3D printing has evolved significantly over recent years, with much of the research effort placed in the materials science field. This has enabled the development of a whole range of high-performance polymers with mechanical characteristics similar to those of metal.
The Potential of Polymer 3D Printing - Exploring Advanced Manufacturing Processes and Bearing Design
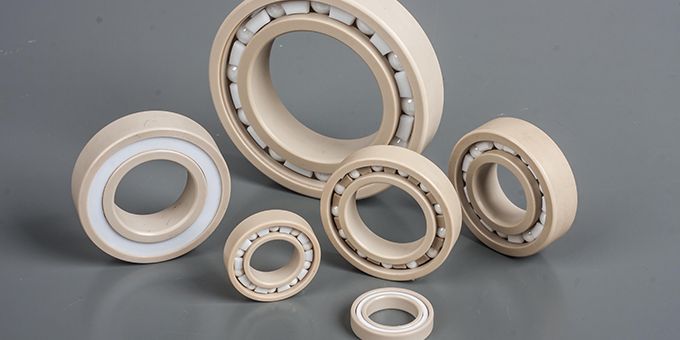
Chris Johnson, Managing Director | SMB Bearings
AM encompasses a range of technologies that create 3D objects by layering materials on top of each other. Specifically, in polymer 3D printing there are five common processes: stereolithography (SLA), fused deposition modelling (FDM), selective laser sintering (SLS), multi jet fusion (MJF) and material jetting.
Each of these processes impacts a material’s microstructure, including size, shape and orientation of the grains or crystals. This presents various challenges and opportunities.
For example, SLA offers a smooth surface finish, but components tend to be less durable than parts produced with other additive technologies. So, let’s explore the bearing design development and production opportunities facilitated by 3D polymer printing processes.
Design flexibility for small or medium batches
3D printing gives bearing manufacturers the design flexibility to produce bearings with bespoke elements and enhanced performance. The 3D printing process is relatively simple and doesn’t require expensive tooling. This allows manufacturers and design engineers to experiment with design features that wouldn’t have been economically viable using conventional bearing manufacturing methods.
Bearing manufacturers can use an increasingly diverse range of materials with 3D printing. For example, 3D printed reinforced polymers can match or be enhanced beyond conventional properties, which opens the door to exciting new design possibilities. Bowman International, an Oxfordshire based bearing manufacturer, used MJF technology to produce a bespoke ‘rollertrain’ retainer using PA11 nylon. The interlocking structure permits room for two-four more rollers, allowing for a 70 per cent increase in load capacity, as well as boasting greater elasticity, durability and functionality.
Another barrier to innovation is minimum order volumes. 3D printing removes this barrier, allowing manufacturers to provide a cost-effective low-volume production service — even for orders as low as ten bearing units. 3D-printed moulds save time and money compared to expensive metal bearing moulds. They also enable a more agile manufacturing approach, meaning that design engineers can test mould designs and easily modify them without incurring unfeasible production costs and high set up fees.
While 3D printed mass-produced bearings aren’t yet commonplace, polymer 3D printing is making an impact in the rapid prototyping world. For example, in a niche concept vehicle, 3D printing may be used to achieve fast and visually appealing prototyping. This would ensure that the smallest of mechanical elements, such as the bearings, functioned in unison with the entire system.
Light weight designs
For low load, low speed applications, plastic bearings offer fantastic performance characteristics and are already five times lighter than their steel counterparts. This reduces the initial weight and energy needed to get them moving. In industries such as aerospace, automotive or medical technology, lightweight design can achieve better safety performance as well as vital cost savings.
Using 3D polymer printing processes, it is possible to design a component that is lighter still — by using honeycomb-like structures. This would be very difficult and time-consuming to achieve with traditional machining processes. Many industries may have historically chosen to rely on metal lightweight innovations, such as Schaeffler’s XZU conical thrust cage needle roller bearing that can be used as an articulated arm bearing in lightweight portable robots. However, 3D printed high-performance thermoplastics such as carbon-fibre and polyether ether ketone (PEEK) offer a feasible alternative to metal.
Opting for a 3D printed retainer in nylon (PA66) or another polymer material, can help to reduce the weight of the whole bearing. Carbon-fibre re-inforced nylon is one of the most popular combinations for nylon printed materials. It offers many of the same benefits as standard nylon including high strength and stiffness, but it produces significantly lighter components. A 3D-printed polymer cage may also reduce the wear on the rolling elements, compared to a conventional steel cage.
A 2018 feasibility study assessed the friction performance of a commercial deep-groove (6004) 3D printed ball bearing. The bearing was fabricated using the MJP process, using plastic material for the structure and fusible wax material for the support. The result demonstrated satisfactory durable life of the 3D-printed ball bearing at low loads and speeds.
Is quality standard?
Friction isn’t the only performance characteristic brought into question in the 3D printing debate. In June 2018, the Additive Manufacturing Standardization Collaborative (AMSC) published an updated version of its a standardisation roadmap for additive manufacturing. Adopting standards to mitigate and control risks as well as allowing more consistent quality are important steps for the future of 3D polymer printing. This is especially important for components that are safety critical, such as bearings.
As with traditionally manufactured components, 3D printed plastic bearings must undergo the same rigorous testing procedures to make sure they are fit for purpose. Crucially, when experimenting with innovative new designs and enhanced material properties, it is essential that the final application environment is carefully considered, reaffirming the importance of bearing specialists in industry.
In the traditional manufacturing versus advanced manufacturing techniques debate, the good news is that you don’t need to pick a side. Polymer 3D printing can be used to supplement traditional bearing manufacturing techniques, offering rapid prototyping and enhanced performance characteristics that have the potential to rival metals. While 3D printed bearings aren’t commonplace just yet, the evidence is showing that they could be in the future.
The content & opinions in this article are the author’s and do not necessarily represent the views of ManufacturingTomorrow
Comments (0)
This post does not have any comments. Be the first to leave a comment below.
Featured Product
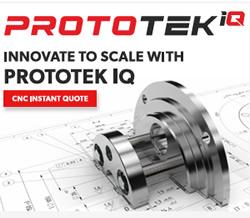