The company’s collaboration with Additive Flow for a particularly challenging project involving a metal and polymer over moulded component, ensured yet another successful outcome for Comeragh that will open up further opportunities in the future.
Multi Property Optimization for Injection Moulding to Maintain Safety and Reduce Manufacturing Costs
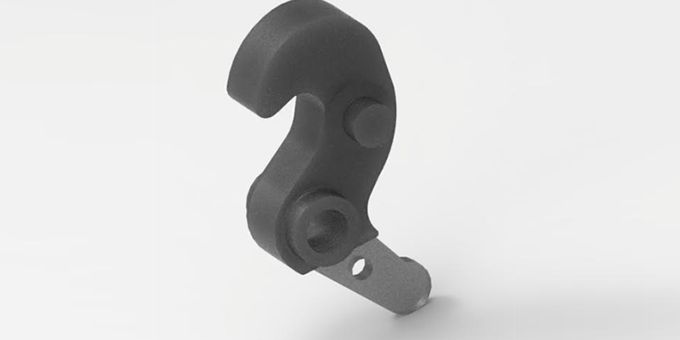
Case Study from | ADDITIVE FLOW
Comeragh Composites is a specialist technical consultancy based in Belfast, Northern Ireland, with dedicated expertise in delivering advanced solutions for polymer and composite manufacturing projects. The company’s collaboration with Additive Flow for a particularly challenging project involving a metal and polymer over moulded component, ensured yet another successful outcome for Comeragh that will open up further opportunities in the future.
Project Overview
The component in question is for a child car seat: specifically it is a hook for retaining the seat within a car. Four of these critically functional components are deployed within a single base unit that is locked into the car and catches the actual seat that the child sits in. Each component was manufactured from connecting two parts, the inner part made from steel and over moulded in a polymer material. Typical production volumes for this individual component are 40,000 per year for the OEM, with the potential to roll it out for other models.
The engineering brief for Comeragh was challenging to say the least: to manufacture this multi material, multi assembly hook more cost effectively without compromising performance or safety. Competition from low cost manufacturing economies is constantly driving this re-engineering approach — with the alternative being to consider relocating manufacturing — to maintain profit margins. Moreover, reducing costs AND maintaining or improving safety requirements are generally considered to be incompatible. But this does not always have to be the case. By engaging with Additive Flow, Comeragh was able to find a solution that not only met the brief but added significant value in other ways as well.
As Additive Flow undertook this project the ABSOLUTE priority was safety performance (equal to or above requirements), while cost reduction was targeted as a required outcome. However, once the human thinking was removed, Additive Flow’s FormFlow software was able to exploit the workflows within such a highly constrained environment, and in this case, was able to deliver a single polymer composite material, injection moulded part that could be manufactured at a reduced cost while adhering to all safety requirements.
Challenge
The original iteration of the component involved manufacturing a metal steel inner part that was then fully over moulded with a polymer material to meet the critical safety requirements. The manufacturing processes involved were proving both highly complex and costly, as well as time consuming.
Solution with Additive Flow
Additive Flow was able to deploy the advanced multi property optimisation capabilities of its FormFlow software to consider the use of a single composite polymer material and eliminate the metal part. To this end, Additive Flow first conducted a structural simulation on the original model, which quickly identified that a direct conversion to a single polymer material was not possible. However, by considering the well understood properties of the polymer PA66 with 30% glass fibre, FormFlow was able to analyse various different orientations of the component and produce results demonstrating the impact of fibre alignment. Results show a 30% difference in stress and a 58.4% difference in displacement – highlighting the need to understand orthotropic behaviour and deal with it.
Additive Flow’s leading multi-property optimiser then allocated different orientations of the fibre within the part, to be delivered by different inlets within the injection molding process. This is especially powerful for this product, as the two forces acting upon the component are perpendicular. Additive Flow’s software Formflow optimised the properties simultaneously with geometry, to align with these different mechanical load cases while optimising weight within the safety factor.
From this, Additive Flow was subsequently able to run a series of optimisations for a single material (multi-property) component that operated within the material stress constraints as the original dual material component, with a weight reduction of 60%. Furthermore, by allocating the different orientations of the fibres, the results then informed Comeragh engineers as to how to best position the inlet for the injection moulding process to ensure optimal production of the component.
Results & Benefits
Production of the new single material component optimized by FormFlow resulted in significantly reduced costs - which were cut in half. The cost-per-part of the original dual-material component was €2–2.50 compared with the cost-per-part of the new single-material component at €1–1.50. This translates to an annual cost reduction of 50% or €40,000 (10,000 units / 4 components per unit). In addition, the injection molding process greatly simplified the end-to-end manufacturing process, while also contributing to the simplification of the supply chain and increasing the recyclability of the component, making it more sustainable at end-of-life.
Findhan Strain, Director at Comeragh Composites, commenting on the outcome of the collaboration with Additive Flow, said: “There is an obvious cost benefit to running an optimisation of this nature. However, another significant benefit for us is the supply chain simplification: now we no longer need to buy in metallic components, deal with suppliers and potential quality issues, or manage the movement of the metal material across the factory floor with a machine operator preparing it for overmolding. Now, with the PA66 single material injection moulded component it is much easier to control the process.
He continued: “A further benefit is the enhanced suitability of the part within a circular economy approach. Although PA66 with 30% GF is not yet easy to recycle, it is easier than steel over moulded with another polymer such as POM. This is particularly relevant when considering an over moulded part that has a low residual value but would require notable effort to recycle. Undertaking these types of design activities are relevant now and will only increase in importance in coming years.”
“I would also add that while some of these benefits are a bit more difficult to quantify financially, they add really significant value for us, for volume manufacturing applications.”
Alexander Pluke, CEO of Additive Flow, further commented on the project: “I think what this project shows is that the optimization algorithms that we have developed at Additive Flow do not just apply to additive technologies but translate easily and very effectively to advanced injection moulding processes. It is really important to consider materials that we’ve known about for a long time and have a good understanding of — and to question why we are not deploying them in a way that is actually possible to improve manufacturing outcomes — regardless of process — in terms of the parts themselves, manufacturability, sustainability and recyclability. I also specifically believe that the multi-property capabilities of FormFlow offer interesting opportunities to really harness the orthotropic strengths of materials in the right way – as we have demonstrated here. Cutting costs and increasing sustainability seems like a real win-win.”
ABOUT ADDITIVE FLOW
Founded in 2017, Additive Flow, London, U.K. is leading the way in the creation of digital solutions with the overall aim of accelerating innovation through the use of AM. The company exists to solve digital workflow issues that currently prevent users — and potential users — of AM from unlocking the potential of manufacturing technologies during the pre-production stages of the process chain. The company was co-founded by Alexander Pluke (CEO) and Charles Fried (CTO), who are leading a growing team that work at the intersection of architectural computation, Artificial Intelligence (AI), machine learning, and material science.
The content & opinions in this article are the author’s and do not necessarily represent the views of ManufacturingTomorrow
Comments (0)
This post does not have any comments. Be the first to leave a comment below.
Featured Product
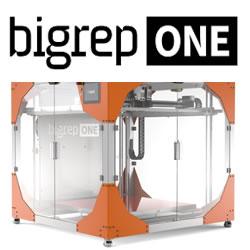