The two may seem very similar, however, several key factors set an AGV and an AMR apart. The biggest difference between the two comes down to how they move through a facility.
Warehouse Automation: Automatic Guided Vehicles & Autonomous Mobile Robots
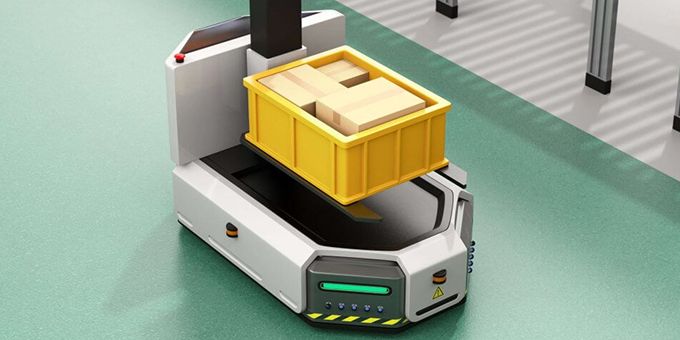
Carlicia Layosa , Product Marketing Engineer | MiSUMi
AGV’s and AMR’s may seem very similar, however, several key factors set an AGV and an AMR apart. The biggest difference between the two comes down to how they move through a facility.
AGV (Automatic Guided Vehicles) by Marta Veverica / CC BY-SA
AGVs (Automatic Guided Vehicles)
An AGV is just what the name implies, a vehicle that operates by a fixed and guided route. They are mobile robots (such as driverless trains, pallet trucks, or unit load carriers) that are, able to move independently of an operator. The way they navigate the warehouse floor depends on the type of AGV it is, generally these machines either follow markers or wires in the floor or use a combination of LiDAR (Light Detection and Ranging) Sensors, to establish routes and avoid obstacles.
AGV with Guidance System
AMRs (Autonomous Mobile Robots)
An AMR is an autonomous robot designed to self-navigate, work collaboratively with humans, offering a much smarter solution than an AGV. With an AMR, you get a flexible solution that offers easy adjustments to changes in your operational needs. Implementation of an AMR is much simpler than an AGV, as there is no need to make expensive facility modifications to automate a warehouse.
An AMR is much more sophisticated, there are many sensors incorporated and onboard computers that allow an AMR to understand its operating environment. Rather than being restricted to fixed routes, an AMR can navigate using mapping technology, allowing it to plan its own paths, travel quickly and efficiently. Also using, LiDAR (Light Detection and Ranging) Sensors, AMRs are smart enough to recognize and react to people, cars, forklifts, etc. Safely performing their jobs no matter how busy the surrounding environment and can even perform tasks like following a person, wherever they go.
TTO 1500 self-driving vehicle by M P Hennessey / CC BY-SA
The Benefits of Warehouse Robotic Systems
Increased safety
- In general, implementation of these types of systems, increase workplace safety. These systems minimize workers from performing dangerous tasks. Vision systems and laser sensors incorporated into these systems, also ensure that accidents are avoided, in and around these work environments.
Increased order and delivery times
- Robots facilitate the transport of orders to facilities, picking robots, the pallet, packaging and pricing departments, loading docks, and shipping containers. The rise of autonomous vehicles and drone delivery concepts will further reduce the delivery times of customer orders.
Better utilization of floor space
- Automating production lines reduces the work area footprint. That means that customers are free to utilize freed up floor space, for other processes or possibly expanding production lines.
Reduced warehouse logistics costs
- Increased use of robots in warehouses means a reduced need for human labor. While this is disadvantageous if you rely on warehouse logistics jobs, it is a win for companies looking to reduce their overhead costs.
Improved quality
- Warehouse robotics perform applications repeatedly and with precision every time. As a result, products are manufactured with similar specifications and processes leading to system reliability and requiring fewer repairs.
Reduced workforce burden
- As robots take over most of the physical work in warehouses, workers will move on to more fulfilling and insightful positions. Robots will also allow people who cannot physically work in traditional logistics operations to potentially gain employment in the maintenance of the units.
Reduced transportation delays
- The use of AGV’s, AMR’s, autonomous trucks, driverless vehicles, and drones, will help to reduce shipment delays due to quick analysis of delivery impacting factors, like traffic conditions, weather, etc.
Commonly used Components for AGV’s and AMR’s
- Timing Belts / Timing Belt Pulleys
- Rotary Shafts
- Cantilever Shafts
- Miniature Linear Guides
- Linear Shafts
- Ball & Roller Bearings
- Factory Frames
- Aluminum Extrusion
- Rollers
- Slide Rails
- Sensors / Switches
- E-Stop Switches
- Stack Lights
- Warning & Signaling Lights
- Timers
- Machined Sheet Metals / Machined Sheet Metal Plates
- Gussets, Angle Plates, Welded Steel Stands
- Posts and Struts
- Shaft Supports
- Bushings
- Casters
- Metal Materials
- Conveyors
- Timing Pulleys
- Cantilever Shafts
- Stack Lights
The benefits of warehouse robotics can take the load off of the workforce and allow for new opportunities in the expansion or growth of your warehouse with various MISUMI components.
The content & opinions in this article are the author’s and do not necessarily represent the views of ManufacturingTomorrow
Comments (0)
This post does not have any comments. Be the first to leave a comment below.
Featured Product
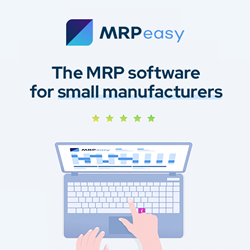