By continually monitoring the condition of your equipment’s most critical mechanical and electrical components, failures can be avoided with predictive maintenance carried out during scheduled downtimes, resulting in continual operations.
Understanding the Key Elements for Machine Condition Monitoring
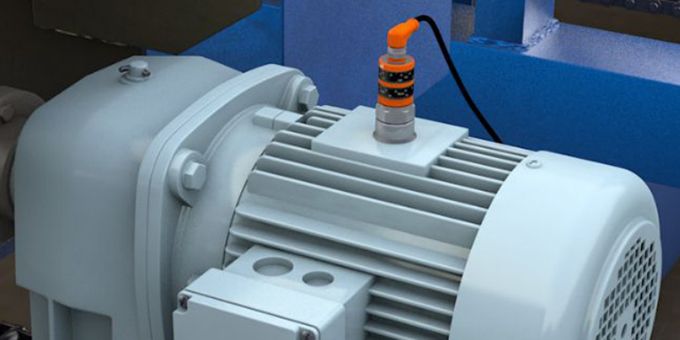
Article from | Automation24 Inc.
Machine condition monitoring is a critical part of every industry to help production run smoothly and efficiently. If one component fails, you can experience downtime costing you valuable time and money. By continually monitoring the condition of your equipment’s most critical mechanical and electrical components, failures can be avoided with predictive maintenance carried out during scheduled downtimes, resulting in continual operations. This FAQ will explore some key elements you will want to consider.
1. What is the basic idea behind condition monitoring?
Equipment gets old and wears out. Condition monitoring systems collect operational data from critical mechanical components—while in operation—flagging potential problems early on and communicating that information in a useable manner. A condition monitoring system allows maintenance managers/supervisors to schedule repairs within regular maintenance cycles, eliminating costly shutdowns, decreasing parts inventories, and improving overall productivity.
2. What would be the first steps in determining the extent to which I need a condition monitoring system?
You’ll first want to conduct a survey of your equipment and what you wish to achieve, such as an increase in machine uptime, catastrophic failure prevention, workers’ protection, and/or enhanced quality. Next, review your equipment’s repair histories and maintenance costs to focus on those areas that could be greatly improved through condition monitoring solutions. A machine’s failure history will signify if it requires closer monitoring (see Q5 concerning costs).
3. What are the most telling signs that a machine is about to fail?
There are several key indicators, vibration often being the number one change that will occur prior to machine breakdown. Whether a failing pneumatic or hydraulic cylinder or system, an electric motor bearing, or mechanical motion device such as a lead screw, vibration will occur prior to failure. Depending on machine load and duty cycle, early detection often avoids expensive downtime. By installing vibration sensors at key locations, minor changes can then be transmitted to a humanmachine-interface (HMI) and/or control system for analysis. Vibration sensors are available for a wide number of applications. Devices typically operate at 24 VDC and provide switching or analog signals depending on your needs. Applications where vibration sensors are most often used include those where bearing failure is a primary consideration, including HVAC compressor imbalances, electric motor deterioration, drives spindles, and any fan used inside a machine or factory. In pneumatic and hydraulic systems such as heavy metalworking machines like presses or injection molding machines, increased vibration is a common early warning sign of failure. A second identifier of early failure is temperature. This is especially the case in equipment that doesn’t start and stop regularly, but instead runs 24/7 at a constant temperature rate. Even minor shifts in temperature can be monitored, leading to a better understanding of equipment health. This will allow action to be taken before a breakdown. Temperature sensors and transmitters are designed to operate over a wide variety of ranges depending on your needs. Typical ranges can be from -40 through 572 degrees F, with special sensors programmable from as far as 148 through 1,112 degrees F. Example applications include machines used in continuous processes, such as chemical processing, paper manufacturing or anywhere else a service interruption could ruin an entire production run. Other applications with high failure consequences include power plant boilers, turbine generators, and equipment located in hazardous environments, which can recognize some of the highest losses.
4. What equipment is needed once I have the sensors in place?
There are two primary approaches, which include the HMI/ operating panel approach and the central control room approach—often used together.
First, HMIs provide a visual representation of current conditions, process outputs, and overall machine health for critical manufacturing or process control equipment. HMIs are available with water and dust ingress protection, with enclosures suited for a variety of environments, and coated versions for a wide variety of applications. HMIs can be programmed to prioritize machine measurements for temperature and vibration based on how quickly a change leads to a failure. For lower priority conditions where changes signify a future failure—and where scheduled maintenance can occur—a simple alarm signal might be appropriate. For situations where a change might require more immediate attention a larger graphic or brighter color might be used. To meet both needs, many HMIs are available with simple screens or complex, multi-color capabilities.
Another approach is for operations to use a central control room to monitor their critical equipment. This is often necessary in harsh environments such as nuclear plants and chemical processing facilities. Condition monitoring can, again, be prioritized to meet your particular needs. A combination of the two approaches is often used when a company is integral with their IIoT (Industrial Internet of Things) infrastructure. For such operations, condition monitoring might go well beyond the monitoring of mechanical components of single machine or series of machines to include an entire plant.
5. What costs am I looking at here?
To come up with a bottom-line cost, consider a prior year’s downtime costs. Include lost production, repair or replacement costs, and labor costs. Compare these downtime costs with the purchase price of the condition monitoring components you need—based on those mentioned above—along with installation and training costs.
The purpose of a condition monitoring system is to be able to schedule repairs during regular maintenance cycles, eliminating emergency downtime completely since operators and maintenance managers/supervisors will have access to machine health and can make maintenance decisions proactively.
6. What else might I gain from using a condition monitoring system?
Another benefit is how condition monitoring helps a company meet federal and industry standards such as those set by ANSI, ASME, API, and INPO. This may include requirements for condition monitoring that are imposed through the Department of Energy for certain industries. Condition monitoring may also help with certifications for safety and quality requirements per OSHA.
Automation24 is the premier online supplier for industrial automation components offering a well-rounded selection of products and solutions from sensor to control cabinet. We have been developing a comprehensive range of items from brand name manufacturers and offer them to our valued customers at the best prices. All items are stocked in our US warehouse and ship same day. Our technical support team is also available for support with your application before, during and after your order.
The content & opinions in this article are the author’s and do not necessarily represent the views of ManufacturingTomorrow
Comments (0)
This post does not have any comments. Be the first to leave a comment below.
Featured Product
