Q&A with Chris Nicholson, CEO of Pathmind. A digital twin is at once capable of simulating things that have never happened before, as well as mirroring a real, underlying physical reality and monitoring its performance.
Determining if a Digital Twin is right for your Manufacturing Operation
Q&A with Chris Nicholson, CEO | Pathmind
Tell us about yourself and your company Pathmind.
I founded Pathmind to help companies apply deep reinforcement learning to supply chain and industrial operations. We solve hard and highly complex optimization problems in those sectors, which traditional tools can't touch.
A lot of companies in supply chain and manufacturing face economic changes and need to increase the resilience of their operations. Pathmind's AI helps them do that.
Previously, I was the CEO of Skymind, an AI company focused on open-source deep learning. And, before that, I led communications and recruiting for FutureAdvisor, a Sequoia-backed Y Combinator startup that used algorithms to manage investments. FutureAdvisor was acquired by BlackRock in 2015 for $200 million.
What is a digital twin? How does it differ from a simulation – if at all?
"Digital twin" can mean a few different things, and those definitions have different functional repercussions.
We think of digital twins as software that is both a tool for thought and a tool for action. That is, a digital twin is at once capable of simulating things that have never happened before, as well as mirroring a real, underlying physical reality and monitoring its performance. Traditionally, those two capabilities have been separate, because they have very different requirements and specs.
Simulations have helped people explore what-if scenarios as a tool for thought, while various production software systems such as ERP and supply chain management software and manufacturing execution systems have served as tools for action in various contexts. The latter are controlling real systems, real machines, real flows of goods.
How can a manufacturing business determine if a digital twin strategy is right for them?
A business should first have a data collection strategy implemented, which allows it to track events and metrics in its physical plant. If your physical system is not wired up to collect data, and you are not storing that data some where to query it, then you are not yet ready for a digital twin to replicate the whole system. Back up and figure out what you want to measure and achieve first, then build a system to collect and store the data.
What kinds of what-if questions can be answered using digital twins?
You can answer three different kinds of questions with digital twins:
- What happens to my KPIs when the environment of my system changes; that is, how does my factory perform when there is a supply shock?
- What happens within my factory when I make different decisions? In this case, AI can help explore different action paths so you can see what leads to the best outcomes.
- What happens to my outcomes when I design my system differently? The design stage comes before exploring action paths or the impact of environmental changes. It's really about seeing, for example, how your delivery times change if you shift the location of your distribution centers, or how your throughput changes if you add a processing station to your shop floor.
Can you share some of the most interesting digital twin use-cases you’re seeing in manufacturing?
Digital twins are used to replicate physical systems such as groups of assembly lines, groups of processing stations on a factory floor and fleets of AGVs/AMRs navigating those factory floors. Those digital twins are usually used to maximize throughput and safety, while minimizing downtime. A common use-case would be scheduling and routing items and jobs through machines and processing stations. With AGVs, the digital twin could be used to route them from one location to another as they carry items to be processed.
Who and what does it take to make a digital twin operational? Are new hires required?
Digital twins are usually built with dedicated software, say simulation software. Specific personnel with specialized skills need to use those tools in order to build, update and monitor digital twins. These people often occupy the role of simulation modeler or industrial engineer. Depending on the company, sometimes current team members can pick up those skills, other times those people need to be hired.
What are some of the biggest hurdles for a company in implementing digital twins?
The biggest hurdles to implementing a digital twin is ensuring that you have built a valid digital replica of your physical, and then maintaining that replica as the underlying physical system changes. This is not a “one-and-done" task. Digital twins do not update themselves automatically. Domain experts need to check the twin against the underlying physical system to ensure that the logic and structure is the same.
How do you see digital twins and AI improving manufacturing going forward?
A digital twin is very useful for testing optimization strategies for your physical plant. That is, if you want to improve the efficiency of your operations, a digital twin can help you surface strategies to do that. We think they will be more and more widely implemented in manufacturing, as part of the digital transformations that will accompany industry 4.0, 5G networks and robotics being rolled out on factory floors.
About Chris Nicholson
Chris Nicholson is the founder of Pathmind, an AI startup that applies deep reinforcement learning to supply chain and industrial operations. Pathmind was founded to help businesses handle deep economic change and increase the resilience of their operations with AI. Chris oversees the company’s strategic vision and day-to-day execution, driving innovation and growth for Pathmind’s technology platform, and optimizing performance in warehouses and on factory floors as part of the digital transformation of business.
The content & opinions in this article are the author’s and do not necessarily represent the views of ManufacturingTomorrow
Comments (0)
This post does not have any comments. Be the first to leave a comment below.
Featured Product
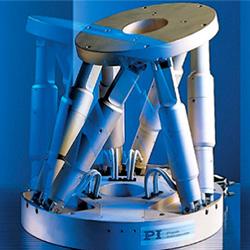