Supply shortages, cybersecurity threats, and a lack of worker digital skills are the top three challenges faced by manufacturers, according to an IDC survey in November 2021.
The New Supply Chain Issues Can’t Be Handled the Old Way
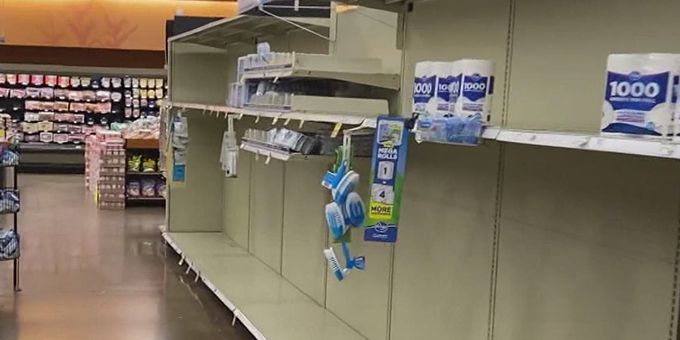
Jan Burian, Senior Director, Head of IDC Manufacturing Insights EMEA | EMEA
Supply shortages, cybersecurity threats, and a lack of worker digital skills are the top three challenges faced by manufacturers, according to an IDC survey in November 2021.
These challenges overlap to some extent. However, and most importantly, they are all linked to one massive problem manufacturers are now confronting: disrupted supply chains and factory operations.
Let’s paint the bigger picture. A recent McKinsey survey revealed that in last 12 months, companies have reacted to supply chain disruptions by increasing their inventories of critical products, implementing the dual sourcing of raw materials, and boosting inventories all along the supply chain.
Let there be no doubt: As the two surveys indicate, shortages are crippling supply chains.
To resolve this situation, or at least significantly improve it, we must go way beyond traditional approaches like boosting inventories or multi-sourcing supplies. These old approaches could even be regarded as prolonging the problem. Organizations should not assume that because they have taken these steps, they have their supply chain risks under control.
In today’s global economy, supply chains face issues similar to those of OEMs. In the long term, inventory increases are not sustainable in a world of minimum safety stocks in the distributed supply chain network. Organizations also continue to prioritize minimizing the financial resources tied up in physical inventories.
Devil in the Details
The use of digital technology as an enabler of supply chain resiliency is inevitable. Supply chain digital platform networks have been available for some time. But what makes such systems work effectively is the presence and vailability of reliable data.
The more organizations share data and actively participate in the network, the greater the transparency, flexibility and sustainability of the results.
IDC predicts that in 2024, to improve long-term supply chain profitability, 70% of manufacturers in global supply chains will invest in software tools to support sustainability and circular economy business models.
This, of course, brings up challenge #2: cybersecurity. As we move from direct customer-supplier connections to platform-enabled sourcing/on-demand manufacturing models, the IT environment becomes even more vulnerable.
Securing end-to-end visibility across the value chain requires the meshing of IT systems and physical devices. There are heterogeneous and legacy systems. Networks include diverse assets, often including multiple connected architectures. Yet converging IT and operational technology (OT) injects even more complication into an already complex IT infrastructure.
Supply chain network stakeholders must take a comprehensive approach to hybrid and multi-cloud permissions management — and they should leverage advanced analytics to keep track of the identities on the network.
But here arises challenge #3: the lack of digital skills among workforces. It’s not news that working in a digital environment requires skills and experience. The question is to what extent organizations succeed in dealing with this challenge. Upskilling/reskilling are frequently mentioned approaches.
However, rapidly upskilling/reskilling on a mass scale is unrealistic for most large manufacturing organizations. The time/resources commitment is simply too large. This is where IT vendors, device OEMs, and app builders play a key role. They are increasingly providing workforces with tools that can be used intuitively or that are AI-based. In many cases, workforces need very little digital experience to use these tools efficiently.
Utilizing customized, ergonomic digital tools first requires their creation, either in-house or via a third-party developer. Utilizing low-code platforms will become critical to deploying such tools rapidly.
IDC predicts that in 2025, more than 60% of organizations will rely on low-code platforms and tools to build smart custom applications that can support connected manufacturing needs. Use of low-code tools is expected to reduce application deployment costs/time by up to one-third.
Implications
The scope of the supplies shortages companies are now facing is beyond the professional experience of most supply chain managers. Handling the aftermath of disruptions through proven methods and approaches seems logical. Unfortunately, it is insufficient.
Short-term actions should remain short term. Over the long term — in the “new normal” world of the pandemic that we find ourselves in — bringing transparency to supply chain complexity through market intelligence tools, supply chain control towers, and extensive collaboration with supply chain stakeholders and technology vendors will be winning combinations.
Supply chain transparency is achieved via extensive connections between logistics providers, warehouse operators, and other service providers (e.g., last-mile delivery). Of course, each new link in the chain increases vulnerability to cyberattacks. A tight focus on IT and OT cybersecurity is crucial for the manufacturing organizations that orchestrate these ecosystems.
The human factor makes it all come together. It is necessary to upskill/reskill the workforce, both blue and white collar, to make these systems function optimally. Organizations should ensure this enhancement maximizes the use of digital tools and solutions that enable intuitive, user-friendly control by the human operator.
Bottom line: Work with technology vendors to ease the transition to the converged human-digital interaction environment!
The content & opinions in this article are the author’s and do not necessarily represent the views of ManufacturingTomorrow
Comments (0)
This post does not have any comments. Be the first to leave a comment below.
Featured Product
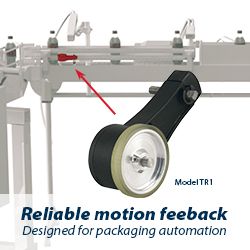