Before the final printing of the building walls, we conducted several tests on the printing of different constructions to be sure in the performance of all units and compliance with the requirements of maximum height and radius of printing.
The Largest in the World 3D-printed Building Was Made in Dubai
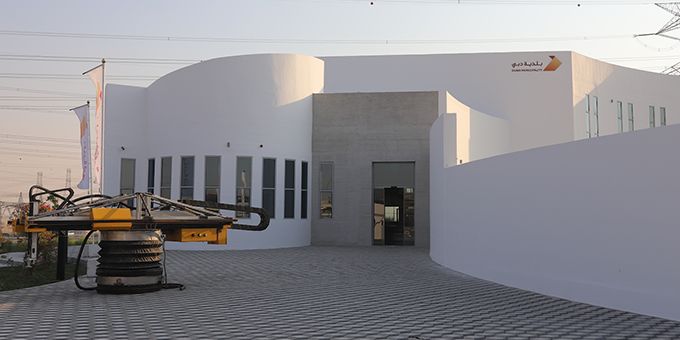
Nikita Zherebtsov, Lead Mechanical Engineer | Apis Cor Company
Mankind has always inspired to progress because of their inquisitive mind. But the second part of human consciousness (skeptical) was sure that good method is a proven method. If we consider in perspective the creation of any landmark invention such as railway, car or aviation it all began by group of people-enthusiasts, looking at whom, many people twirled a finger and said: “This is impossible!”.
The first cars and planes really looked more like homemade crafts glued together than product of industrial industry. However, the laws of the market are immutable at all time: if there is a consumer demand supply will arise sooner or later. After a generation, railways, cars and aviation which it is impossible to imagine the modern world without.
A similar situation is observed in one of the most conservative industries – construction. Even yesterday the technology of 3D-printing in constructions was considered as a funny curiosity which does not have much practical sense, a kind of game of the mind and imagination of engineers. But 3D-printing responded to the tough demand of the market “build faster and cheaper” as well as possible. 3D-printing really works, and we can proud of new printed build, which was fully made by this technology. The company Apis Cor printed an office building in Dubai (UAE), hitting the "Guinness Book of records".
First printing project in Stupino
In 2014 Apis Cor become development of a new project – a mobile construction 3D-printer. The prototype we created was worked on a circular design: the machine printed layers of material around itself. We decided to move away from the idea of portal design because of the difficulties of its transportation and the limited size of the printed building. Such printers are usually installed in factories and there are printed individual elements of the building which will be deliver on a construction site for assembly. Our solution compares beneficially with the developments of other companies. To consolidate the result and gain experience we decided to print the first sample in Stupino (Moscow region) in 2017. We built the first building with an area of 38 sq. m. using 3D-printing.
Nowadays United Arab Emirates, which has significant funds due to oil production, pays great attention to the development of own economy, implementation of new technologies. According to the Dubai municipality plan, at least a quarter of all new buildings should be built using additive technologies by 2025. Based on this, the proposal received from him looked very promising.
Features of the new projects
On the instruction of the municipality, we had to build two-floor administrative building with a height of each floor – 4.7 meters. The total area of the building – 640 square meters. When we got acquainted with the design project, we understood that the customer did not consider about the peculiarity construction’s 3D-printing, and that the power of our equipment is not enough. The current prototype was designed for maximum wall height of 3 meters.
We solved this problem by increasing the height of the boom, which gave rise to a new problem – because of increased height the stiffness of the entire structure decreased. The change of printing trajectory was about 5 centimeters. While we were solving this problem the time to send the equipment to Dubai become. Engineers had got only 2 months for search and manufacture the solution, of which a month was taken by the delivery of equipment to UAE and month to print formwork for foundation. So, the problem with stiffness had to be solved in parallel.
I suggested creating an additional construction, which will increase stiffness of printer system. The printer lift system is based on 3 hydraulic cylinders that lift synchronously. We have created an additional unique mechanism which was flexible when lifting and when stop it makes stiffness construction like truss. Its installation had to be carried out directly on the construction site, because there was no tome for searching a workshop at which all this works can be done. Having arrived with all details and equipment in Dubai, I went with my colleagues to construction site to finalize the equipment. As if we did not prepare ourselves in advance for the peculiarities of the local climate, it was very difficult at first time to experience the heat. We were literally in the desert (construction site is behind the city in new area under construction), it is June, the temperature reaches 50 degrees Celsius. It is physically impossible to stay under the sun more than 20 minutes. So, the most parts of works we did at night illuminating the site with a spotlight. After installation of an additional truss for stiffness, we solved most of problems associated with the error in the trajectory and insufficient stiffness.
The subject of my special pride was the high accuracy of printing. We not only confirmed the results that were achieved in Stupino, but also took a new bar: at a height of three meters the change of vertical at the highest point become 5 millimeters or 0,095 degrees.
Arriving in the UAE, we realized that we need to develop new material for printing, because we can not use the same mixture, which we used to print house in the Stupino. The mixture technologist has developed a new mixture based on gypsum from local building material and taking into account the specific climate of UAE. While we were engaged in the revision of mechanical part, and technologist was developed and tested new formulations of the mixture for printing, a focus group of engineer-builder, architects, project managers adapted the project documentation to the peculiarities of the construction method and the dimensions of the equipment. They also faced a big task: it is necessary to synchronize and optimize trajectory of printing when moving the printer on the construction site. Because the floor area of building is more than 300 square meters, it was necessary to make several rearrangement of equipment and synchronize the code so that rearrangements will not affect the quality of construction.
