Digitization is transforming every industry, but perhaps none more so than manufacturing and logistics. In detail-oriented industries like these, any technology that promises to improve efficiency, transparency, and consistency is immediately intriguing.
Think Smart, Think Agile: A Guide to Using Tech to Solve Supply Chain Problems
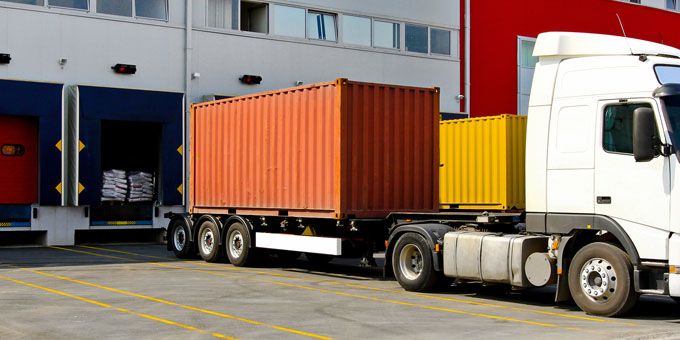
Bhaskar Ballapragada | ThroughPut Inc.
Digitization is transforming every industry, but perhaps none more so than manufacturing and logistics. In detail-oriented industries like these, any technology that promises to improve efficiency, transparency, and consistency is immediately intriguing. Therefore, it’s not surprising that industries invested in supply chains have been quick to embrace advances like artificial intelligence and the Industrial Internet of Things.
In a recent Deloitte survey, 62% of respondents said the supply chain was the top priority for digital investment. As more companies have undergone digital transformation, embracing new technologies has become a competitive necessity. What often gets overlooked, however, is that simply implementing as many new technologies as possible is not the formula for a successful digital transformation.
In fact, having too many of the wrong technologies can completely derail a transformation.
Learning From GE's Mistakes
General Electric undertook one of the largest digital transformation efforts ever starting several years ago. One division within the company — GE Digital — was responsible for driving transformation in every other aspect of the company. It was an ambitious undertaking that eventually became a notorious failure.
The plan was for GE Digital to create applications in-house that could boost return on investment and drive business differentiation. Instead, the effort caused revenues at GE to fall from $124 billion in 2017 to a projected $12 billion in 2020. One initiative, in particular, ate up $4 billion in development costs before being put on an indefinite hiatus. Amid all this turmoil, CEO Jeff Immelt resigned. The great irony is that in trying to transform for the future, GE put its own survival in jeopardy.
The various reasons GE failed are complicated, but many of them stem from a lack of focus and planning. When one business unit is responsible for transforming a massive global company, it’s predictable that the scale of the effort could be overwhelming.
For better or for worse, shortsighted digital transformation efforts are not unique to GE. One study found that companies have an average of 29 digitization projects in the idea, proof-of-concept, or pilot stages, but only 14% have managed to move projects beyond the pre-deployment stage. Like GE, lots of digital transformation efforts start strong before stalling out.
Instead of trying to transform as quickly as possible, companies should be cautious and calculated about it. That means adding only the technologies that are necessary and manageable. Just as importantly, it means avoiding technologies that are extraneous or inhibiting.
When Technology Is an Obstacle
It's not uncommon to have several technologies, platforms, and frameworks in the news at any given time, with each one of them being the next big thing and having significant hype about its potential. In some cases, it’s true, but in many more cases, it’s inflated or outright false. More importantly, the real business value behind these are unclear, and they are implemented by IT teams without a real in-depth understanding of domain knowledge. Following is a list of a few technologies that have been, in my opinion, a distraction to the success of digital transformation:
Radio frequency identification technology is a great example. It promises to offer end-to-end visibility across a supply chain, yet installing all the necessary technology is a huge undertaking with significant costs. RFID has undeniable potential, but only if the problems of scale can be overcome.
Augmented reality faces a similar problem. Some companies use this technology with individual technicians or in a single facility, but none have managed to deploy AR across the entire supply chain. The inherent software and hardware challenges make widespread deployment difficult, meaning that AR can offer benefits but can’t anchor a digital transformation.
Blockchain is more scalable, owing to the fact that it requires no hardware. However, supply chain managers have been slow to embrace this distributed ledger technology because it’s incompatible with many of their legacy systems and data silos. Until those are replaced and broken down, blockchain is not especially viable. Realistically, this technology is a product of digital transformation, not a driver of it.
That said, achieving digital transformation is less about the technologies companies implement and more about the strategy they adopt. Instead of adding things to the supply chain, the focus should be on taking baby steps, an agile approach to solve existing problems using existing data.
Making Meaningful Improvements to Supply Chains
Remember that digital transformation is not a goal in and of itself. Companies are pursuing digitization to become better, not to become more tech-dependent. It’s incumbent on all supply chain managers to look beyond the latest innovations in favor of engineering improvements through whatever means are available. Follow these strategies:
1. Select the KPIs.
There is no way to track the progress of a digital transformation unless there are targets set for key performance indicators. Begin by identifying the metrics that reveal whether the transformation is working based on the company’s long-term goals. Then, decide on targets that are ambitious and realistic based on the amount of resources available. Once the decisions are made, companies gain true visibility into the supply chain.
2. Choose technology wisely.
Before deciding to implement any new technology, it should be evaluated according to two criteria. First, explore whether the technology is really the premier solution or something older or simpler could be just as effective at a lower cost — for example, predicting machine maintenance using inspections instead of AI. Second, consider whether the technology is scalable and customizable. Given the dynamic nature of digitization, any new technology must be able to grow and adapt to continue delivering value.
3. Collect data effectively.
Evaluating supply chain performance requires massive amounts of data at every step along the way. If the data is being sent off to a silo and updated infrequently, decision makers will struggle to understand the supply chain. Digital transformation can only succeed if companies can learn to collect more data, integrate it in one place, and update it in real time. It requires technological solutions, as well as plans, policies, and the right talent.
4. Identify all bottlenecks.
All resources need to be directed toward bottleneck areas; otherwise, they won’t improve KPIs. Bottlenecks can exist in multiple locations and be hard to identify, which is why companies should systematically root them out. If no bottlenecks exist, create one by increasing performance targets. The goal is to find all the stress points within the supply chain.
Technology has (and will) revolutionize supply chains, but it’s essential to remember that no one has invented a panacea yet. The problems remain the same, and the solutions are just as elusive. Even as technology offers new capabilities, it will always be up to supply chain managers to solve the core problems.
About Bhaskar Ballapragada
Bhaskar Ballapragada is chief architect at ThroughPut Inc. Bhaskar leads product- and technology-related initiatives and helps companies detect, prioritize, and alleviate dynamic operational bottlenecks by applying machine learning algorithms.
The content & opinions in this article are the author’s and do not necessarily represent the views of ManufacturingTomorrow
Comments (0)
This post does not have any comments. Be the first to leave a comment below.
Featured Product
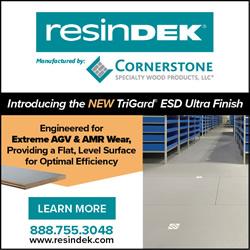