Adding automated decision-support to visual inspection helps speed inspection rates, improve end-to-end product quality, and provides more qualitative product evaluation to ensure manufacturing processes are repeatable and traceable.
Bringing AI to Electronics Assembly Inspection
Article from | Pleora
Visual inspection is the oldest method for quality control. The human eye has proved to be excellent at detecting cracks, deformities, scratches, missing components, and other errors and issues that can impact quality.
However, manufacturers have a lot to lose if they mistakenly send poor quality products to their end-customers.
Humans versus Machines
Humans excel at sensing differences through sight, touch, and even smell depending on the product. We can distinguish subtle flaws, variations or differences and can adjust when faced with unpredictability. Humans are also easily trained. We learn by example and can adapt for new products or requirements.
However, technology brings speed, accuracy and repeatability that we simply can’t match as humans. And despite some human advantages, we also suffer from a number of limitations. Our eyes can be easily tricked, making us unreliable. Try and count the black dots in Figure 1. A machine vision system makes decisions faster, thanks to higher processing speeds and ever-expanding memory capacity. Automation can be programmed to be unbiased and consistently accurate.
Figure 1: Humans are very good at inspection. We can use our senses and are quick to learn and adapt. But we can also be easily fooled. Try and count the black dots in this image.
Unfortunately, unlike machines we get tired, bored, distracted, and can make subjective decisions. As a result, most manual inspection tasks typically exhibit error rates of 20-30 percent, primarily due to human error. Typically, these errors are related to missing a defect, incorrect assembly, or a “false positive” where an operator identifies an issue that does not exist.
Considering these error rates, and the resulting higher costs due to waste and manufacturing downtime as well as the impact of poor product quality on brand perception, there’s an obvious opportunity to leverage technology advances to help human inspectors.
AI-Powered Decision Support
Adding automated decision-support to visual inspection helps speed inspection rates, improve end-to-end product quality, and provides more qualitative product evaluation to ensure manufacturing processes are repeatable and traceable. As end-markets increasingly demand more customized products, human inspection can sometimes be more cost-effective and adaptive than automated processes for on-demand and low volume manufacturing.
New visual inspection systems leveraging advances in no-code algorithm development and edge processing platforms make it easier and more cost-effective for manufacturers to add AI decision-support for in-progress and finished goods. These systems provide pre-packaged inspection skills that can be easily customized and retrained for specific requirements, including verifying components, inspecting labelling, checking assembly, and digitizing work instructions.
As a fully integrated tabletop system, the operator can use the camera, edge processing, and display to acquire images and create an AI model. They don’t need to switch between cameras, PCs or cloud-based systems; making the system easy-to-use, highly cost-effective, and all in a smaller footprint.
Figure 2: A fully integrated visual inspection system includes a camera, display, edge processing, and pre-packaged common inspection skills, while no code development platforms enable easy customization for unique requirements.
No Code Advantages and Simple Training
One of the most significant hurdles for manufacturers considering AI-based inspection is algorithm development. There is a perception that it requires specialized skills, or expensive consulting, to deploy the technology for manufacturing applications.
No code block-based platforms let any end-user easily design AI and computer models to automate tasks, such as visual inspection, digital work instructions, automated counting and measurement.
For visual inspection systems, pre-packaged skills for common requirements such as image compare and image save can be quickly trained and deployed, without requiring programming language expertise. With just one good image (a “golden master”) the system is trained to distinguish good from bad or pass/fail. More experienced developers can use the software platform to customize pre-packaged plug-ins for custom requirements.
Figure 3: Image Compare skills help guide an operator during work-in-process and final assembly inspection steps.
Electronics Inspection and Image Compare
One of the fastest ways manufacturers can add AI decision-support into processes is with image compare. The visual inspection system compares the manufactured product with the “golden master”, and visually highlights differences and deviations on a monitor.
DICA is an electronics contract manufacturer located just outside of Ottawa, Ontario that services an expansive list of healthcare, industrial controls, telecommunications, security, and digital imaging companies located in “Silicon Valley North”. The company specializes in high quality electronic assembly services for the small-to-medium volume market.
Figure 4: DICA is a specialized electronics manufacturer that incorporates AI-based vision inspection tools in its quality processes.
Serving a high-value, lower volume market can pose inspection challenges for the company, as not all products are well-suited to automated processes. As a result, a number of products are primarily inspected by human operators. The company prides itself on its exemplary record for product quality, and views the automated visual inspection system as a method to add decision-support for its inspectors.
Automated image compare capabilities are used to match the approved layout and final production for electronic assemblies. The system quickly compares the placement of components on the circuit board, and highlights differences and deviations for the human inspection before it moves to the next step in the manufacturing process or to final packaging.
The system is also used by DICA for quality checks on incoming components from suppliers. In addition, the manufacturer uses the system to capture and save an image of every printed circuit board. This data is shared with traceability systems for inventory and shipment management and batch tracking, as well as other business processes including root cause analysis for defects.
With its intuitive, step-by-step process, the Image Compare Plug-in needs just one known, good image for training. DICA operators and quality control staff have trained multiple Image Compare plug-ins to inspect different products. The operator simply chooses the correct plug-in to use with the product to be inspected, and the visual inspection system automatically highlights any differences of deviations on a visual display. The operator can adjust the sensitivity as required to inspect different levels of components on the board.
For the manufacturer, the visual inspection system offers many valuable benefits:
• Reduces subjective decision-making for the human operator, especially over a long shift, where the system ensures consistency and accuracy.
• Cost-savings, as errors can be detected during different phases of production.
• The scalable system is quickly trained with images of “good product” for multiple product lines. An operator or quality manager can train the system, with no programming skills required.
• It’s faster to train employees for inspection requirements any time a new product is added, or new employees to better understand the difference between good and bad products.
• Image save helps reduce time, cost, and risk and enables better traceability processes if a potential error is detected in the field.
Changing Visual Inspection
Adding decision support and automating processes for visual inspection helps ensure consistency. The technology can aid a tired operator at the end of a shift, a new employee who is unsure what makes a product “good” or “bad”, or simply speed the inspection process. It lets manufacturers take advantage of new technologies for processes where automation is cost prohibitive, including low volume production.
As part of a wider Industry 4.0 initiative, automation and decision-support tools for visual inspection can help provide real-time process visibility to drive data-based decisions.
Ed Goffin is marketing manager with Pleora Technologies a leading provider of AI and real-time sensor networking products for industrial automation, security, and medical imaging applications. To learn more about Pleora’s AI Solutions visit pleora.com/ai-for-quality-inspection/.
The content & opinions in this article are the author’s and do not necessarily represent the views of ManufacturingTomorrow
Comments (0)
This post does not have any comments. Be the first to leave a comment below.
Featured Product
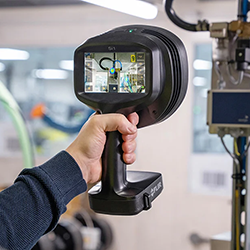