If robotics developers don't understand EMI and take steps to prevent it, the resultant issues could cause robots to behave unexpectedly, such as requiring frequent restarts, showing a limited radio frequency range, moving unintentionally or affecting other nearby robots.
Best Practices for Preventing Electromagnetic Interference in Robotics

Kayla Matthews | Productivity Bytes
Electromagnetic interference (EMI) is also known as radio frequency interference (RFI). It happens when one electromagnetic field interferes with another, resulting in both of them getting distorted.
If robotics developers don't understand EMI and take steps to prevent it, the resultant issues could cause robots to behave unexpectedly, such as requiring frequent restarts, showing a limited radio frequency range, moving unintentionally or affecting other nearby robots.
Here are four things robotics professionals should do to cut down on problems related to EMI.
1. Choose the Right Motor
Some robotics engineers make the mistake of not recognizing that EMI issues exist until after they get deep into the process of building their robots. They fail to realize that motor selection can play a substantial role in mitigating EMI.
For example, an ironless core motor has an internal structure that can reduce EMI. More specifically, these motors have a smaller amount of magnetic energy during commutation, which results in less inductance.
According to Angelica Perzon, a sales engineer at Maxon, a Swedish drive company, ironless core motors do not eliminate all electromagnetic interference. However, they make the issue easier to address at earlier stages.
Also, components that support Ethernet-based control systems, such as dual-port motors, can help enterprises deal with noise issues, especially when they transition from analog-based systems. No single motor is right for every industrial robotics project. Engineers should be mindful of potential EMI issues early on and determine how motor selection could manage them.
2. Use a Shielding Cable
Using more than one robot in a cell or depending on the robot for tasks like welding can both increase the likelihood of EMI issues. However, a shielding cable is a product that helps limit the effects of EMI. These specialized industrial Ethernet cables are wrapped with materials that make EMI less prevalent. HELUKABEL, a company that sells these Ethernet cables, recently announced a new shielding cable in its PROFINET line that's specifically for robotics.
It has a double-shielding design intended for robots subjected to continuous torsion loads. A shield is an isolation barrier to a signal, so it does not stop the source of the noise. Thus, even when utilizing a shielding cable, it's crucial to identify the source of the EMI and determine whether it's resolvable.
3. Engage in Testing Throughout the Robotics Development Process
In addition to the EMC definition provided earlier, robotics engineers should also take electromagnetic compatibility (EMC) into account. It's similar to EMC, but it relates to whether a device can operate as intended in its environment without disrupting the expected performance of surrounding devices.
Therefore, EMC testing is an essential part of ensuring that a robotic in development will work safely and not cause unintended consequences. Emissions testing requires using EMI measurement equipment such as amplifiers and receiving antennas to determine the type and amount of noise a device generates. Additionally, immunity testing assesses how tolerant a device is of external noise.
Cutting down EMI is a priority in robotics, as well as in other industries like aerospace and defense. Chad Hutchinson, Director of Engineering at Crystal Group, Inc., shed light on what can happen when one device generates EMI, and another one is affected by it:
"You’ll have issues with susceptible electronics not being able to operate correctly; it could fail during an operation or do the wrong thing at the wrong time, which could result in personnel injuries, damage to the equipment, or a failure of the mission or whatever the application happens to be."
Test results can determine what's going wrong regarding levels of EMI associated with a robotic component, allowing engineers to pinpoint where and how to make changes. For example, if a particular component is responsible for an excessive amount of noise based on what the testing equipment shows, a robot's development team can know where to start investigating first.
4. Rely on Ferrite Beads
Ferrite beads form a low-pass filter that reduces high-frequency electronic noise existing in a specific band. They're solid or snap-on cores that fit around the cable connected to a device associated with EMI. If robotic developers discover several noisy components, they can use ferrite beads to isolate as many of them as necessary.
However, the correct placement of a ferrite bead is necessary to address the identified issues. For example, a ferrite bead put on the robot cable near the robot will stop noise conducted to the robot cable from affecting the robot's operation.
5. Stay Consistently Aware of EMI
These four best practices will help robot engineers and other members of the development team avoid preventable issues with EMI. These professionals should also strive to reduce EMI issues throughout the development process rather than addressing them at a late stage.
If you like this article you may like "Predictive Analytics vs Machine Learning"
The content & opinions in this article are the author’s and do not necessarily represent the views of ManufacturingTomorrow
Comments (0)
This post does not have any comments. Be the first to leave a comment below.
Featured Product
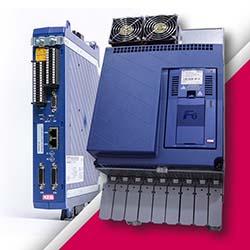