Throughout history, there have been industrial applications that require a load or force measurement within a system that involves either linear electric or hydraulic smart actuators.
Precise Load and Force Measurement in Smart Hydraulic and Electric Actuators
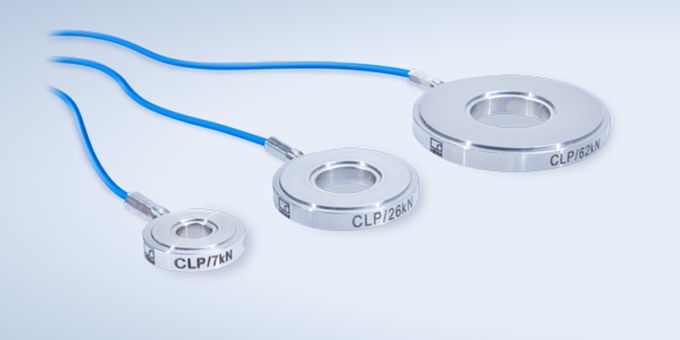
Article from | HBM
Hydraulic Smart Actuators
These actuators normally monitor cylinder and system load by measuring the fluid pressure using a pressure transducer. While this method provides the operator with an understanding of the fluid pressure levels within the system, there is inherent error in measuring the force that the piston applies. Variances in fluid temperature, cylinder size, friction, piston/rod seal geometry, and transverse loads collectively can negatively affect load calculations by as much as 20% or more.
Electric Smart Linear Actuators - Open Loop
An open loop measurement system has been used by controlling the voltage and current sent to the actuator rotational servo motor. This method of force value calculation can have error percentages over 15-20%. Errors can occur due to both friction and the condition of the actuator.
Electric Smart Linear Actuators – Closed Loop
Various industries are increasingly requiring much more precise measurement of load and force within their actuator systems. This can be accomplished using a strain gauge based load cell method of force measurement creating a Smart Linear Actuator. Placement of strain gauge based load cells either externally or internally within the actuator can provide precise force measurements within an accuracy of under +/- 1%. Rugged load cells can measure the force an actuator applies within the system or an external force acting upon the system. Various load cell outputs of mv/V, 4-20mA, 0-5VDC, J1939 CANbus, etc. send a signal that then allows the increase of power to the electric actuator servo motor or the hydraulic valve to properly adjust to the required level of force.
OEM Sensors from HBM
At the OEM level, HBM can provide highly custom, fully integrated load cells designed to fit into actuators housing or anywhere within the mechanical system. This gives OEMs greater flexibility to have the load cell designed around their system and to their desired specifications. The list of applications that require precise force and load measurement is rapidly growing, and for various reasons.
In manufacturing, we see advancements in material handling, molding, die-cutting, stamping and riveting pushing for a higher level of accuracy. Synchronized load balancing can be achieved in process automation through the use of force measurement using load cells.
Off-highway industrial vehicles are becoming more intelligent along with providing a higher level of safety. This includes a higher level of control for agricultural equipment such as planting downforce, grain tank balancing, or safety overload condition monitoring on scissor lifts and crane hoists.
Within medical facilities we see advancements in patient care with intelligent control of hospital beds, stair lifts, and lift tables.
As advancements in a wide range of industrial applications are made, there will be a greater need for precise load and force measurement where electric and hydraulic smart actuators are being implemented. HBM is ready to partner with OEMs to design and manufacture custom load cell solutions ready to handle tomorrow’s toughest challenges.
The content & opinions in this article are the author’s and do not necessarily represent the views of ManufacturingTomorrow
Comments (0)
This post does not have any comments. Be the first to leave a comment below.
Featured Product
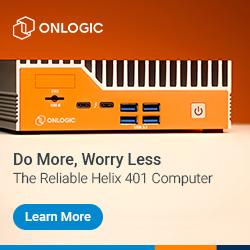