Solutions for avoiding thermally induced dimensional deviations of workpieces have become more crucial than ever for the machine tool building industry. Thermal drift is primarily caused by feed axes on the basis of recirculating ball screws.
How Machine Tool Feedback Can Reveal or Hide Axis Errors
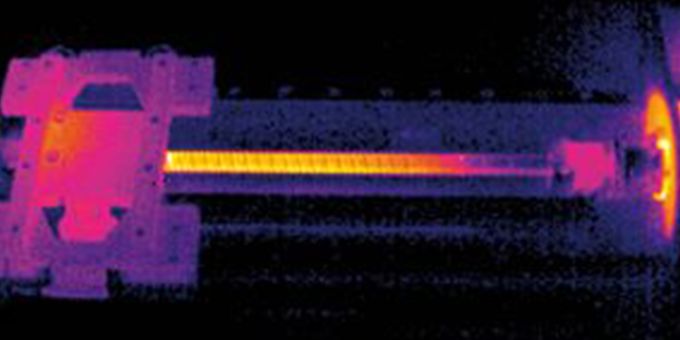
Article from | Heidenhain
Solutions for avoiding thermally induced dimensional deviations of workpieces have become more crucial than ever for the machine tool building industry. Thermal drift is primarily caused by feed axes on the basis of recirculating ball screws. The temperature distribution along ball screws can change very rapidly by feed rates and moving forces.
Machine tool builders and users have options for combating thermal and other discrepancies. Active cooling, symmetrically designed machine structures and temperature measurement are common practice today. But there’s another discussion too, one of feedback. The types of encoders and their feedback loop with the control can actually either mask or reveal distortion, which can be the difference between an on-spec part and extra finishing.
Position acquisition on linear axes
The position of a feed axis can be measured either through the recirculating ball screw in combination with a rotary encoder, or through a linear encoder. If the axis position is determined from the pitch of the feed screw and a rotary encoder (see top illustration), then the ball screw must perform two tasks: As the drive system, it must transfer large forces, but as the measuring device it is expected to provide a highly accurate screw pitch. However, the position control loop only includes the rotary encoder. Because changes in the driving mechanics due to wear or temperature cannot be compensated in this way, this is called operating in a semi-closed loop. Positioning errors of the drives become unavoidable and can have a considerable influence on the quality of workpieces.
If a linear encoder is used for measurement of the slide position (bottom illustration), the position control loop includes the complete feed mechanics. This is referred to as closed loop operation. Play and inaccuracies in the transfer elements of the machine have no influence on position measurement. This means that the accuracy of the measurement depends almost solely on the precision and location of the linear encoder.
Closed loop: position measurement of a linear axis by a linear encoder
Semi-closed loop: position measurement of a linear axis by a rotary encoder in the feed motor
Various conditions of application together with growing feed rates and forces lead to constant changes in the ball screw’s thermal condition. Local temperature zones develop on a recirculating ball screw, which change with every change in position and decisively reduce accuracy in the semi-closed loop. High reproducibility and accuracy over the entire traverse range of linear axes can therefore be achieved only through operation in a closed loop. The results are precise workpieces and a drastically reduced rejection rate.
As an alternative to using a recirculating ball screw, linear feed axes can also be driven by linear motors. In this case, the position of the machine axis is also measured directly by a linear encoder mounted on the axis slide. For highly dynamic and at the same time quiet operation, linear motors already depend on high-resolution, accurate linear encoders. For this type of drive, the advantages of closed loop operation apply unrestrictedly.
Position acquisition on rotary axes
The basic principle for linear axes also applies to rotary axes. Here, too, the position can be measured with a rotary encoder on the motor, or with a high-accuracy angle encoder on the machine axis.
If the axis position is measured using a rotary encoder on the feed motor it, too, is referred to as a semi-closed loop, because the transmission error of the gear mechanisms cannot be compensated through a closed position loop.
Position measurement by an angle encoder on the machine axis. Errors of the drive mechanism are compensated.
Semi closed loop: Position measurement by rotary encoder on the feed motor. Errors of the drive mechanism are not recognized.
Error of the mechanical transmission in rotary axes are caused by eccentricity of the gear wheels, play or friction and elastic deformations in the tooth contacts and the bearings of the transmission shafts.
Beyond this, most prestressed transmissions are subject to significant friction that heats the rotary axes and can therefore— depending on the mechanical design—result in positioning error. In a semi-closed loop, the error in the transmission of rotary axes leads to substantial positioning error and to significantly reduced repeatability. The errors of the rotary axes are transferred to the geometry of the workpiece, which can greatly increase the number of rejected parts.
The positioning accuracy and repeatability of rotary axes can be decidedly improved with the use of precise angle encoders. Since the axis positions are no longer measured on the motor, but rather directly on the rotary axes of the machine, this is referred to as Closed Loop operation. Errors of rotary axis transmissions have no influence here on positioning accuracy. The accuracy with which a rotary axis can move to a certain axis position over a long period is also decidedly increased. Economic manufacturing with minimal scrap is the result.
The rotary axes that are driven directly by a torque motor play a special role. The torque motors’ special design permits very high torque without additional mechanical transmission. Rotary axes with torque motors require a high-resolution angle encoder immediately on the machine axis. They are always operated in a Closed Loop.
Conclusion
Machine accuracy must be maintained even under strongly varying load conditions. Consequently, feed axes must achieve the required accuracy over the complete traverse range even with strongly varying speeds and machining forces. Position errors of 200 µm and more may result during a machining operation if the slide position is determined only from the spindle pitch and a rotary encoder on the motor. Essential drive errors are not compensated in the semi-control loop when this method is used. These errors can be eliminated by using linear encoders.
Angle encoders used on rotary axes provide similar benefits, since the mechanical drive components are also subject to thermal expansion. Linear and angle encoders therefore ensure high precision of the components to be manufactured even under strongly varying operating conditions of the machine tools.
The content & opinions in this article are the author’s and do not necessarily represent the views of ManufacturingTomorrow
Comments (0)
This post does not have any comments. Be the first to leave a comment below.
Featured Product
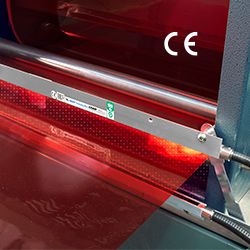