The complex, large parts on the motorcycle proved difficult to manufacture. Curtiss’ CNC suppliers quoted long lead times and had trouble delivering on the uncompromising design and quality requirements.
Making a Game-changing Electric Motorcycle With Hybrid Manufacturing
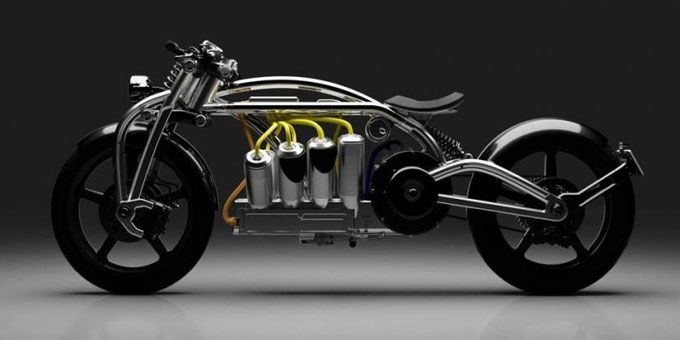
Case Study from | Fast Radius
With its sweeping chromoly frame and eight banks of sleek, visible battery cylinders, the Zeus 8 electric motorcycle from Curtiss would be unlike anything the market had ever seen. Curtiss planned a major launch event to unveil the bike, but they ran into challenges sourcing parts for the prototype.
The complex, large parts on the motorcycle proved difficult to manufacture. Curtiss’ CNC suppliers quoted long lead times and had trouble delivering on the uncompromising design and quality requirements. With the Zeus 8 launch event approaching, Curtiss needed a partner who could get their unique bike into production quickly.
Enter Fast Radius, a leading provider of comprehensive hybrid manufacturing solutions. Curtiss was able to make their stunning motorcycle on time by leveraging three of Fast Radius’ core areas of expertise:
- Application engineering
- Hybrid manufacturing
- Operational efficiency
Application engineering
The expert application engineers at Fast Radius work with customers to optimize their designs for any manufacturing technology. In the case of the Zeus 8, Curtiss’ team designed large, sleek parts to make the bike so distinctive. Producing those parts, however, was challenging: most CNC machines couldn’t create parts as large as Curtiss needed, but making and assembling smaller pieces into a larger part wouldn’t give the bike the polished, dramatic look it needed. To solve this, the engineers at Fast Radius worked with Curtiss to make their designs ready for manufacturing. Together, they created parts that could be manufactured while still adhering to Curtiss’ high design standard.
Hybrid manufacturing
Fast Radius evaluates each application separately to determine the best way to make it. Five-axis CNC milling was the best way to produce large parts for the Zeus 8, but there were many smaller parts that also needed manufacturing solutions. Rather than pushing Curtiss toward a single manufacturing process, the Fast Radius team evaluated all of the part requirements and created a hybrid solution that comprised three separate production processes, including legacy and additive methods.
Curtiss is eager to innovate further with Fast Radius. The two companies are currently exploring parts on the motorcycle that could be made additively. For example, the seat and handle grips of the Zeus 8 motorcycle might be designed and engineered using industrial-grade 3D printing technology.
Operational efficiency
After Curtiss and Fast Radius completed designs and chose the appropriate technology for each part, they moved into production immediately to meet Curtiss’ approaching deadline. Thanks to Fast Radius’ lean manufacturing model and project management expertise, the parts were produced in only 12 days, a full two days faster than any other supplier could offer. Fast Radius has such quick turnaround times because they are committed to getting parts right the first time. In the case of the Zeus 8, Fast Radius produced 60 parts and components that maintained better than 95% first-pass yield. This efficiency saves customers money, too, by eliminating the need for costly part revisions.
Conclusion
Impressed by what they saw with the Zeus 8, Curtiss engaged Fast Radius in an ongoing partnership to make parts for their entire line of luxury electric motorcycles. “Fast Radius can get us the best parts with the shortest lead times, but that’s not the only reason we partner with them,” said Curtiss CEO and Chairman, H. Matthew Chambers. “We work with Fast Radius because they push us toward the cutting edge of manufacturing technology. We’re creating the most advanced motorcycles the world has ever seen, and Fast Radius is committed to making our vision a reality.”
The combination of engineering knowledge, advanced manufacturing expertise, and operational efficiency made Fast Radius the partner Curtiss needed to get its exceptional motorcycles to market quickly.
The content & opinions in this article are the author’s and do not necessarily represent the views of ManufacturingTomorrow
Comments (0)
This post does not have any comments. Be the first to leave a comment below.
Featured Product
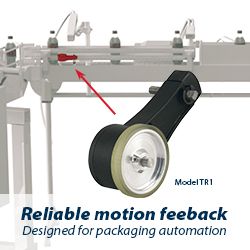