A challenge lies in that fact that every single smart device connected to the IoT generates huge amounts of data. All of this information must be processed and analyzed to successfully take advantage of the opportunities presented by Industry 4.0.
The Dynamic Duo of the IoT - Combining Cloud and Edge Processing Gives the Best of Both Worlds
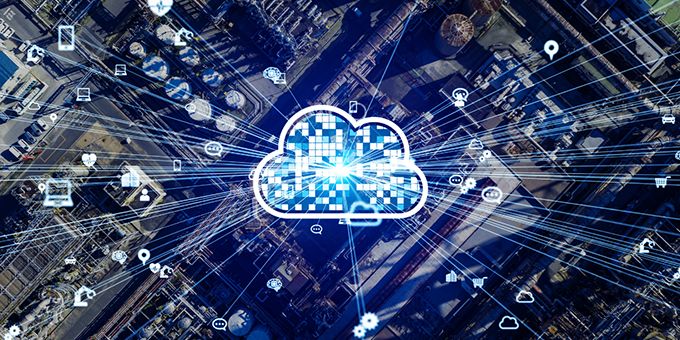
Claudia Jarrett, US Country Manager | EU Automation
Bert and Ernie, Thelma and Louise, even Butch Cassidy and the Sundance Kid: sometimes opposites attract. This old phrase not only rings true in pop culture, but in industrial data processing, too. Here, Claudia Jarrett, US country manager at industrial automation parts-supplier, EU Automation, explains how manufacturers can get the most value out of cloud and edge data servers — by bringing them together.
The internet of things (IoT) is changing the world, including the manufacturing industry. In fact, 87 per cent of businesses surveyed in Vodaphone Business’s recent IoT Spotlight Report 2020 said that the IoT is critical for their future success, while 81 per cent of adopters said they are prioritizing the IoT more highly than they did before the COVID-19 pandemic.
Given the benefits of IoT technology, it’s no wonder more and more US manufacturers are taking advantage. They including improved analytics and decision making, the ability to identify faults or issues before they occur, and more optimized, cost-effective and efficient production.
However, a challenge lies in that fact that every single smart device connected to the IoT generates huge amounts of data. All of this information must be processed and analyzed to successfully take advantage of the opportunities presented by Industry 4.0. This is where cloud computing comes in.
Up in the cloud
Over the last decade, cloud computing has become the first choice when it comes to updating data management strategies while also implementing smart manufacturing technologies. All the data gleaned from sensors around the factory is sent to the cloud, a remote data center where the information stored, managed, and processed.
There are advantages for what operators can see and control. By using a cloud-based service, manufacturers can easily manage and access their data from anywhere. This is ideal for remote-monitoring numerous sites and, of course, for the current home working trend forced by the pandemic.
With the cloud, manufacturers can also analyze their smart factory data without the need to invest in costly software license. In fact, cloud services are often run on a cost-per-use basis, which means manufacturers only have to pay for what they nee, and have a system that’s easily scalable with their business.
But there are risks to storing data in the cloud. One is network outages, which leave manufactures unable to access their data when they need it most. This is a real liability in applications where traceability is key. Take food and beverage, for instance, where downtime is not only costly but can cause the loss of otherwise-perfect batches. Another concern is security, of course —any movement of data does increases risks of cyberattacks.
Computing on the edge
This leads us to edge computing. Essentially, edge computing means moving data processing as close as possible to its source of origin. For example, a smart sensor on a robotic arm takes a reading and sends it to a server with a human machine interface (HMI) at the side of the line. There, the data can be processed immediately and decisions are made by human workers in real-time.
The major benefit of edge computing is speed, or reduced latency — the time that elapses between sending the data to the cloud, and then receiving it back on a HMI device where the information can be acted upon. The difference may only be milliseconds, but there are situations where this time makes the difference between an accident occurring, or not.
The speed of edge computing is also a plus for maintenance, predictive or otherwise. The ability to gather, process or act on data in real-time makes it is possible to more quickly identify when equipment parts need to be repaired or replaced. What’s more, manufacturers needn’t do this alone: a reliable industrial parts supplier can help source the exact part manufacturers need, whenever they need it.
Predictive maintenance and the ability to source replacement parts quickly combines with another major advantage of edge computing: a lower risk of outages. Edge computing naturally has a more distributed architecture than centralized cloud computing. Rather than all the data going to one location, the cloud, numerous edge devices can be installed around a factory to process different data segments. Therefore, it is much less likely for every edge server to simultaneously experience a failure, leaving the plant completely without access to data.
Lastly, edge computing can be implemented gradually across the plant, machine-by-machine. This would be interest to the businesses surveyed in Vodafone’s IoT Spotlight Report that have embarked on their IoT journey, as a gradual roll-out can be performed cost-effectively in accordance with the manufacturer’s own pace and needs.
Better together
Cloud and edge computing might seem like complete opposites. One processes data remotely, while the other keeps it much closer to home.
Yet, it is by implementing both cloud and edge solutions together that manufacturers can achieve a real difference, making their data architecture stronger, more secure and reliable. Data can be collected and processed on an edge server, where it is analyzed and any immediate decisions can be taken. This information can then be sent to the cloud to be stored and analyzed in an aggregated form, for such applications as machine learning.
Manufacturers that are looking to increase their IoT adoption, or are dissatisfied with their current data processing strategy, may find that cloud computing and edge solutions are a perfect duo — just like Butch and Sundance.
The content & opinions in this article are the author’s and do not necessarily represent the views of ManufacturingTomorrow
Comments (0)
This post does not have any comments. Be the first to leave a comment below.
Featured Product
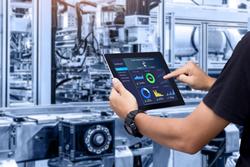