Knowing which method of preventative maintenance to use isn’t always a straightforward decision. Depending on the complexity and value of your equipment and the possibility of compliance requirements, you might use more than one approach.
5 Types Of Preventative Maintenance In Commercial Facilities
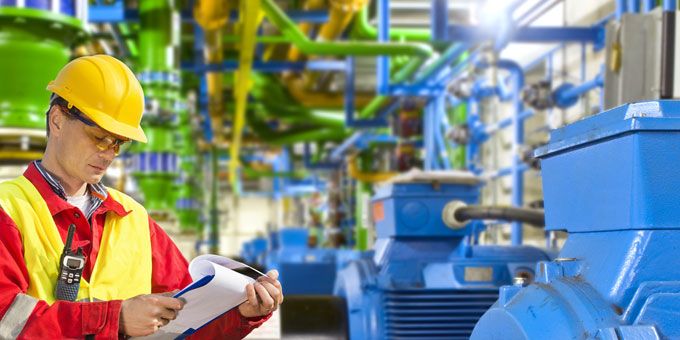
Cem Alptekin | Iota Communications
We’ve talked about preventative maintenance before on our blog, and where it stands on the continuum relative to other types of maintenance. But that’s not the end of the story; there are different approaches to preventative maintenance itself, all of which are used to ensure your equipment is operating correctly and potential problems are identified.
Knowing which method of preventative maintenance to use isn’t always a straightforward decision. Depending on the complexity and value of your equipment and the possibility of compliance requirements, you might use more than one approach. Below are the five common types of preventative maintenance in use at commercial facilities today, along with some preventative maintenance examples.
Time-based Maintenance (TBM)
When you change an air filter once every six months, you’re practicing time-based maintenance. Time-based maintenance activities might involve anything from inspecting and cleaning to servicing and part replacements. The frequency of TBM is usually predetermined according to the equipment supplier’s recommendations and/or past performance of the machine.
TBM has some advantages and disadvantages as a maintenance strategy. It uses less manpower than some other maintenance strategies. But even though you’re following the set schedule, in some cases you may be changing or servicing something before it actually needs to be done. For example, a manufacturer may recommend replacing a fan filter every three months, but if that filter is located in an area of the building where it isn’t used often, you could go longer without replacing it. That makes the cost of TBM higher than it should be.
Another maintenance strategy, condition-based monitoring (discussed below) can help prevent over-maintenance, and is seen as generally more valuable and economical than TBM.
Failure-finding Maintenance
Failure-finding maintenance is conducted to ensure that something—often a protective device of some sort—still works. Protective devices are those designed to call attention to a problem, shutdown a process to prevent further problems, and guard against accidents. Activating an alarm occasionally would be considered failure finding maintenance.
While other types of preventative maintenance involve regularly changing or replacing parts, or noticing an apparent condition that might indicate imminent failure, failure-finding maintenance applies to hidden failures that can be uncovered only by actually checking if something still works. By some estimates, up to 40 percent of failures in industrial settings fall into the hidden category; and up to 80 percent of those require failure-finding to be rooted out. An example of this type of preventative maintenance: A diesel generator might have a protective device that should shut down the generator in the event of elevated cooling water temperature; the functionality of that device will not be discovered without simulating the appropriate conditions and checking if the device gives the right response.
Unfortunately, failure-finding maintenance is usually given low priority by maintenance professionals, but it is critical to maintaining a safe environment—and sometimes preventing the major disasters that happen as a result of multiple failures.
Risk-based Maintenance
Risk-based maintenance is a strategy that aims to decrease mechanical failures by evaluating the levels of risk associated with your equipment, and then prioritizing your maintenance activities accordingly. The theory behind risk-based maintenance is essentially Pareto’s Law, which, when applied to maintenance, holds that 80 percent of failures are attributable to just 20 percent of your equipment; therefore it makes sense to focus your efforts on those areas.
Both the probability of a failure and the consequences of a failure are considered in support of this approach. Based on the results of your evaluation, you can make better decisions about what to inspect, and when. Many times facility managers do this unconsciously as part of their routines, but it’s more effective at delivering results when a methodology is used to help make decisions. When done right, risk-based maintenance can optimize both asset performance and your financial resources as well.
