Understanding current trends in CNC machining is the first step to taking advantage of them. Here’s what’s changing and what it means for machine shops.
Take Advantage of Current CNC Machining Trends
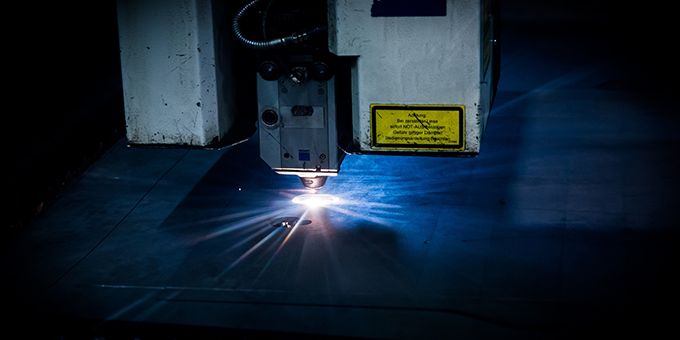
Megan Ray Nichols | Schooled by Science
Custom manufacturing providers, including CNC shops, find themselves under new pressure from a variety of sources. Globalized competition, new technologies and the struggle to retain talent during demographic upheavals are just a few things they face.
Understanding current trends in CNC machining is the first step to taking advantage of them. Here’s what’s changing and what it means for machine shops.
Reducing Risk Using Machines-as-a-Platform
As CNC machines become more capable of executing complicated designs across more axes of movement at once, the risk of collisions and machine damage increases. This is a key reason why machines-as-a-platform are growing in popularity and importance.
Service providers like MasterCam and Provencut use computer-aided manufacturing (CAM) to create digital twins of CNC equipment. Machine shops don’t have to rely on so-called “tribal” knowledge sets anymore. Instead, operators can download machine tool setups, specifications and pathfinding instructions as feed, speed and design “recipes” to execute on CAD designs.
The advantage of these machine platforms is twofold. First, it gives a shop the means to test machine calibration and product designs in a purely digital setting. Second, it reduces the risk of damage and faulty parts due to a poor match between calibration and workpiece design.
Moreover, design intent — including tool choice and finishing instructions — is baked right into the digital models. No 2D drawings are required.
Improving Business Continuity Through E-commerce
The custom manufacturing and machining industries have long been consultative in nature. Companies often faced a lengthy and difficult process of procuring the right inserts, mills, drills, and other materials and components they need for the task at hand.
The benefits of e-commerce in this space shouldn’t be overlooked. Online marketplaces like Xometry Supplies make it simple for job shops and manufacturers to find and purchase manufacturer-direct parts, tools and raw materials with transparent pricing.
AutoCrib and MSC Direct use a different tactic by providing on-premise vending machines for frequently ordered parts and machine components. Over time, these cabinets use inventory tracking to “learn” which products the shop goes through most quickly and automatically reorder them.
Another company, called DigiFabster, uses the e-commerce model plus automated estimating tools to connect machine shops with potential clients. The company claims some customers have seen their labor costs drop by 20% or more thanks to the platform. The idea here is to provide a full-featured customer portal for ordering services while allowing the machine shop itself to retain its independence and unique branding.
Supplementing a Limited Talent Pool With On-Machine Training
The makers of CNC machines and similar equipment recognize the value of intuitive operation. As devices become more complex and deliver more design variables into the operator’s hands, the risks of a limited talent pool in custom manufacturing grow only more pronounced.
A Deloitte study points to a potential $2.5 trillion impact on the U.S. economy by 2028 if steps aren’t taken to address the shortfall of skilled manufacturing employees. Quickly advancing technologies is one factor, and the rapid retirement of older, highly skilled workers is another. How are machine designers answering the call?
Multiple providers, including Haas Automation and Amada, have expanded their portfolios of intuitive machines with the addition of on-machine troubleshooting, tutorials and intelligent feedback tools.
Machine controllers are larger and provide more screen real estate than ever to control machines and receive feedback. These new CNC machines help address workforce development bottlenecks and reduce the likelihood of user error through intuitive visual feedback.
CNC machines with workforce development and troubleshooting software can be more expensive on day one due to licensing costs. However, they can tell the user when they don’t have the right die or tool equipped, or when there’s a conflict between the design and the machine setup, or show other sources of potential risk. The result is fewer defects, more confident control over machine capabilities and faster throughput.
Improving Versatility and Speed Using Modular, Multi-Axis Machines
The digital side of operating a machine shop or manufacturing plant isn’t the only factor experiencing a sea change. The hardware itself is advancing in ways that make it more cost-effective to operate and upgrade, all while unlocking more complex product designs.
Four- and five-axis machines have become competitively priced in the milling as well as laser, waterjet and laser cutting fields. This is a significant change in itself, and it brings responsive servo drives, high-accuracy tables and confident multi-axis control to a greater number of manufacturers. Companies that add more axes to their workflows can tackle more complex geometries and reduce the time required for machine setup.
Although the prices on four- and five-axis machines have fallen into accessible territory, machine designers know that shops may prefer an intermediate step as they build their operations. As a result, modern designs for three-axis machines increasingly favor modularity — including the opportunity to cost-effectively upgrade them with two-movement axes when needed.
Another modern compromise is the so-called “3+2” machine. These execute three-axis programs after repositioning the part across the fourth and fifth axis.
Some estimates say fewer than 5% of manufactured parts take advantage of full five-axis movements. These steps forward are moving five-axis manufacturing out of the “nice to have” category and making it a necessity for exploring innovative new designs in a variety of industries.
Boosting Uptime and Machine Life With the IIoT
Sensors have become considerably cheaper to deploy separately or incorporate into existing equipment in recent years. For manufacturers and machine shops, the benefits of merging hardware and software with the Industrial Internet of Things are clear.
Even small machine shops can use the sensing and data sharing capabilities of the IIoT. These include:
-
Aggregating historical data about machine and part performance, as well as energy demand, to uncover trends and bottlenecks and find the right moment to upgrade or replace machines
-
Using intelligent machine monitoring to find the ideal moment to deliver preventive maintenance between production runs
-
Incorporating smart material handling equipment that finds process bottlenecks and uncovers opportunities to add parallel production lines
-
Adding tool presetters and machine probes that query databases to make sure the physical characteristics of the workpiece match the machine’s assumptions and ensure the right match of tool and workpiece
Machines with integrated intelligence and internet connections represent the future of manufacturing. Companies have the tools they need to vastly decrease upstream product rejections and ensure the longest life for their assets.
A Bright Future for Manufacturing
There’s every reason to be optimistic about the future of manufacturing, even with the dearth of talent to fill skilled positions. Machine intelligence and sensors, plus new ways to procure essential materials and services, adds up to an industry that’s well-positioned for growth.
The content & opinions in this article are the author’s and do not necessarily represent the views of ManufacturingTomorrow
Comments (0)
This post does not have any comments. Be the first to leave a comment below.
Featured Product
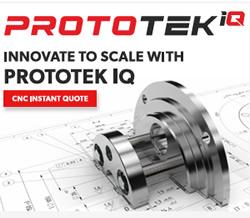