Michael Davies, Iota Communications: Even if you’re already practicing preventive maintenance, there’s still more you can do to maximize equipment uptime and utilization rates. In this article we’ll cover the basics.
What Is Preventive Maintenance?
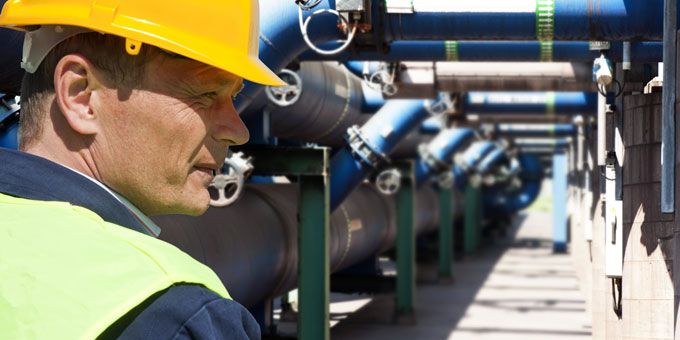
Michael Davies | Iota Communications
Which of these scenarios best describes your building’s maintenance program?
-
Reliant on a paper management system, your workers spend most of their time performing failure maintenance tasks—unscheduled activities done in response to equipment malfunctions.
-
Largely digital-based, your maintenance program consists primarily of scheduled maintenance activities and only small amounts of time are spent addressing equipment failures.
If you answered scenario #2, congratulations—you’re already practicing some level of preventive maintenance that’s helping to minimize firefighting. If you said scenario #1, it’s time to rethink your maintenance strategy altogether.
Even if you’re already practicing preventive maintenance, there’s still more you can do to maximize equipment uptime and utilization rates. In this article we’ll cover the basics: what preventive maintenance is, an example of how it works, and, for those of you looking for ways to improve your program, how to be even more proactive using predictive maintenance.
What is preventive maintenance?
The specific definition of preventive maintenance varies from one person to the next, but the meaning of the term is the same: It is scheduled maintenance and inspections with the dual purposes of ensuring equipment is operating correctly and identifying potential problems to minimize equipment failures.
To get an idea of what is meant by preventive maintenance, this gradient scale positions it relative to other kinds of maintenance:
-
Reactive maintenance (also known as breakdown maintenance or “run to fail”) focuses on repairing and restoring assets in response to breakdowns that have already occurred.
-
Preventive maintenance is a strategy focused on maintaining the continual operation of machines and equipment through regular inspections and, to the extent possible, identifying and anticipating problems that may be imminent, then addressing them proactively.
-
Predictive maintenance is an advanced strategy that uses data analytics to predict equipment failures in advance and prescribing remedies to address them.
Many maintenance teams use a combination of reactive and preventive maintenance; a small number are also utilizing some level of predictive maintenance. Best practices suggest that 30 percent of all maintenance work should be preventive, though top-notch building operators strive to increase that to 60 to 80 percent or more.
Contrary to what building operators might think, reactive maintenance is costlier than it seems. There’s no outlay of financial resources while an asset is still operational. But the cost of fixing something at the last minute is exponentially higher than what you would spend to maintain its continuous operation, thanks to emergency repair costs and the business downtime you’re likely to incur. (In a lot of ways, this gradient can be viewed in terms of the 1-10-100 rule: It’s always less costly to operate at the “1” level, which is to predict and prevent failures, than it is to correct a failure that’s already happened—the “100” level.)
That’s not to say reactive maintenance has no place in building management. If it’s carried out correctly—say, for non-essential, rarely used, old, or low-cost equipment—it can be a smart strategy to save on both manpower and resources. But reactive maintenance as a rule is an expensive way to operate, discourages the long-term health of your equipment, and also risks spreading your maintenance team thinner than necessary.
One study found that preventive maintenance has an ROI of 545 percent—in large part due to increasing the useful life of equipment as well as a smaller degree of energy savings.
A Preventive Maintenance Example
Any consistent, regularly scheduled maintenance performed on active pieces of equipment could be considered preventive maintenance. Assets that are the best fit for preventive maintenance are those that are critical to your business operations and for which the repair and replacement costs are high.
Your HVAC system, for example, is a good candidate for preventive maintenance. Routine inspections like the ones below can help prevent some common failures, promote good-quality air circulation, and keep it running at peak efficiency:
-
Clean the evaporator and condenser coils regularly to remove dust, debris, mold, or other material.
-
Clean rooftop or other exterior condenser units and regularly remove snow, ice, and other debris surrounding them.
-
Replace the air filters regularly.
-
Calibrate the thermostats.
-
Inspect compressed air lines regularly for leaks.
-
Conduct maintenance audits regarding the performance of your HVAC equipment.
Beyond Preventive Maintenance: Predictive Maintenance
If you’re already practicing preventive maintenance and are looking for ways to make your efforts even more efficient, it’s time to take a look at predictive maintenance.
Predictive maintenance—pinpointing when a piece of equipment is likely to fail and addressing it before it happens—is made possible thanks to the Internet of Things (IoT), which allows for the collection of real-time performance data. With the help of machine learning and algorithms, this data can then be mined and patterns identified. Eventually, that data can be used to provide valuable insights about aberrant performance that could indicate the likelihood of an imminent breakdown.
One industry survey states that predictive maintenance is proving to be a “powerful new technology that is realising tremendous results and value for companies.” Ninety-five percent of respondents said it is responsible for improving one or more several key maintenance value drivers.
Predictive maintenance is a step up from preventive maintenance because it standardizes and automates the process. A trained technician may be able to determine future equipment failure just by listening to a motor and feeling the vibrations. But someone new to the job or building may not be able to discern the same thing; only over time do they gain that kind of insight.
Data-based predictive analytics ensures that even a novice can see when something’s gone awry. Performance metrics over time can provide an understanding of the performance anomalies that lead to equipment failures. We can then leverage machine learning to build a predictive maintenance model that gives early warning alerts when failures are likely—giving you enough time to address the problem before it starts. For example, let’s say that thanks to continual data collection you know the normal vibration level of a compressor in good working condition. You then have the information you need to set a threshold for anomalies outside a normal variance. Any future vibration level detected outside that range may not be cataclysmic, necessarily, but it should be flagged and passed to a technician for inspection.
Predictive maintenance starts with sensors that monitor and collect the necessary data. A wide variety of sensors are available to collect a broad range of operational data on everything from vibrations, sights, and sounds to temperatures and power consumption. Paired with your critical assets, sensors can give you an unprecedented level of insight into your daily operations that supports your equipment—and your building—better than preventive maintenance.
Ready to take a step past preventive maintenance?
Now that you have a good understanding of what preventive maintenance is compared to predictive maintenance, are you interested in finding out more about how you can take advantage of the power of predictive technology for your building? If so, get in touch with Iota.
Iota’s line of IoT sensors enables you to remotely monitor your equipment, providing precise measurements about any aspect of operations you’re most interested in. They also offer a subscription-based service of predictive analytics and machine learning algorithms that’s designed to help you optimize equipment performance through fault and anomaly detection. Learn how they can help you get the information you need from all your important assets—contact Iota today.
The content & opinions in this article are the author’s and do not necessarily represent the views of ManufacturingTomorrow
Comments (0)
This post does not have any comments. Be the first to leave a comment below.
Featured Product
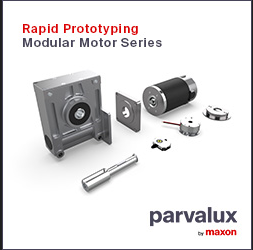