.
- Other Employees include office or warehouse personnel who may work in an area where an energy control procedure is utilized.
Verifying Absence of Voltage. When electrical maintenance is needed, NFPA 70E requires that workers establish and verify equipment is in an electrically safe state. This involves a test for absence of voltage. Although NFPA 70E is comprehensive around LOTO guidelines and the need to first verify the absence of voltage, it does not articulate the removal of hazards before this maintenance or inspection begins, therefore increasing risk to the electrician. Eliminating a hazard is the most effective method according to the hierarchy of controls, and should be the first choice whenever possible. NFPA 70E emphasizes the need to work on electrical systems only when they are placed in an electrically safe working condition, but creating and verifying this condition requires more than just de-energizing, as it involves multiple steps to confirm the system is safe and to verify the absence of voltage.
Absence of Voltage Testers (AVTs) are permanently-mounted testing devices that are specifically designed to determine if a circuit part is de-energized prior to opening panels or removing covers to access and maintain electrical equipment. They are designed to automatically run internal diagnostics and administer the live-dead-live type of verification testing with an internal known voltage source and actively indicate the absence of voltage. AVTs also help improve electrical safety through a Prevention through Design approach, making them an ideal option for maintenance and service professionals.
While training can deliver the results a facility is looking for, every plant is different and safety professionals should seek out third-party support in order to better understand the latest standards that can keep them in compliance. For more information on best practices for implementing a modernized safety program, read our new eBook How Understanding the Hierarchy of Controls can Lead to Reduced Electrical Incidents.
The content & opinions in this article are the author’s and do not necessarily represent the views of ManufacturingTomorrow
Comments (0)
This post does not have any comments. Be the first to leave a comment below.
Featured Product
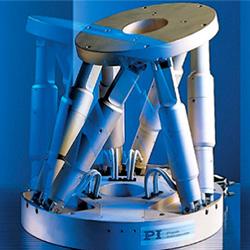