In addition, it was necessary to adjust the trajectory of printing taking into account the laying of vertical reinforcement of walls, laying of communications, installation of ceilings and jumpers for windows, doorways and columns. Bypassing the vertical reinforcement occurred due to improvements in the printing code.
During the printing of the building in Dubai, the most of the work on the bypass armatures was carried out manually. Based on our experience and data, in the future we are going to develop a machine vision system to automatically detect obstacles and bypassing them. All work for trajectory optimization formed the basis of the new software for making G-code.
Before the final printing of the building walls, we conducted several tests on the printing of different constructions to be sure in the performance of all units and compliance with the requirements of maximum height and radius of printing. We had to be sure at all: in mechanics, hydraulics, feed system, mix quality, correct code and etc. After that finally we started to print the walls of the first floor.
At the beginning of printing the main building we always checked the condition of the equipment. Based on this data we have finalized the technical documentation for maintenance and working with printer. It was not serious problems with a mechanics, but it was always necessary to make allowance for the fact that when were creating the equipment in Moscow we knew very little about the climate of the Emirates.
The main problem of the climate in Dubai – it is constant transition of the temperature through the dew point. Simply put, in one night every metal surface was covered with a coating of rust. The solution was obvious – to choose a lubricant that would prevent corrosion. With all the evidence of this decision, we had a lot of trouble. In the desert a strong wind carries huge amounts of sand, so it sticks immediately on the freshly applied lubricant, which is very harmful as guides and bearings. After trying dozens of options, we found a suitable lubricant and began to apply it. It was a lubricant for a motorcycle chain in the form of spray, having excellent protective properties, high viscosity, besides the sand did not stick to it. Subsequently, taking into account the experience in Dubai, when designing new models of the printer, we began to use stainless steel guides – this is quite an expensive solution, but significantly increases the service life of the node.
The main works of printing of the building was made by team of four people: project manager, software developer, architect and engineer. We joked that we were taking part in racing “Paris-Dakar”. The comparison was perfect – absolutely terrible weather and climatic conditions and incredible load.
The printing of final building fell within 500 hours of machine time – 8 hours per day. Previously, we could not afford such a luxury - to print as much time as convenient. At the very first printing tests back in Moscow, we tried not to stop the printer, as after each stop it was necessary to do a lot of works: washing of all hoses, printer routing, kneading system and feeding the mixture. When printing in Dubai - we already had sufficient experience and many of the procedures were automated. Sometimes it was necessary to make breaks in the printing for several days or weeks because the General contractor need to laid fittings, isolation, communications and ceilings. Installation of ceilings was carried out in the traditional way - laying of a slab by means of the crane. After printing the 1st floor, the ceilings were installed, then the printer was installed on the ceiling and started printing the 2nd floor.
The building printed in Dubai, unlike the house in Stupino, will be put into usage and there will be the offices of local companies. This building is the first printed building in the new region of Dubai and the municipality plans to "print" the whole region.
During the project we were facing with technical problems, organizational difficulties, and sometimes waves of skepticism and misunderstanding. But anyway, the printing of the building was successfully completed in august 2019, after which the General contractor moved to the execution of finishing works, and the presentation of the finished building took place in October 2019. The building was included in the Guinness book of records as the largest 3D-printed building in the world. Other large 3D-printed editions already exist, but they were all assembled from prepared blocks, whereas we printed the building "whole" on the construction site.
Further development of technology
During the project we discovered for ourselves the subtleties not only of the technical features of the construction 3D-printing processes, but also determined the vector of development, so that all our achievements formed the basis of a new era of the construction industry. But like any innovation, construction 3D-printing must pass the test of time. This is a challenge to an entire industry that has its own market and infrastructure, and disputes with conservative institutions about efficiency can drag on. However, I believe that the technology has great potential for development and in 10 years printing houses will become as commonplace for everyone as building houses out of bricks or blocks.
I am sure that in the future we will be able to achieve automation of construction without human intervention, not only when printing the foundation and walls, but also be able to print ceilings and roof and automatically install engineer communications, doors and windows. All this can already be done today by usage only ready-made solutions. But it takes time and resources. Also soon we will not be limited to printing houses in 2-3 floors. The compositions of the mixture for printing already allow you to move to multi-floor construction. The main limitation is the lack of a legislative framework for printed houses. Today, many companies are engaged in construction printing and I am sure that soon it is going to be revolutionary changes in the construction industry.
If you like this article you may like "Quick Guide to Metal Additive Manufacturing for Industrial Components"
The content & opinions in this article are the author’s and do not necessarily represent the views of ManufacturingTomorrow
Comments (0)
This post does not have any comments. Be the first to leave a comment below.
Featured Product
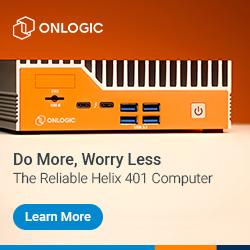