Sean Riley, Global Industry Director for Manufacturing & Transportation, Software AG: Industry-wide, use cases have been proven, IIoT platforms have shown their effectiveness and potential, and roadmaps to success have been developed.
Why IIoT is a Priority for Manufacturers
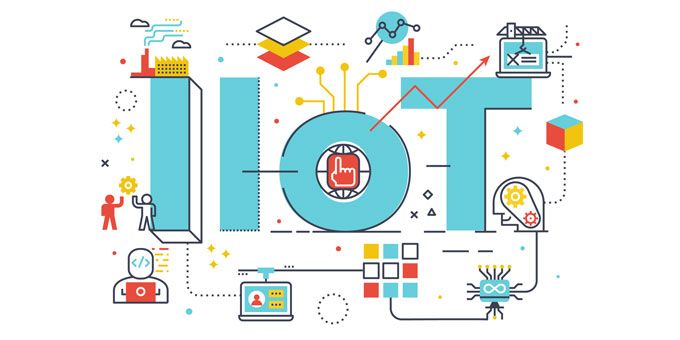
Sean Riley, Global Industry Director for Manufacturing & Transportation | Software AG
The Internet of Things — especially in an industrial capacity — is reaching a major tipping point in terms of accessibility, capabilities and usefulness.
Industry-wide, use cases have been proven, IIoT platforms have shown their effectiveness and potential, and roadmaps to success have been developed as opposed to the mere visions imagined just a few years ago. Overall, this means that manufacturers who have not previously invested in IIoT will be empowered to quickly catch early entrants and fast followers in IIoT, while still finding comparable value.
For manufacturers who have not harnessed the power of IIoT yet, the environment won’t be better than it is now.
Why IIoT Deployment Is So Vital
Every year, manufacturers are faced with the unrelenting need to decrease operating costs through operational improvements. While many of the same operational cost-reduction strategies may continue to work, IIoT initiatives present new ways to obtain more efficiencies.
For example, having real-time insights into operations allows manufacturers to more quickly respond to manufacturing chain complications and also allows for the mitigation of time- and cost-consuming shutdowns or other problems. In addition, manufacturers can create new products and iterate on existing lines based on data collected from devices connected to the IIoT.
Those deploying IIoT products or investing in IIoT platforms for the first time may not have the expertise of those already leading the way, but they are not too far behind. Manufacturers who purchase and deploy the latest IIoT products can still maintain parity with their early-adopter competitors by moving quickly.
But the window is closing. Manufacturers who do not invest in IIoT will increasingly find it to be an uphill climb to catch up to those who have embraced the new technologies because of having to navigate a maturity curve.
Investments have been made and projects have been created and implemented in a wide array of industrial and manufacturing capacities. Those who have already implemented IIoT into their business and those who do so over the next year will have a distinct advantage due to the institutional knowledge flowing through the organizations. As that knowledge gap grows, it will be even more difficult for other manufacturers to catch up with the leaders, early-adopters, and those who are just starting to embrace IIoT.
How To Invest In IIoT
Those who are taking their first foray into IIoT need to have a good strategy when putting money into new products and platforms. The initial investments should be made with IIoT device connectivity and basic real-time analytics. This allows manufacturers to not only deploy new technologies but to have a complete understanding of what is needed to continually bring devices onto the platform and then track what is happening with them once they are on the platform.
The first investment in IIoT in connectivity and analytics is key not only for getting a platform deployed but also for closing the knowledge gap. Time and time again, manufacturers have invested in platforms without also emphasizing connectivity and analytics. Unfortunately, those businesses have had to spend one to two years creating simple analytics and trying to find ways to securely connect devices. This is why there are still opportunities for those deploying IIoT for the first time catch up. Selecting the correct, all-encompassing platform for their requirements can close the knowledge gap and the technology gap.
Manufacturers Must Implement Smart Strategies With Their Smart Technologies
Manufacturers need to be intelligent not only how they invest in IIoT, but also how they deploy the solutions they want to use to optimize their business. Many companies who deploy new technologies, products, or software do so in a fragmented, unplanned manner and have to fix costly errors down the line. The best advice for manufacturers who decide to deploy IIoT is to start small while thinking big. In other words, understand your starting point but always have an end target to serve as a beacon.
Initial projects should be co-used across teams and operational processes and carefully scoped out in order to deliver the highest impact and value over the shortest amount of time possible. It is also important that manufacturers deploying IIoT for the first time are aware that they should be ready to take action immediately if it is not working with their business as anticipated. If tangible value takes more than three months to obtain then either the project is too large in scope or the IIoT platform has a significant deficiency. Adjust accordingly.
For example, if an industrial equipment manufacturer wants to offer product contracts based on outcomes rather than the just selling the product, this will require a significant amount of capabilities including predictive analytics, machine learning, and automating a sizeable number of processes. Rather than focus on this implementing the IIoT solutions as THE objective, use it as a target with an initial objective of connecting existing equipment and providing condition-based alerts to drive service actions. Creating and launching a minimum viable product for the latter should take between four to six weeks which gives a long lead time to observe whether or not value has been obtained inside the three-month threshold.
In sum, manufacturers should be smart and assess their IIoT deployment. Doing so the right way can have a tremendous impact on the bottom line of the business immediately and distance manufacturers from competitors for years to come.
About Sean Riley
Sean Riley is the Global Industry Director, Manufacturing & Transportation, at Software AG. He has more than a decade of experience in supply chain related fields with a specific focus on logistics operations. In addition to his work experience, he holds a BA in Business Administration from Hanover College and a MBA with Distinction in Managerial Finance from DePaul University and is a certified Six Sigma Greenbelt. After receipt of his MBA, he has served as a guest lecturer for DePaul focusing on new value proposition development within a set growth strategy.
The content & opinions in this article are the author’s and do not necessarily represent the views of ManufacturingTomorrow
Comments (0)
This post does not have any comments. Be the first to leave a comment below.
Featured Product
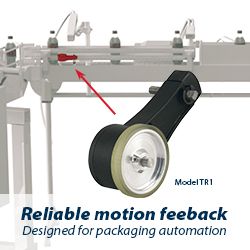