Booth C-3238. This year Butler is showcasing our Ease of Use Enhancements on our core product – the SP1 Automatic Splicer.
PACK EXPO Q&A with | Butler Automatic
Tell us about your company
Butler Automatic builds automatic roll splicers for packaging applications. Butler splicers eliminate roll change downtime, which is the largest contributor to bagging, pouching, or thermoform line output loss. This means our customers can increase their output by as much as 15 percentage points while significantly reducing their process waste. As the leader in providing Overall Equipment Effectiveness (OEE) solutions for the packaging industry through automatic roll splicing, Butler Automatic has been improving overall factory output for its customers for more than 60 years.
With over 17,000 automatic splicers installed worldwide, Butler is a global packaging equipment benchmark for effective design, quality build, and reliable performance. Butler utilizes OPL’s (One Point Lessons) and CIL’s (Clean-Inspect-Lubricate Instructions) to help our customers train staff and maintain their equipment. Leveraging these simple guidelines and clearly defined maintenance procedures are key to long term reliability and consistent automatic splicing performance.
Our global presence is evenly split between US and International customers. Over 2,000 Butler splicer systems are installed on flexible packaging applications, such as horizontal and vertical form fill seal (pouching and bagging), thermoforming, flow wrapping and shrink sleeve lines. Butler partners with more than fifty packaging equipment OEMs, and provides automatic roll splicing solutions to brand owners, copackers and manufactured goods producers in the Food, Dairy, Snack, Pet Food, Beverage, and Pharmaceutical sectors. Butler provides solutions for flexible packaging converting operations as well.
Your company will be exhibiting at PACK Expo, what is it that makes this an important event for your company?
One of the many reasons Butler Automatic exhibits at Pack Expo is because the show provides the largest platform to reach potential customers. The show assembles nearly 30,000 packaging professionals, all of whom are wanting to stay abreast of the newest technology and trends while searching for solutions to their packaging needs. Since Butler’s automatic splicing solutions improve OEE (Overall Equipment Effectiveness) for and roll-fed packaging applications, it is important for Butler to be seen by both OEM’s and end users. Our message of improving overall factory output for Co-Packers, VFFS, HFFS, Thermoform and Shrink Sleeve applications is important to share with the industry. Exhibiting at Pack Expo delivers our message to target customers.
What makes your booth a must visit for PACK Expo Attendees?
This year Butler is showcasing our Ease of Use Enhancements on our core product – the SP1 Automatic Splicer. These design improvements and features include new HMI graphics, air intake and splice prepared monitoring, web break detection and web stop, omni-directional adjustable brackets for core sensors, adjustable integrated exit idlers, base mounted automatic web alignment, sealed stainless steel roller bearings, and a more robust nip assembly.
These improvements were designed and implemented in order to make the operator/machine interaction simpler, reduce training and maintenance time, and improve OEE (Overall Equipment Effectiveness) in our end user’s packaging lines. The new HMI graphics include enhanced visual feedback on the process and recovery instructions making operation and problem recovery easier. The web break detection, air and splice monitoring reduce operator error caused downtime. The sealed stainless steel bearings reduce maintenance time.
Mike Mucci, Vice President of Engineering, states that these product improvements “are the result of listening to our customers and Butler Automatic’s drive to design, deliver and support automatic roll splicing solutions which are easy to use, reliable, and perform consistently.”
When you get a chance to walk the exhibit hall floor yourself, what is it you will be most interested to see? Any educational sessions, pavilions etc. you plan on attending?
It is always great to see what other OEMs are developing and how they are solving industry wide issues such as simplified user interfaces, hygienic design, ease of use issues, and automation. It’s also interesting to see the trend towards flexible packaging and stand up pouching.
The factory floor is undertaking rapid advancements, be it automation, robotics, machine vision or data. Automation Technology is a huge part for many manufacturers, give us an idea on how your company and product is being utilized now in the smart factory.
Butler splicers eliminate downtime when changing a roll on any roll fed process. Automating this process allows for factory operators to set up a splice for a roll change when there is time available, thus saving operator time while eliminating downtime. Automatic splicing also allows for the use of “short rolls” at no extra labor or downtime cost, reducing waste. A third benefit is that process change-overs (ie size changes) can be done with no roll change downtime.
All three of these benefits allow the new “smart factory” to operate more efficiently.
Give us your thoughts on what the future holds for manufacturers and automation technology.
The future is eliminating downtime and reducing operator and maintenance labor. Butler splicers do this by design.
The content & opinions in this article are the author’s and do not necessarily represent the views of ManufacturingTomorrow
Comments (0)
This post does not have any comments. Be the first to leave a comment below.
Featured Product
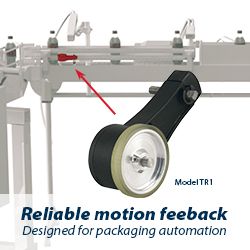