In general, dynamic micro-CT is ideal for obtaining much more complete 3D information throughout a process and provides researchers with a lab-based capacity to collect data during testing without discrete interruptions―true in situ testing.
Dynamic Micro-CT: Moving beyond 3D into 4D
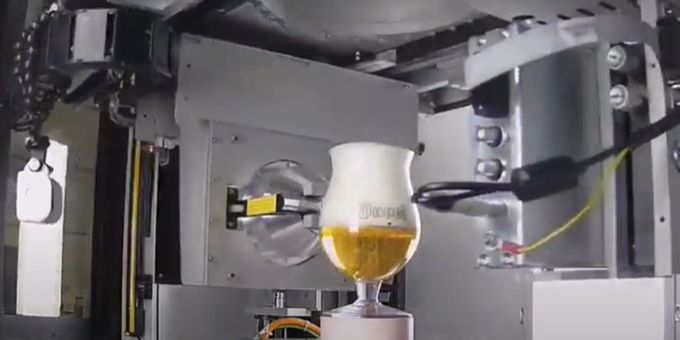
Q&A with Luke Hunter, Micro-CT Product Manager | TESCAN
Can you explain how micro-CT works and why there is such an increase in use?
Micro computed tomography, or Micro-CT, is one of the best methods for performing non-destructive three-dimensional (3D) imaging of a sample. The technique involves the collection of a large number of two-dimensional (2D) x-ray radiographs (same basic technology used for x-rays on people) of a sample at different angles, which are then reconstructed into a geometrically accurate 3D volume of the sample. Many people may be familiar with a medical “CAT” scan, which operates under the same principles, but at much coarser spatial resolution, at best 100’s of microns. Micro-CT extends spatial resolution down to single microns and below and the non-destructive nature of the technique allows for interrogation of a very broad range of material types and sample sizes.
While 2D imaging can provide a nice look at a single “slice” of a sample, the requirement of understanding the 3D relationship of complex features is becoming more essential. Additionally, the act of acquiring 2D images on the inside of a sample has traditionally required physically destroying the sample, which can introduce artifacts and does not allow for further use of the sample in its original form. The alternative of non-destructive 3D imaging with micro-CT has gone a long way to alleviate the issues with traditional “3D” imaging.
Examples of micro-CT 3D images from various application areas are shown below, in Figure 1:
Figure 1: Examples of various micro-CT images from several different application areas
I understand that TESCAN dynamic micro-CT excels in high temporal resolution for pushing the boundaries of 4D micro-CT, including Dynamic CT. Could you tell us more about 4D and Dynamic micro-CT and their advantages over conventional micro-CT?
Observing how a sample changes in 3D over time (known as 4D imaging) is a natural extension of traditional micro-CT imaging and has been performed with great success through in situ experimentation. However, due to limited temporal resolution and the resulting long scan times, lab based micro-CT imaging had been either relegated to relatively slow processes (hours to days) or needed to be performed in an interrupted nature, where the sample is not undergoing change while the imaging takes place, for example, in situ experiments involving temperature or loading. This is commonly referred to as 4D time-lapse imaging, where there are discrete breaks in the continuity of the data.
In contrast, dynamic CT, by leveraging higher temporal resolution, uses continuous data collection throughout the process, eliminating the need to interrupt processes, as well as making it possible to capture faster events where interruption is not possible (i.e., fluid flow). In general, dynamic CT is ideal for obtaining much more complete information throughout a process and provides researchers with a lab-based capacity to collect data on testing without discrete interruptions―true in situ testing.
Are there specific features of your systems which allow you to perform these types of high temporal resolution dynamic studies?
TESCAN is a pioneer in lab-based dynamic CT with systems engineered to provide the flexibility of traditional micro-CT for routine imaging needs, while also providing several essential characteristics for enabling dynamic CT. Along with optimizing standard parts of the system (x-ray source, sample rotation, and detector) for high temporal resolution, a number of other key elements are in place for dynamic CT. Specifically, “no cable wrap” continuous rotation for in situ apparatuses, in situ interfaces for simply swapping of test rigs, and unique temporal reconstruction techniques that allow users to leverage the full benefit of continuous data. The hardware and software tools allow individual scans down to a few seconds and temporal discretization near the rate of individual radiographs, which may be on the order of 100 milliseconds or better.
