Adding two axes to the conventional three axes does technically create a machine with five axes, but this 3+2 mechanism does not exactly equal a 5-Axis machine.
3+2 Vs. 5-axis: What’s the Difference?
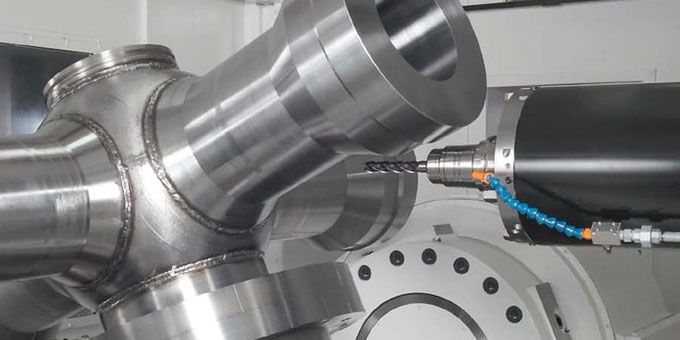
Contributed by | Okuma
For over a century, conventional machining has utilized three dimensions: the X-axis, the Y-axis and the Z-Axis. Using this type of movement to remove material is arguably still the most popular way to produce products in the milling field. However, in the last few decades, machinists have developed more advanced and productive ways to produce parts, including 3+2 and simultaneous 5-Axis machining. The following is everything you need to get comfortable with the difference between 3+2 and simultaneous 5-Axis, so that you can decide what’s most profitable for your operation.
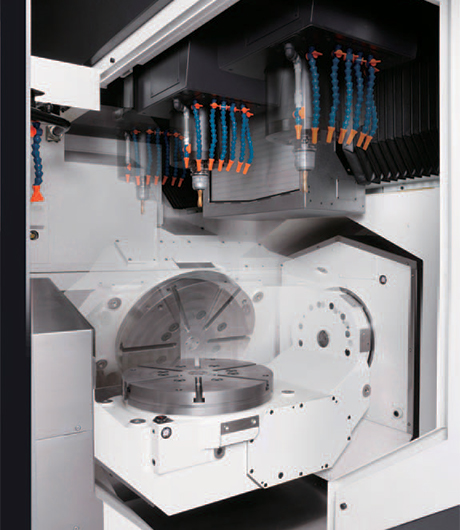
Adding two axes to the conventional three axes does technically create a machine with five axes, but this 3+2 mechanism does not exactly equal a 5-Axis machine. While this may sound illogical at first, don’t worry – this blog post has everything you need to get comfortable with the difference between 3+2 and 5-Axis, so that you can decide what’s most profitable for your operation.
3+2 MACHINING
Vertical machines are typically used to reach the three traditional axes, but over the years, products like rotary tables and tilt-rotary trunnions have been added to create movement on an additional two rotary axes (chosen from the A, B and C axes) resulting in a 3+2 axes operation. This process is also referred to as positional five-axis machining because the fourth and fifth rotary axes keep the part in a fixed orientation, then typical 3 Axis machining can be carried out, instead of moving it continuously during the machining process (as in the simultaneous 5-Axis process – see below).
The main advantage to adding a 3+2 setup to your current vertical machine is that it allows a workpiece to be machined from all sides. This reduces the need for additional set ups thereby lowering the cycle time and reducing costs. 3+2 can also use a shorter, more rigid cutting tool than a regular three-axis machining, resulting in greater dimensional stability.
SIMULTANEOUS 5-AXIS MACHINING
5-Axis machines, also known as simultaneous 5-Axis, move the cutting tool on the X, Y and Z axes and rotate the A, B and C axes to maintain continuous contact between the tool and work piece, unlike 3+2 operations, where the part is in a fixed orientation.
Why swap out your rotary table for an integrated 5-Axis machine?
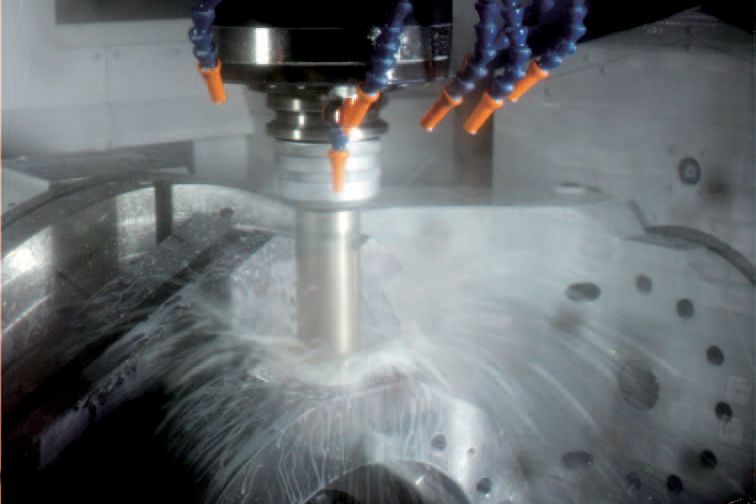
Think of it this way: as technology progresses, it makes our lives easier. For example, as smartphone apps developed, they enhanced our everyday processes. They’ve made things like directions, high-quality photography and the internet user-friendly and simple. The latest simultaneous 5-Axis machines are not much different. As 5-Axis technology continues to grow and develop, it makes the 5-Axis process easier to navigate. A designated 5-Axis machine is built not only to handle, but constantly improve upon the 5-Axis process. They’re also less complicated to operate because the “bells and whistles” are built in.
With 5-Axis machines you can use standard length tools, which increases tool rigidity, leads to higher feed rates and longer tool life, helping you cut costs in tool turnover and insert replacement. Your machine’s accuracy is greatly improved through Okuma’s 5-Axis autotuning, giving you a “done in one” set up process. Accuracy also means less scrap, so your shop produces less waste. That minimized set up also increases speed and relies much less heavily on human interreference, cutting out the dire need for skilled individuals. A major plus: 5-Axis machines give your shop a competitive edge and show the consumer you’re able to do more, accurately, at a quicker pace.
There aren’t many disadvantages to using simultaneous 5-Axis, especially with the advancements that these machines have made in the last decade. Price is one of the main concerns we receive, but at the end of the day the return far outweighs the benefits.
The content & opinions in this article are the author’s and do not necessarily represent the views of ManufacturingTomorrow
Comments (0)
This post does not have any comments. Be the first to leave a comment below.
Featured Product
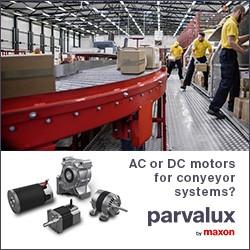