Condition-based Monitoring (CBM)
Condition-based monitoring involves monitoring the condition of a piece of operating equipment or machinery to determine what type of maintenance needs to be done and when. Signs of declining performance or imminent failure would indicate maintenance needs to be done to restore the machine to its previous level of performance and reliability. This approach is designed to avoid a breakdown by fixing problems before they occur, which means it is a type of predictive maintenance (number 5 below).
CBM is a more effective preventative maintenance strategy than time-based, because it is a proactive measure intended to specifically identify changes in machine performance and head off issues.
Examples of what elements could be monitored to diagnose problems are:
⦁ Visual—This is the most basic form of condition monitoring and may uncover things like cracks or corrosion.
⦁ Vibrations—Changes in the vibrations produced by compressors, pumps, motors and other types of equipment can help spot performance problems.
⦁ Wear debris (tribology)—Analyzing interacting machine surfaces for wear and fractures may serve as an early warning of equipment failure.
⦁ Temperature (thermography)—Corroded electrical connections, faulty machinery, and damaged machine components can all change the temperature distribution of running equipment.
⦁ Sound—The sound of a running machine is usually fairly stable; a change in the noise signal may indicate a change in the condition of the machine.
Predictive Maintenance
Predictive maintenance is pinpointing when a piece of equipment is likely to fail and addressing it before it happens. Rather than simply aiming to minimize downtime, predictive maintenance aims to maximize uptime. It’s an improvement over traditional preventative maintenance approaches because it helps prevent failures in a timely manner.
It’s very similar to condition monitoring in that both strategies have the same goal. The difference is that condition monitoring identifies immediate tasks based on monitoring results, while predictive maintenance helps you plan maintenance tasks based on knowledge about overall equipment health and expected performance—knowledge that comes through the gathering and analysis of data.
The Internet of Things makes predictive analytics possible. Sensors attached to your machines and equipment monitor and collect a broad range of operational data, on everything from vibrations, sights, and sounds to temperatures and power consumption. With the help of machine learning and algorithms, this data can then be mined and patterns identified. Eventually, that data can be used to provide valuable insights about aberrant performance that could indicate the likelihood of an imminent breakdown.
As an example of this type of preventative maintenance, consider a commercial refrigerated unit. A manufacturer that owns numerous commercial refrigerated units around the country needs a reliable way to prevent the units from failing because there are high costs associated with failure—including the cost of emergency repairs and product spoilage. As part of a predictive maintenance strategy, the manufacturer could equip each of the refrigerated units with a variety of sensors. The sensors would measure:
⦁ Refrigerator temperature
⦁ Humidity level
⦁ Temperature of the coolant going into and out of the compressor
⦁ Temperature of the coolant going into and out of the evaporator
⦁ Vibration on the compressor
⦁ The number of times the compressor starts and stops
⦁ How long the compressor runs
⦁ The amount of power the compressor is using
All this data could be stored and analyzed using an Internet of Things platform. Using predictive analytics, it’s possible to understand the optimal performance of a refrigerator unit and, when anomalies in the data arise, to determine if and when the unit might fail. The problem can then be addressed before it happens.
Paired with your critical assets, sensors can give you an unprecedented level of insight into your daily operations that supports your equipment—and your building—better than preventive maintenance. Predictive maintenance can significantly reduce downtime, decrease your financial expenditure by prolonging the life of your equipment, and increase the overall safety of your operation.
Move Toward A Predictive Maintenance Strategy
Would you like to get started with predictive maintenance but aren’t sure how? Talk to the folks at Iota. They can help your company get all the information you need from your important assets so you can predict and prevent failures before they happen.Iota’s line of IoT sensors enables you to remotely monitor your equipment, providing precise measurements about the aspect of operations you’re most interested in. They also offer a subscription-based service of predictive analytics and machine learning algorithms designed to help you optimize equipment performance through fault and anomaly detection. Contact Iota to get started with better monitoring and management today.
The content & opinions in this article are the author’s and do not necessarily represent the views of ManufacturingTomorrow
Comments (0)
This post does not have any comments. Be the first to leave a comment below.
Featured Product