TESCAN developed the DynaTOM for the most complex in situ experiments, where rotation of the sample and the apparatus through multiple revolutions would not be possible, for example, in the case of flow experiments involving multiple fluids and/or gases with associated monitoring cabling. DynaTOM is a unique gantry-based system where the sample remains stationary while the x-ray source and detector rotate around, similar to the operations of a medical scanner, but with micro-CT resolution capabilities. This one-of-a kind solution is the world’s only commercially-available system of its type.
TESCAN systems have been engineered to emphasize high temporal resolution for enabling Dynamic CT. Does this mean you have had to sacrifice spatial resolution?
There are always trade-offs regarding temporal resolution, signal/noise, and spatial resolution. This is true of every measuring or imaging system. It is often the case that a micro-CT system can perform well at one aspect of imaging and poorly at others. With TESCAN solutions, we’ve created a balance to provide the best of all worlds. Our CoreTOM and UniTOM XL are multi-scale workhorse systems with temporal resolution down to a few seconds and spatial resolution down to 3 microns.
We also have an exciting new system, just recently introduced, providing a higher spatial resolution solution. UniTOM HR is the latest addition to our dynamic micro-CT portfolio and is the first micro-CT system to provide both sub-micron spatial resolution and full dynamic CT capability.
It seems like there would be a number of interesting applications for Dynamic CT and high temporal resolution imaging, can you give us some examples?
Specific to manufacturing, understanding the 3D change of a structure as it undergoes mechanical testing is an obvious area of interest. For example, in a recent demonstration we performed uninterrupted in situ compression on a number of 3D printed plastic test parts with different infill patterns. For this test we collected continuous data while the samples rotated 220 times, with temporal resolution of 5.8 seconds per rotation, resulting in detailed dynamic CT data tracking the change of the internal structures during the testing. For more information on this particular application, I encourage readers to check out an application note on the subject as well as a supplemental video.
The application note, titled “Dynamic CT Compression of Complex 3D Printed Parts”, can be found here.
The short video on the same subject can be found here.
In another example, also involving continuous compression, we looked at the behavior of an aluminum foam as it underwent testing. For this test we collected scans of about 15 seconds per sample revolution with a constant displacement rate. Some key takeaways for this example are shown in the graphic below where there is a clear change in loading behaviour at certain points during the test. If this test had been performed in an interrupted manner, the most common testing method prior to lab-based dynamic CT, it is highly unlikely we would have seen this realistic result. With the associated CT data, we analyze the tomograms around this load change and identify specific details of change; individual struts in the sample necking and failing over the course of a short time, less than 24 seconds in this case as shown in Figure 2.
Figure 2: Left - four points out of 150 during compression; Right - Detailed images at 12 second interval showing strut failure
I’ve also seen some more general-interest examples that highlight the applicability of Dynamic CT. Can you share the detail of some of these?
Of course! Dynamic CT can be used across a wide range of applications, from compression and tensile testing to multi-phase flow visualization to heating and cooling applications. As a couple of fun examples, we dove into the tasty world of food science. In one case we used dynamic CT to image the collapse of a beer foam on two different beers. In another, we watched as ice cream tragically melted―the videos speak for themselves.
About Luke Hunter
Luke Hunter is a product marketing manager for TESCAN. He has over 15 years of experience in the X-ray microscopy and micro-CT industries, as an application specialist, application manager, and solutions marketing manager. He received his master’s degree from University of California, Berkeley (Berkeley, CA USA) in Mechanical Engineering and his bachelor’s degree in Mechanical Engineering from Washington State University (Pullman, WA USA). TESCAN is a global supplier of scientific instrumentation and microscopy solutions, headquartered in Brno, Czech Republic. The company is focused on research, development and manufacturing of scientific instruments and laboratory equipment including electron- and ion microscopy, micro-CT and more.
The content & opinions in this article are the author’s and do not necessarily represent the views of ManufacturingTomorrow
Comments (0)
This post does not have any comments. Be the first to leave a comment below.
Featured Product
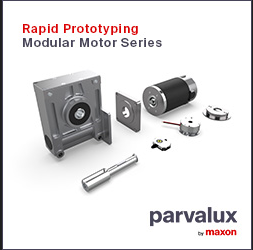