A recycling center customer was looking for a high-performance, industrial-grade Artificial Intelligence (AI) solution that could successfully function in harsh environments. The customer needed an automated solution to help identify certain materials on the recycling line.
Industrial AI and Robotics Controller System in Waste Recycle Industry
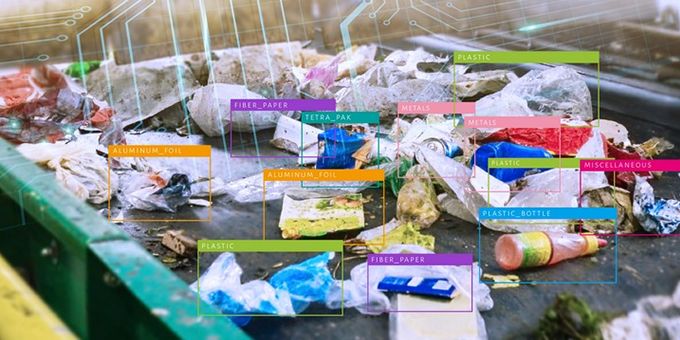
Case Study from | Advantech
Project Introduction
Governments and industries across the world are raising the standard of recycling. Massive amounts of collected waste require precise material sorting, from small sized light objects such as bottle caps, to complex material mixtures like paper, plastics and metals. There are also essential sorting considerations for domestic hazardous materials. But, with accurate waste categorizations and separation, we can prolong the lifespans of incinerators, reuse valuable materials, and reduce greenhouse gas emissions. Moreover, billions of dollars worth of recyclable materials goes unrecovered annually. Therefore, how to mitigate the impact to the environment is an important issue for government and industry to focus on.
A recycling center customer was looking for a high-performance, industrial-grade Artificial Intelligence (AI) solution that could successfully function in harsh environments. The customer needed an automated solution to help identify certain materials on the recycling line.
System Requirements
The customer needed help creating a new solution to enhance recycling performance by accelerating object identification and classification capabilities. To do this, they needed an industrial AI solution to take the place of their previous, less-effective commercial hardware solution. The new AI solution required high computing performance for processing on site. Advantech’s MIC-770 + MIC-75G20 solutions were the best option to meet the customer’s high-processing edge computing requirements.
System Description
Project Implementation
System Diagram
Featured highlights:
- High Performance system
- Harsh working environment with vibration
- Able to accommodate GPU and Plugin card
-
Fast turnaround time
-
Strong technical support
Conclusion
Advantech already had the needed hardware in its inventory and was able to work with our Channel Partner to prepare a complete solution bundle for the end user. Our inventory and Channel Partner bundle meant a quick turnaround time for the customer to get up and running. Advantech also prepared additional parts for the solution for faster repairs. By utilizing Advantech to create an automated AI solution to identify certain materials on the recycling line, the customer improved their entire process with more efficiency and accuracy. Additionally, with industrial-rated products, the end user did not need to worry about the solution functioning properly in harsh industrial environments.
The content & opinions in this article are the author’s and do not necessarily represent the views of ManufacturingTomorrow
Comments (0)
This post does not have any comments. Be the first to leave a comment below.
Featured Product
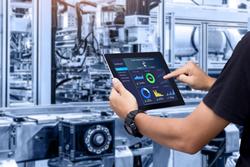