In today’s competitive business environment, customization is key. Manufacturers in all industries are expected to provide a wide range of sizes, colors, styles and assortments, and they’re finding that flexible manufacturing strategies are essential for staying competitive.
Three Ways to Improve Production Line Modularity
Article from | Omron Automation
In today’s competitive business environment, customization is key. Manufacturers in all industries are expected to provide a wide range of sizes, colors, styles and assortments, and they’re finding that flexible manufacturing strategies are essential for staying competitive.
The goal of these strategies is to minimize the effort required to change over from one product version to another. Let’s take a look at a few tactics that can help you achieve this.
Get rid of rigid elements on your line.
The first step in implementing a flexible system is to find particular elements that are highly rigid and see how they can be made modular with cutting-edge technology. One example of an inflexible element is a conveyor belt. When conveyors connect production line stations, it can be extremely difficult to rearrange the lines or add new stations.
Employing innovative autonomous mobile robots (AMRs) with integrated conveying functionality from Omron Automation Americas can dramatically increase flexibility. These robots take care of material transport needs without requiring fixed pathways or any other changes to the factory floor.
AMRs give manufacturers a much wider range of options for customizing production lines than conveyors can. In addition, you can incorporate collaborative robotic arms onto these mobile robots for a complete pick-and-carry solution.
Avoid excessive part orientation hardware.
Traditional part feeding solutions, such as bowl feeders, typically require parts to be oriented in highly precise ways prior to feeding. This means that mechanical adjustments and/or hardware redesigns are required whenever you start producing a new product, thereby dramatically increasing changeover time and costs.
For manufacturers seeking to optimize production and improve ROI, handling and sorting multiple parts on the same production machine is critical. The Omron AnyFeeder solution is an economical alternative to well-known, conventional part feeding techniques. When combined with a vision-guided robot, it exceeds the capacity of hand-tooled bowl feeders.
AnyFeeder’s flexibility in feeding small parts of various size, shape and material enables fast line changeovers and significantly reduces tooling costs, thereby delivering a crucial competitive advantage.
Take advantage of wireless technologies.
Production modularity can be improved by adopting a simple solution such as the Omron A2W Series wireless pushbutton, which simplifies wiring and maximizes layout flexibility. The extensive flexibility of A2W also enables its installation on moving parts. No batteries or recharging is necessary thanks to the self-generating power feature that’s built into the switch.
These three strategies show that modularity enhancements are available to any manufacturing company, regardless of size or budget. Start small with a wireless pushbutton, or go big with a fleet of AMRs, and watch your production soar.
The content & opinions in this article are the author’s and do not necessarily represent the views of ManufacturingTomorrow
Comments (0)
This post does not have any comments. Be the first to leave a comment below.
Featured Product
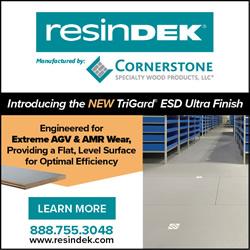