Remote monitoring for managing and reducing water usage is an especially consequential and cost-saving technology. Here’s why manufacturers should begin putting it to work today.
Remote Monitoring for Reducing Manufacturing Water Usage
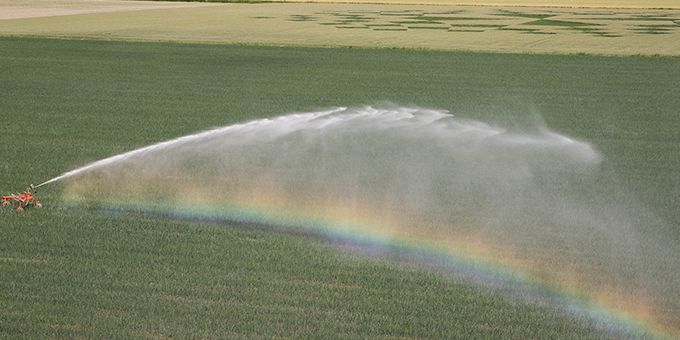
Emily Folk | Conservation Folks
There can be no Fourth Industrial Revolution without the Industrial Internet of Things. The IIoT is a powerhouse of automation, improved functionality and greater efficiency for every type of industrial activity, including manufacturing.
Remote monitoring for managing and reducing water usage is an especially consequential and cost-saving technology. Here’s why manufacturers should begin putting it to work today.
Saving Water and Money Using Remote Water Monitoring
You’re likely familiar with the Industrial Internet of Things by now. It allows the networking of industrial control systems, sensors and other remote assets.
By communicating with each other and with operators, these industrial networks function like a central nervous system. They gather and transmit data, allowing this information to work in enterprise planning, asset management and collaboration with outside parties.
Remote water monitoring takes the fundamentals of the IIoT and puts them to work in the management of water and wastewater. Below are just some of the ways this advancement is advantageous in a manufacturing setting.
1. Early Detection of Problems Causing Water Loss
Remote networked sensors help operators monitor the pressure in water mains, transportation pipes and holding or mixing tanks.
The first advantage is that this system helps spot leaks that lead to wasted water and unnecessarily high expenses. The second advantage is the ability to fine-tune the pressure in the system in real-time so that operations use only the minimum pressurization at any given time.
Both advantages lead to water and cost savings that can be substantial over time. Manufacturers that let leaks go undetected or unaddressed typically turn up the water pressure to compensate, leading them to spend far more on their supplies than they would have otherwise.
2. More Affordable and Timely Maintenance
Achieving repeatable and timely maintenance cycles is another factor that helps manufacturers reduce the amount of water they use and waste — as well as keep costs down across the facility.
Historically, manufacturers used the run-to-failure model for their water and wastewater transportation and treatment equipment. With the IoT providing equipment analytics in real-time, operators can switch to a predictive maintenance model instead. This system prevents equipment from operating inefficiently for extended periods, eliminates downtime and optimizes the useful lifetime of critical assets.
Abundant case studies explore the advantages of advanced monitoring and communication technology. Entire towns can use industrial radios at the edge of their networks, powered by message queueing telemetry transport (MQTT), to send and receive data more efficiently between remote water treatment stations.
The concept applies to companies with multiple manufacturing plants just as easily. Edge computing provides the necessary tools for an enterprise to monitor large water infrastructure systems with ease and minimal personnel.
3. Provide Monitoring for Water Additives
Another way manufacturers can ensure they’re getting the most out of their water supplies and budget is through remote additive monitoring and administration. Holding tanks typically need specific amounts of chlorine to keep the water stable and in usable condition, or else the manufacturing process may be compromised and cause material losses and product defects.
The administration of precise amounts of acids to storage tanks is another application of remote water additive monitoring. Acids help neutralize alkalinity and prevent scale from forming. In doing so, it increases equipment longevity and allows stored water to pass through the system and be used in the manufacturing process as many times as possible before needing replacement.
Manufacturers Need Remote Water Monitoring
Whether used for mixing, diluting, washing, cooling, fabricating or another process, water is often the lifeblood of industrial manufacturing.
For the sake of the bottom line and the health of the planet, it’s essential to optimize our use of this precious resource and let nothing go to waste. The use of industrial water is declining in the U.S. and has been since 1950 — an achievement made possible by more efficient equipment and better monitoring technologies.
From more cost-effective maintenance to stopping leaks before they start, remote water monitoring with the IIoT is a worthy investment and a technology that’s here for the long haul.
The content & opinions in this article are the author’s and do not necessarily represent the views of ManufacturingTomorrow
Comments (0)
This post does not have any comments. Be the first to leave a comment below.
Featured Product
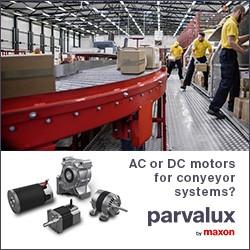